Since you can never eliminate the possibility of an emergency, it is always a good idea to set up some procedures and protocols in place that will speed-up your response, minimize safety risk, and prevent collateral damage.
Here’s a short 4 step outline on how to set up emergency maintenance procedures.
#1) Define and identify your emergencies
Start by defining situations that would qualify as emergencies in your facility. This step helps to make a clear distinction between true emergencies and other issues that, although urgent, are not emergencies.
There will always be some overlap, but here are some explanations that can help you narrow down your definitions:
- Emergencies will deteriorate rapidly within a short period causing safety incidents and major business disruptions; they need immediate attention. Even if they happen on a weekend, holiday, or at night.
- Urgent situations (non-emergencies) are important as well but they can usually be isolated and attended to during normal business hours.
Another way to look at it is, if it has to be addressed right away it is an emergency and if it can be addressed a bit later, it is just a high priority work order. It helps if all employees on the premises can distinguish between emergency and non-emergency maintenance issues as this can help to quicken the reporting process.
It usually makes the most sense to focus on emergency maintenance issues that come in the form of critical asset failure as general workplace emergencies should already be covered by standard safety training that follows OSHA’s recommendations.
Gaining clarity into what could happen in potential emergency scenarios helps an organization to better manage their resources (labor, funds, spare parts, PPE, etc.) that will be required to resolve those issues.
After the WO is scheduled, email and push notifications are sent to the assigned technicians. The technicians can then review the WO and start performing the required work. When the work is finished, they need to close the work order:
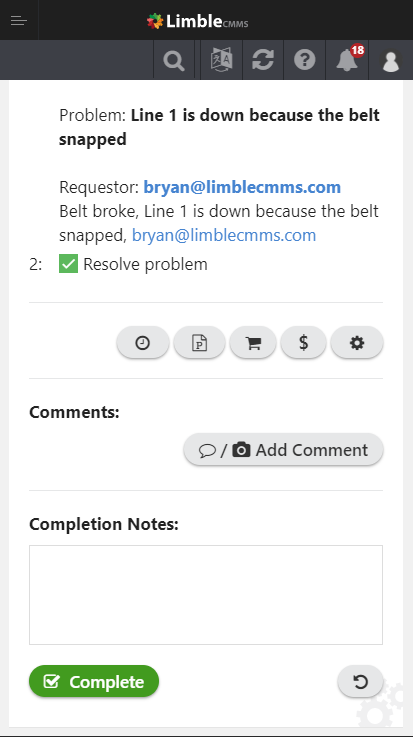
The technicians can leave completion notes, attach pictures and comments, log time it took to complete the WO, and note down how many spare parts they used. All of this helps organizations track how much resources they are spending on emergency repairs.
Better safe than sorry
While it is hard to ever be fully prepared for emergency maintenance, things we discussed in this article will hopefully help you not to get caught with your pants down.
Having a strong proactive maintenance strategy and properly trained employees are the two most important factors for avoiding preventable maintenance emergencies. The best you can do is to have a clear plan in place people can follow when an emergency maintenance request is generated.
Through Limble CMMS, we have helped numerous businesses win their battles against emergency maintenance. Reach out to learn more.
The manager reviews the request and creates an emergency work order. As you can see from a screenshot below, such a WO in Limble would be level 6 and can be tagged with something like @Safety that signals the issue is a safety risk.
