The U.S. Food and Drug Administration (FDA) is the agency that regulates the manufacture, marketing, and distribution of foods, drugs, cosmetics, biological products, and medical devices in the United States. Today, the FDA operates as part of the Department of Health and Human Services (DHHS) and plays a critical role in protecting public health by ensuring the safety, quality, and efficacy of these consumer goods.
Manufacturing and FDA medical device regulations
The Food and Drug Administration was established in 1906 and granted much of its enforcement authority by the 1938 Federal Food, Drug, and Cosmetic Act.
Exercising this authority requires a comprehensive regulatory apparatus. Regulatory standards were codified into federal law as part of the Code of Federal Regulations (CFR). CFR Title 21 (or 21 CFR) is the section of the Code articulating the rules concerning the FDA as well as agencies under the purview of the FDA including the Center for Devices and Radiological Health (CDRH) and any Institutional Review Boards (IRB) formally established and designated by the FDA.
The manufacture of medical devices falls within the scope of these Title 21 rules. This means that any organization or business involved in the manufacture of medical devices must understand and comply with the FDA medical device regulations outlined in 21 CFR.
Understanding FDA regulations on medical devices
Manufacturers of medical devices have a responsibility to ensure the safety and effectiveness of their output. FDA regulations provide strict and detailed rules on how to do so.
Overview of FDA regulations for medical devices
The FDA is charged with enforcing many regulatory controls, including:
- Medical Device Classification, with Class I devices (e.g., elastic bandages, examination gloves) presenting the lowest risk, Class II devices (e.g., powered wheelchairs, infusion pumps) presenting moderate risk, and Class III devices (e.g., pacemakers, heart valves) indicating relatively high-risk devices
- Premarket Requirements, which include Premarket Notification (510(k)), wherein manufacturers must demonstrate that the device has substantial equivalence to an existing and approved device, and Premarket Approval (PMA), wherein Class III devices must undergo clinical studies and applicants must present clinical data for rigorous review
- Quality System Regulation (QSR), which requires manufacturers to establish their own systems for ensuring adherence to all FDA requirements relating to medical device design, packaging, storage, installation, servicing, and more
- Device Labeling Requirements, including the provision of adequate directions for use, warnings, and precautions
- Post-Market Surveillance, including Medical Device Reporting (MDR), tracking, and post-approval studies
Implementation of FDA Regulations
The FDA uses several mechanisms and strategies to communicate, implement, and enforce regulations for medical device manufacturers.
- Establishment registration and device listing ensure accountability by requiring manufacturers to register operations and list devices with the FDA.
- Good Manufacturing Practices (GMP) provide guidelines for what must be included in each manufacturer’s QSR (e.g. process validation, quality audits, maintenance SOPs, etc.).
- Inspections and audits provide the FDA with a first-hand look at manufacturing facilities and help the agency determine how effectively individual operations are meeting regulatory requirements.
- Enforcement actions such as warnings, fines, mandated recalls, product seizures, legal injunctions, and criminal prosecutions provide the FDA with the authority to penalize manufacturers who violate regulations.
- Guidance documents can provide detailed information on particular aspects of medical device regulation to help manufacturers understand and comply with regulatory requirements.
Importance of FDA regulations
Medical device manufacturers are a critical part of the healthcare ecosystem. While some medical devices like cotton swabs and rubber gloves may carry minimal risk, device types such as pacemakers and defibrillators carry both serious risk and potentially life-saving importance. This reinforces the important role that FDA regulations play in:
- Protecting patients from unsafe and ineffective medical devices
- Ensuring devices perform effectively, as intended, and in line with claims from manufacturers
- Monitoring adverse events and maintaining strict oversight to prevent widespread harm from defective devices
- Fostering confidence in the reliability of medical devices and the credibility of the companies that manufacture them
- Using administrative, legal, and financial consequences to punish and prevent the market participation of bad actors
What is 21 CFR?
As noted above, 21 CFR is the section of the Code of Federal Regulations that relates to the roles, responsibilities, and legal mandate of the FDA as well as the Drug Enforcement Administration (DEA). 21 CFR provides a critical legal and regulatory framework for oversight of the food, drugs, cosmetics, biological products, radiological equipment, and medical device industries in the U.S.
This framework has a direct impact on maintenance work, providing a number of rules and conditions to which maintenance programs must adhere. Below, we highlight several key provisions of 21 CFR with direct relevance to maintenance work.
- Quality System Regulation (QSR) (21 CFR Part 820) must include conditions for the maintenance of equipment used in the manufacturing process.
- Good Manufacturing Practices (GMP) (21 CFR Parts 210-211 for drugs and Part 820 for devices) require maintenance teams to keep manufacturing equipment in clean and operational condition and to document tasks completed in connection with these responsibilities.
- Electronic Records and Signatures (21 CFR Part 11) specifically addresses the criteria under which the FDA considers electronic records and electronic signatures trustworthy, reliable, and equivalent to paper records and handwritten signatures.
