-
Reduce downtime
Stay ahead of issues with a proactive preventive maintenance plan, and respond swiftly when unexpected emergencies arise.
LEARN MORE -
Increase productivity
Simplify work order management and supercharge efficiency with intuitive, collaborative software your team will love.
LEARN MORE -
See every work order
Track open and past work orders to ensure compliance and gain full visibility into tasks at the individual team member level.
LEARN MORE
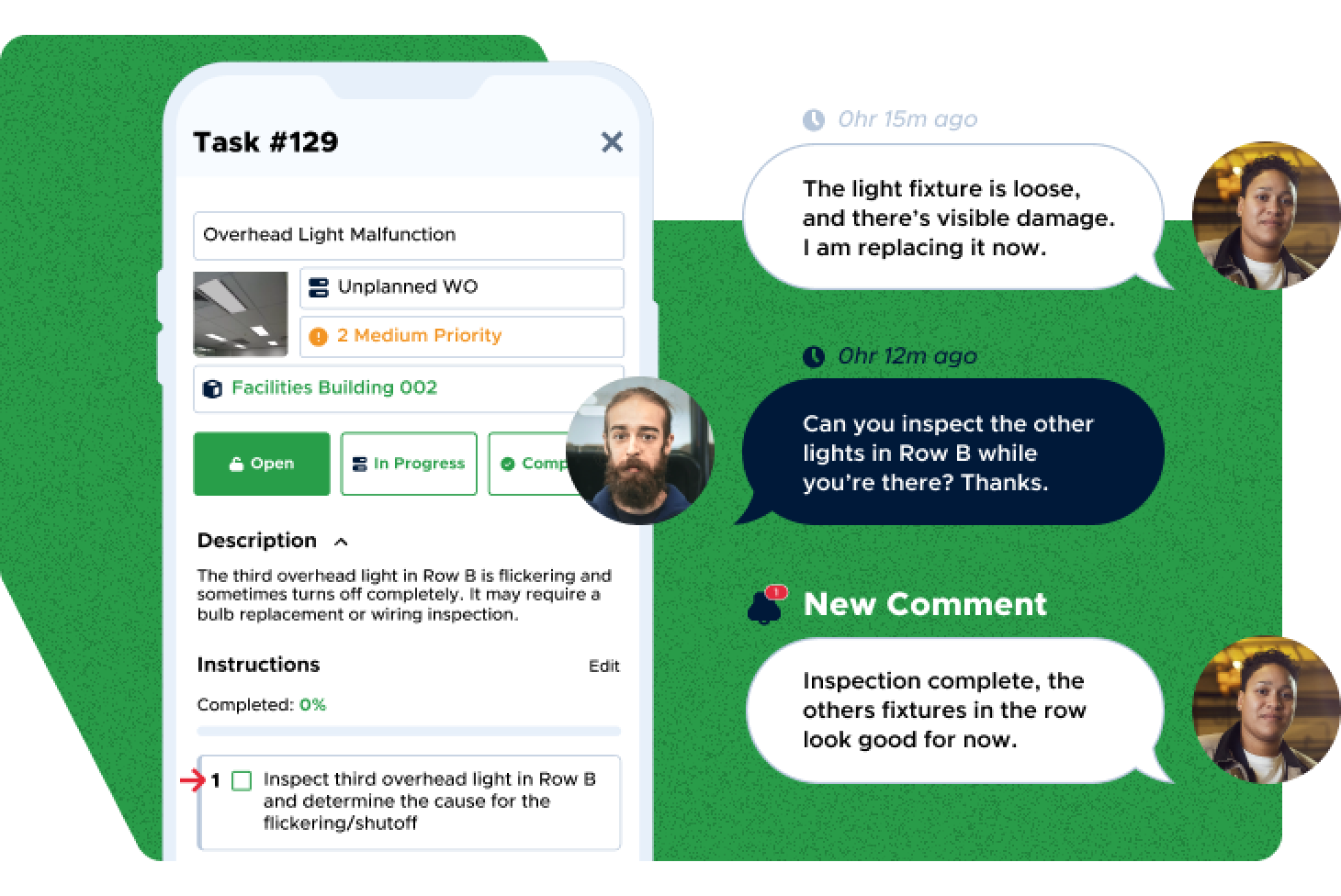
The mobile CMMS app for on-the-go teams
Work smarter with a mobile maintenance app that keeps your team connected and productive, wherever they are.