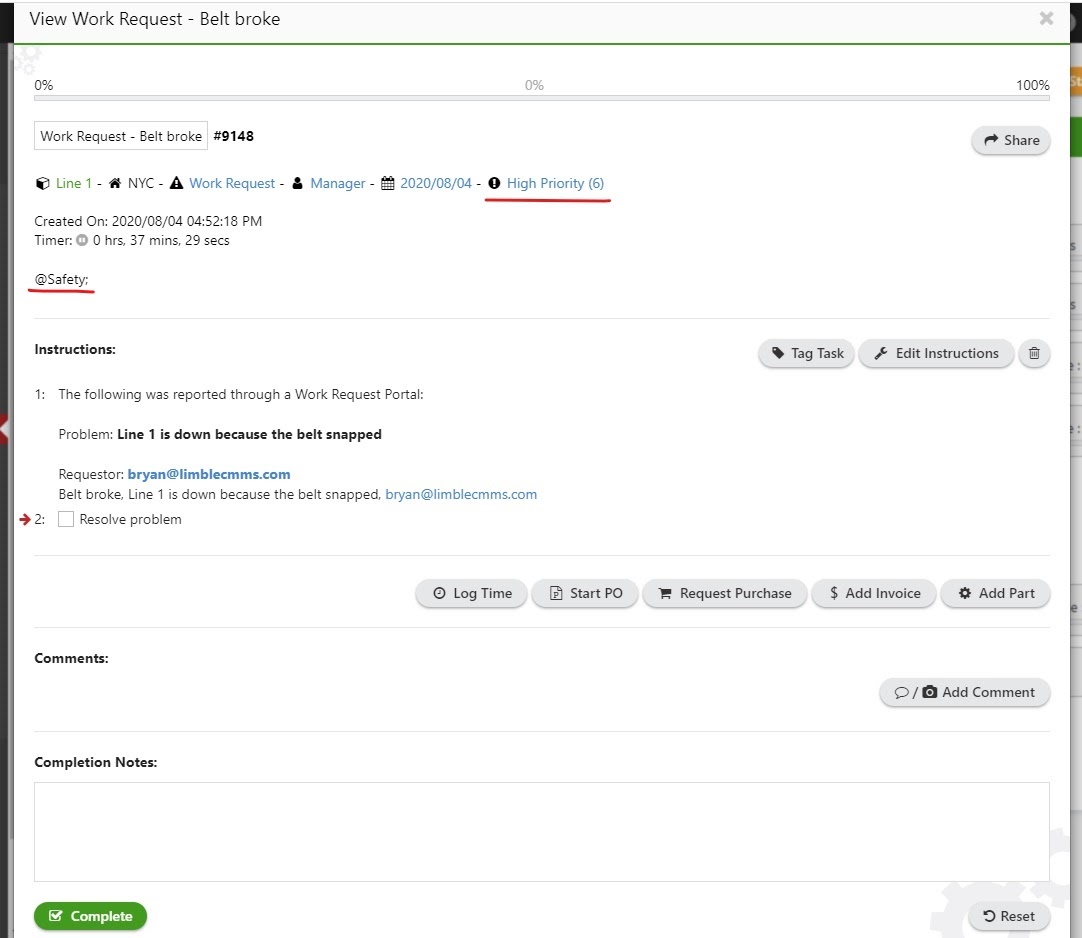
After the WO is scheduled, email and push notifications are sent to the assigned technicians. The technicians can then review the WO and start performing the required work. When the work is finished, they need to close the work order:
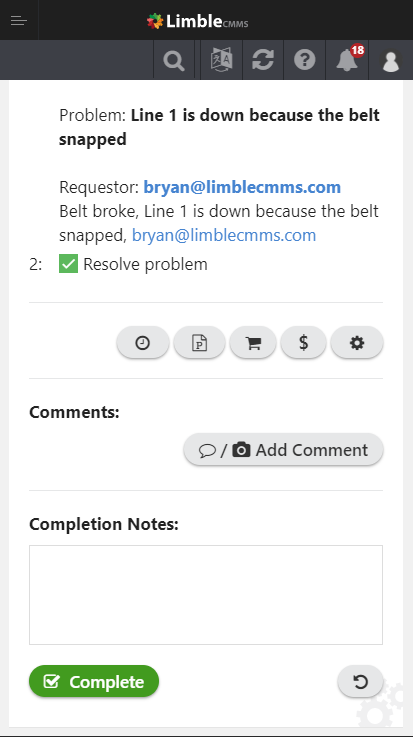
The technicians can leave completion notes, attach pictures and comments, log time it took to complete the WO, and note down how many spare parts they used. All of this helps organizations track how much resources they are spending on emergency repairs.
Better safe than sorry
While it is hard to ever be fully prepared for emergency maintenance, things we discussed in this article will hopefully help you not to get caught with your pants down.
Having a strong proactive maintenance strategy and properly trained employees are the two most important factors for avoiding preventable maintenance emergencies. The best you can do is to have a clear plan in place people can follow when an emergency maintenance request is generated.
Through Limble CMMS, we have helped numerous businesses win their battles against emergency maintenance. Reach out to learn more.
[/vc_column_text][/vc_column][/vc_row]
First, a worker submits the emergency maintenance request.