- Facility requirements conditioned by 21 CFR include regulations dictating how manufacturing facilities and systems (such as HVAC, plumbing, ventilation, etc.) must be designed and maintained to ensure a controlled environment.
- Documentation and recordkeeping rules conditioned by 21 CFR include requirements for the documentation of schedules, procedures, and repairs, and provide parameters for audits and inspections.
- Training for maintenance personnel is central to ensuring a comprehensive understanding of the standards dictated by 21 CFR and implementing the proper procedures for compliance.
21 CFR Part 11
21 CFR Part 11 outlines the FDA’s rules and regulations relating to the creation, modification, maintenance, archiving, retrieval, and transmission of electronic records and electronic signatures.
Key provisions of Part 11 include:
- Electronic records rules for conducting validation, keeping audit trails, retaining records, and controlling access
- Electronic signature requirements including required signature components, identity verification conditions, and rules around the use of biometrics
- Procedures and Documentation including delineation of Standard Operating Procedures (SOPs), training in the implementation of these procedures, and detailed documentation of all associated processes, training, validation efforts, and operational procedures
21 CFR Part 820
21 CFR Part 820 outlines the conditions medical device manufacturers must adhere to when developing internal quality system regulations (QSR). Part 820 provides rules to ensure safe, effective, consistent, and high-quality production of medical devices.
Some key provisions of Part 820 include:
- General provisions for developing an internal quality policy and a plan for implementing this policy
- Design controls including a development plan, input requirements, and intended output
- Document controls ensure documents are approved, distributed, and maintained properly, with controls to prevent unauthorized changes
- Purchasing controls for evaluating and selecting suppliers as well as maintaining records of their ability to meet specified requirements
- Production and process controls including ongoing monitoring, process review, and validation
- Corrective and Preventive Action (CAPA) systems for investigating and addressing the root causes of non-conformities
- Labeling and Packaging Control ensuring the accuracy, consistency, and traceability of products
- Handling, Storage, Distribution, and Installation procedures for products throughout their lifecycle
Additional provisions of 21 CFR 820 include rules for recordkeeping, servicing procedures, statistical evaluation techniques, and more.
Maintenance in medical device manufacturing
Maintenance teams play a critical role in keeping businesses compliant with FDA regulations and promoting consumer safety. This is especially true in the medical device manufacturing sector, where consistency, compliance, and quality control can have a direct impact on the health and well-being of patients and caregivers alike.
Maintenance personnel perform many key responsibilities in alignment with FDA regulations including:
- Preventive maintenance (PM) activities such as inspection, cleaning, lubrication, calibration, testing, and preemptive parts replacement across the total product life cycle
- Corrective maintenance activities including rapid response to malfunctions and breakdowns as well as strategies for the minimization of downtime
- Validation and qualification of equipment installation, operation, and performance, as well as periodic reassessment
- Detailed recordkeeping of all maintenance activities, including preventive and corrective maintenance actions, calibration schedule, and validation efforts
- Compliance with Quality System Regulations (QSR) including adherence to Standard Operating Procedures (SOPs) and support of internal and external audits
How does maintenance technology support compliance in medical device manufacturing?
A CMMS platform can be particularly valuable for medical device manufacturers working to simplify adherence to FDA medical device regulations. The right CMMS solution can make it easier to implement a compliance program and more cost-effective to stay compliant with 21 CFR provisions. This, in turn, can spare your organization the costs and consequences of non-compliance.
Among the CMMS features that can be particularly helpful in keeping your organization compliant are:
- Automated maintenance scheduling
- Detailed recordkeeping
- Comprehensive audit trails
- Preventive asset management tools
- Enhanced quality control
- Integration capabilities
- Mobile accessibility
- Advanced performance metrics
- Continuous improvement
By leveraging a leading-edge CMMS software like Limble, organizations can improve the efficiency, effectiveness, and compliance of their maintenance operations.
Want to be sure that your organization is in full compliance with current federal regulations? Download our 21 CFR Compliance Toolkit today to see what sets Limble’s security features apart and prepare to ace your next audit.
Free 21 CFR Compliance Toolkit
Our toolkit is chockful of useful information to give direction to your maintenance team as it navigates complex 21 CFR rules.
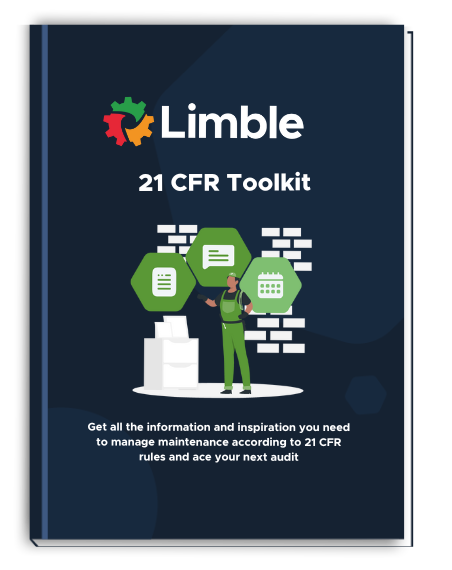