- Automate workflows and updates with streamlined work order requests
- Stay organized with real-time access and communication
- Boost productivity with offline mode, mapping, and QR code scanning
Instant work order request system
No more lost tickets, daily interruptions, or duplicated work. Anyone can scan a QR or bar code, or visit a URL to submit an issue.
- Access requests instantly on any device
- Keep everything organized with robust configurations
- Save time with customizable workflows and automated updates
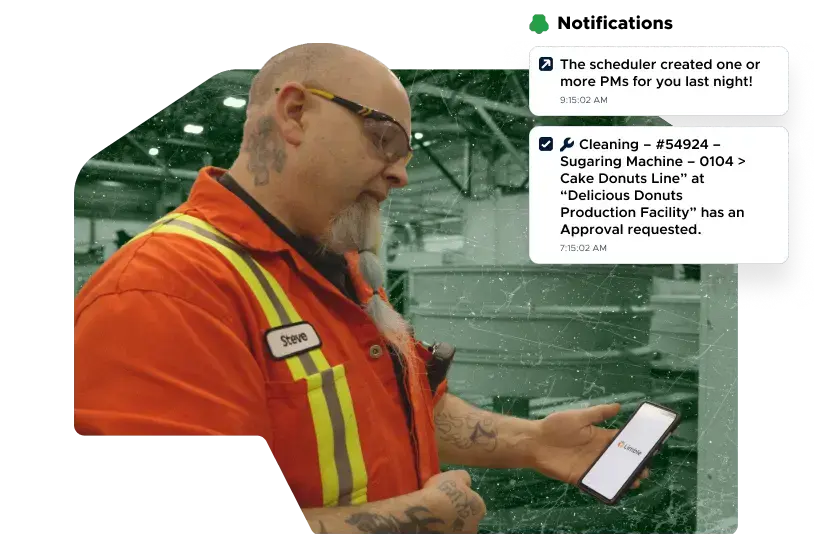
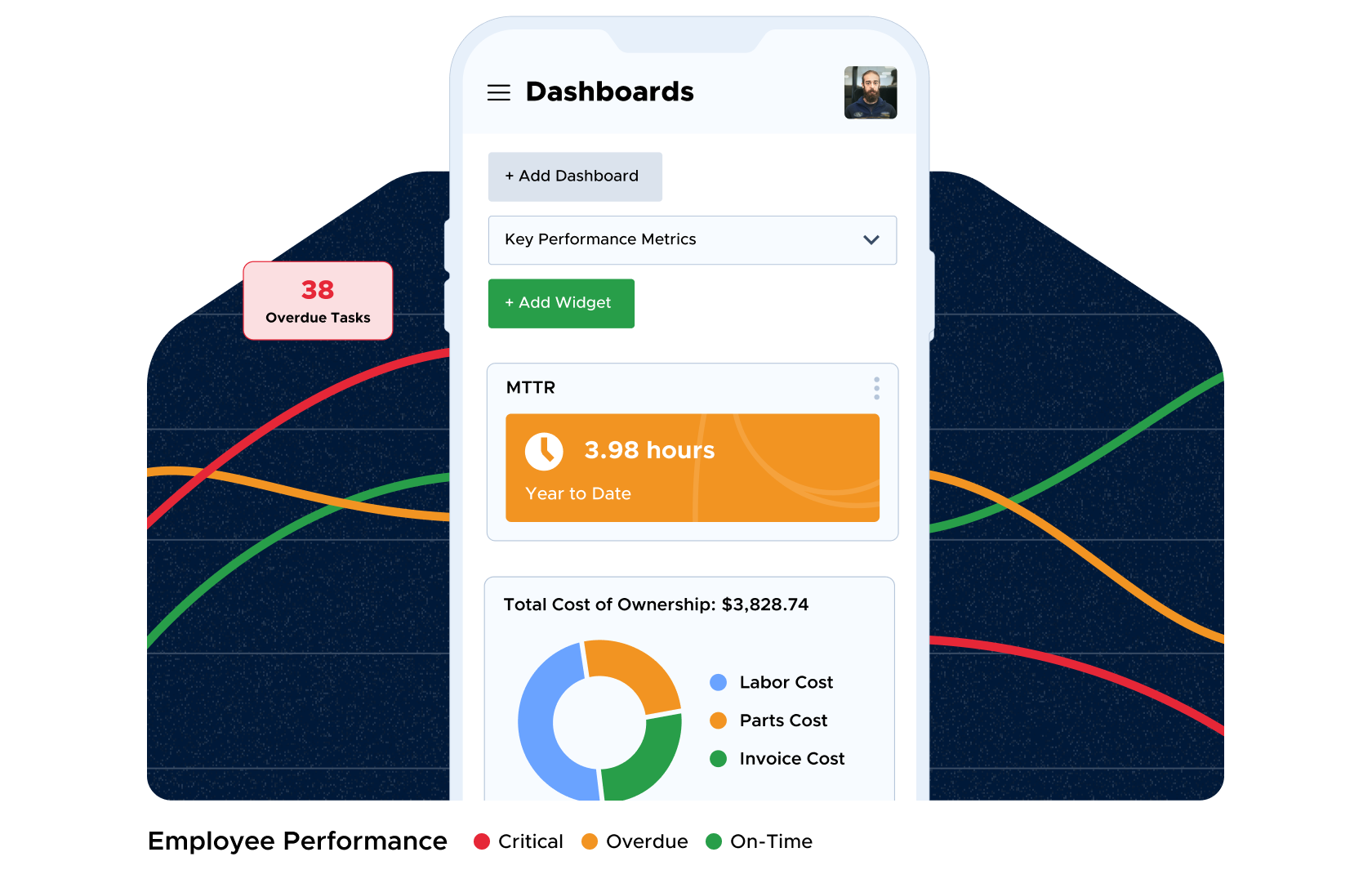
Key information at your fingertips
Quickly look up information about work orders, assets, parts inventory and more; all from your mobile device.
- Search assets, parts, POs, and vendors
- View maintenance history for easier troubleshooting
- Scan QR codes for instant info
- Access repair manuals and warranties
Get control of your inventory