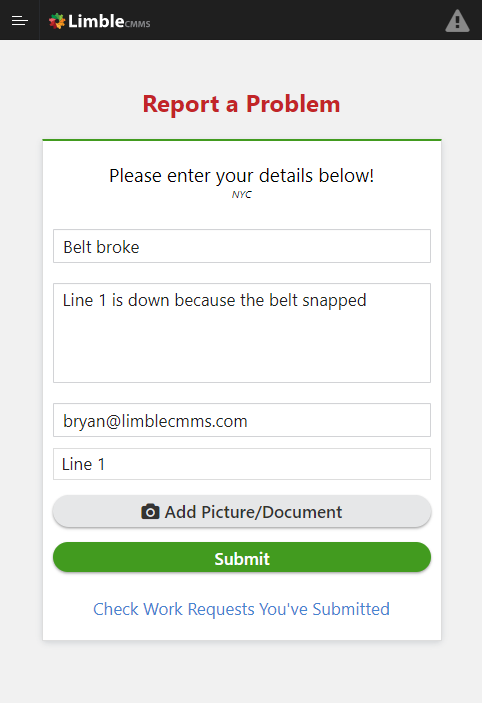
The manager reviews the request and creates an emergency work order. As you can see from a screenshot below, such a WO in Limble would be level 6 and can be tagged with something like @Safety that signals the issue is a safety risk.
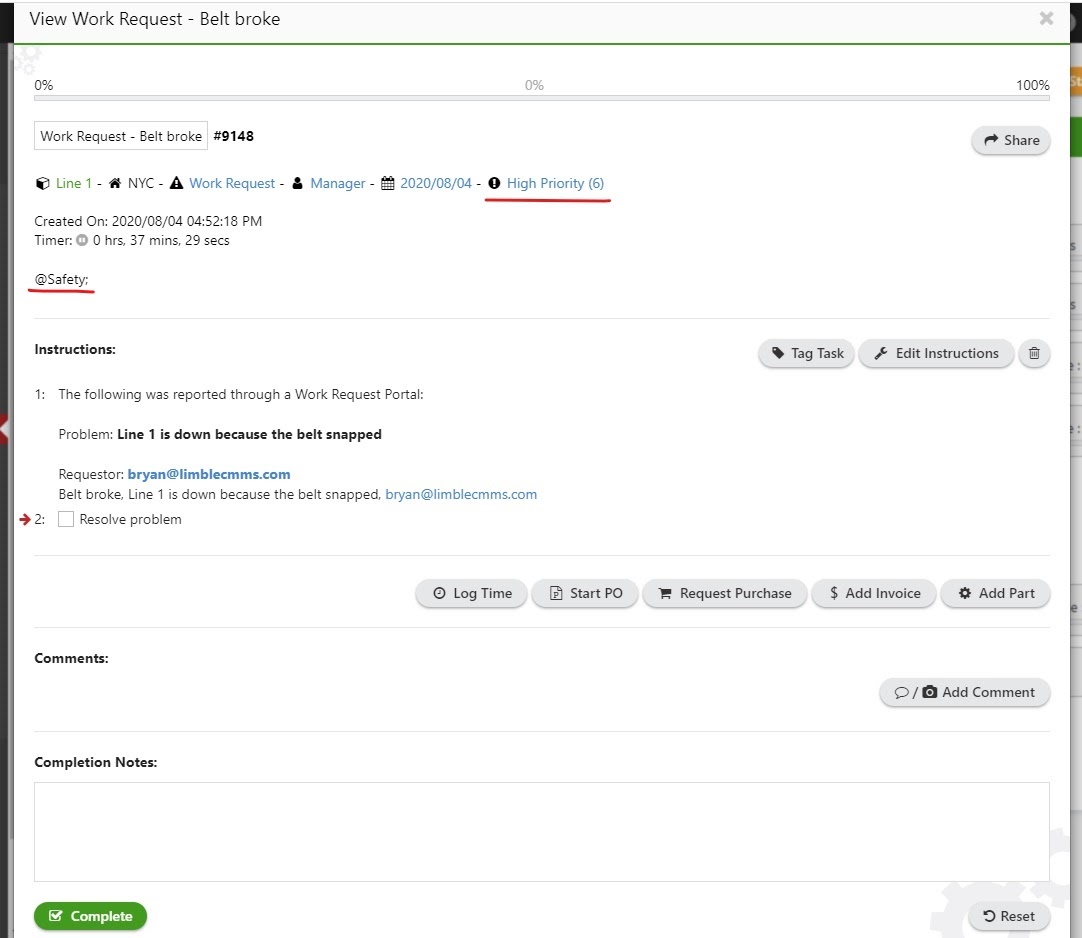
After the WO is scheduled, email and push notifications are sent to the assigned technicians. The technicians can then review the WO and start performing the required work. When the work is finished, they need to close the work order:
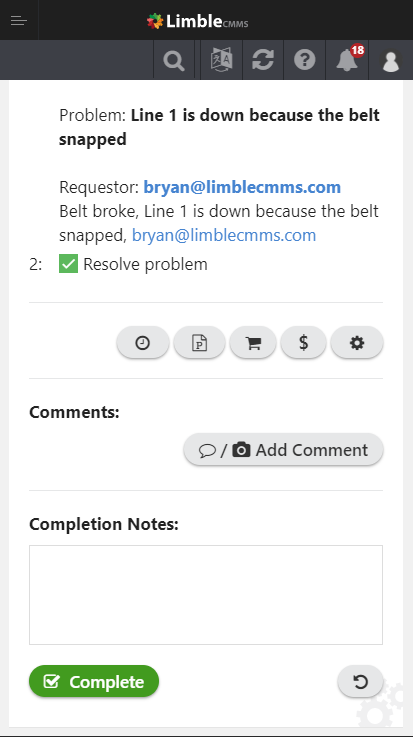
The technicians can leave completion notes, attach pictures and comments, log time it took to complete the WO, and note down how many spare parts they used. All of this helps organizations track how much resources they are spending on emergency repairs.
Better safe than sorry
While it is hard to ever be fully prepared for emergency maintenance, things we discussed in this article will hopefully help you not to get caught with your pants down.
Having a strong proactive maintenance strategy and properly trained employees are the two most important factors for avoiding preventable maintenance emergencies. The best you can do is to have a clear plan in place people can follow when an emergency maintenance request is generated.
Through Limble CMMS, we have helped numerous businesses win their battles against emergency maintenance. Reach out to learn more.
[/vc_column_text][/vc_column][/vc_row]
Automating maintenance with computerized maintenance management system will help to minimize the fallout consequences and speed up the emergency response process by:- Having the ability to quickly schedule work order and notify the right members of your maintenance team
- Speeding up the diagnosing process with instant access to asset maintenance history
- enabling real-time communication and coordination of different members of your maintenance team
- speeding up the repair process with instant access to maintenance checklists, LOTO procedures, step-by-step safety instructions, and similar documents
For an in-depth guide about what is a CMMS check out our What is a CMMS System and How Does it Work guide.
Managing emergency WOs in Limble CMMS
In Limble CMMS, you can manage emergency work requests by creating work orders of the highest priority and adding relevant tags such as “Safety incident”. The system will send out email and push notifications to the assigned technician(s) to resolve the problem.
Let’s see how that looks in practice with a few screenshots.
First, a worker submits the emergency maintenance request.
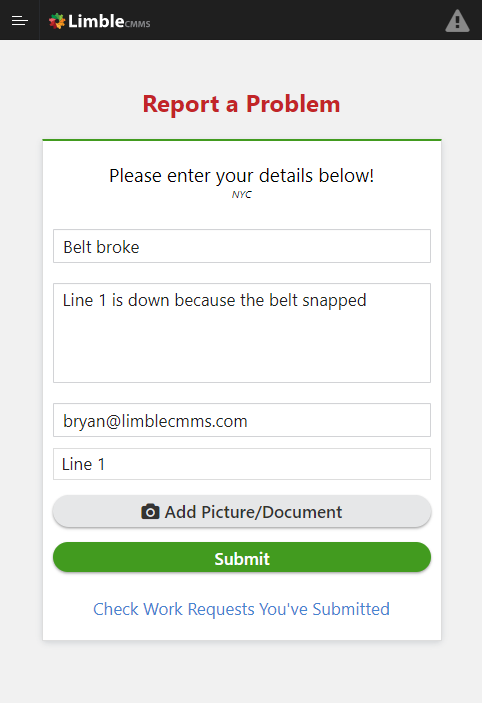
The manager reviews the request and creates an emergency work order. As you can see from a screenshot below, such a WO in Limble would be level 6 and can be tagged with something like @Safety that signals the issue is a safety risk.