Organize your spare parts to know what is in stock, where it is, and when it will run out to ensure your technicians have the parts they need to do the job.
- Get alerts for low parts
- Scan barcodes/QR codes for stock info
- Track unused parts and stale items
- Use cycle counts for inventory accuracy
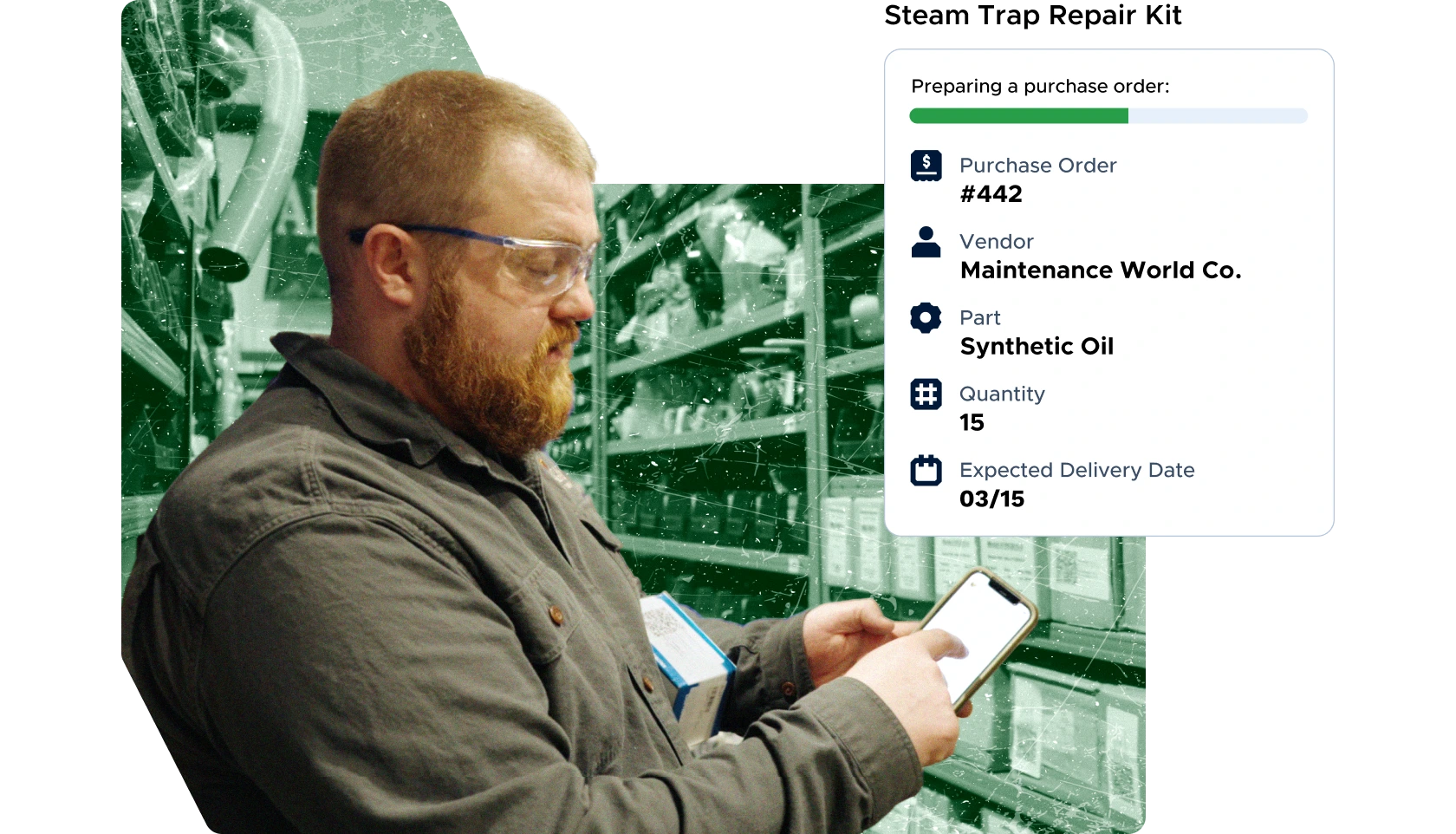
"Everyone picked it up quickly and suddenly all our maintenance requests that had been up on the wall were now on our phones and laptops. It simplified the operation for absolutely everyone here"
AJ Popovic Maintenance Technician VIEW CASE STUDYFAQ for a mobile CMMS app
How does a mobile CMMS software improve maintenance management?
Can maintenance teams track work requests and schedules on mobile devices?
Yes, Limble’s mobile CMMS software allows teams to create, update, and track work requests, maintenance schedules, and asset performance from anywhere. Push notifications ensure technicians stay on top of critical tasks and complete work without delays.
Does a mobile CMMS support inventory management?
Many mobile CMMS solutions include inventory management functionality, helping teams track spare parts, automate reordering, and ensure they have the right materials for their maintenance needs.
How can different industries benefit from a mobile CMMS?
- Manufacturing: Monitor asset health, schedule preventive maintenance, and reduce unplanned downtime.
- Healthcare: Ensure compliance by managing medical equipment maintenance with checklists and alerts.
- Hospitality: Streamline facility maintenance with work requests and real-time tracking.
- Facilities Management: Improve asset performance with mobile dashboards and automated reporting.
- Utilities & Energy: Track remote assets, inspections, and maintenance schedules via smartphones.
Does a mobile CMMS provide real-time reporting and dashboards?
Yes, the best CMMS software offers real-time dashboards and predictive maintenance insights, giving teams instant visibility into asset information, work orders, and maintenance schedules to make data-driven decisions.