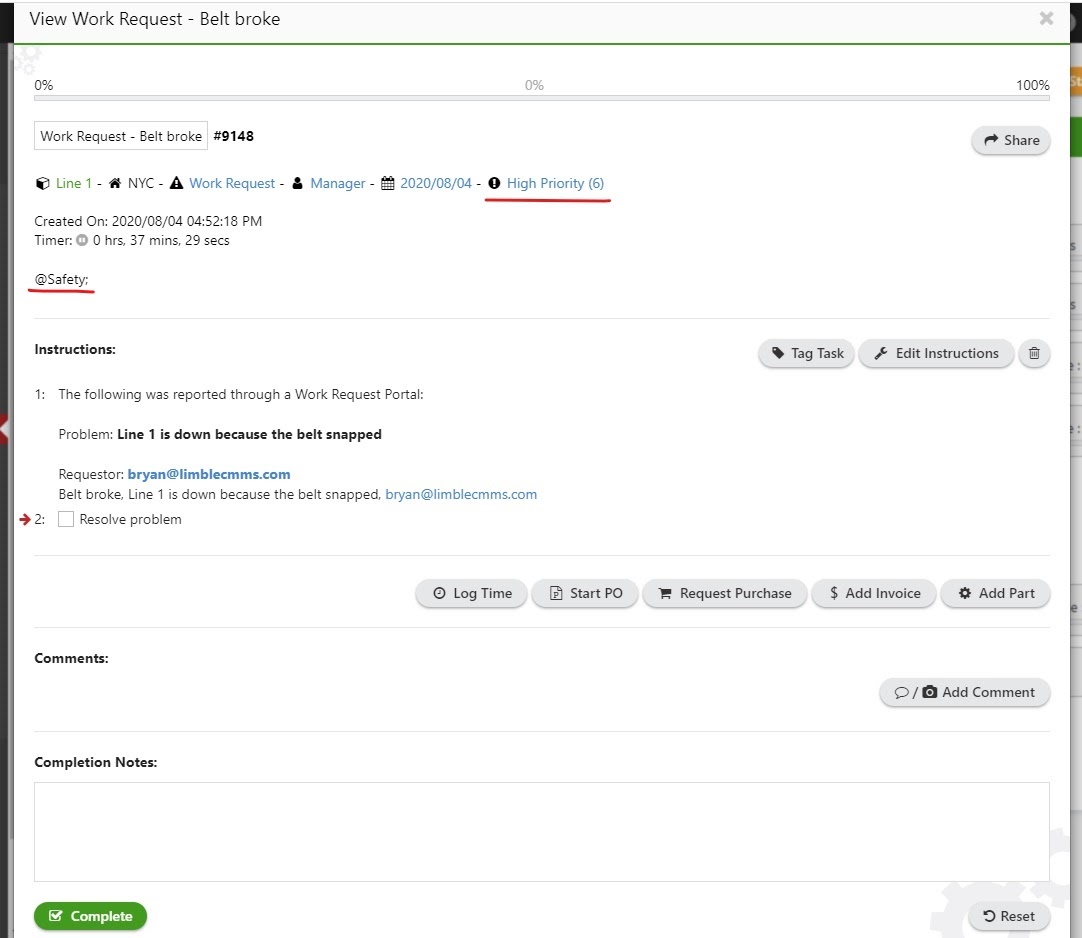
After the WO is scheduled, email and push notifications are sent to the assigned technicians. The technicians can then review the WO and start performing the required work. When the work is finished, they need to close the work order:
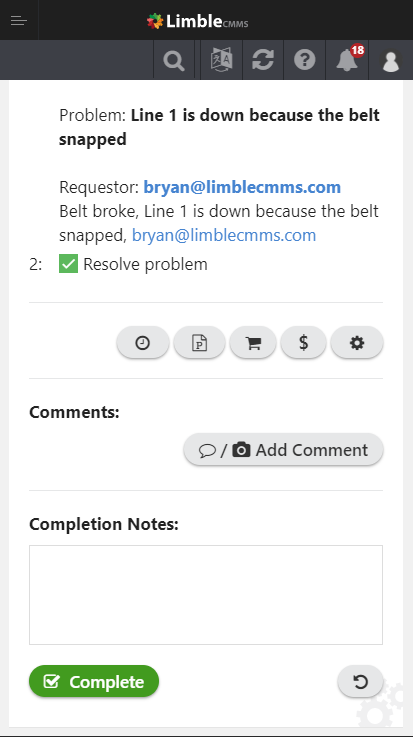
The technicians can leave completion notes, attach pictures and comments, log time it took to complete the WO, and note down how many spare parts they used. All of this helps organizations track how much resources they are spending on emergency repairs.
Better safe than sorry
While it is hard to ever be fully prepared for emergency maintenance, things we discussed in this article will hopefully help you not to get caught with your pants down.
Having a strong proactive maintenance strategy and properly trained employees are the two most important factors for avoiding preventable maintenance emergencies. The best you can do is to have a clear plan in place people can follow when an emergency maintenance request is generated.
Through Limble CMMS, we have helped numerous businesses win their battles against emergency maintenance. Reach out to learn more.
[/vc_column_text][/vc_column][/vc_row]
Automating maintenance with computerized maintenance management system will help to minimize the fallout consequences and speed up the emergency response process by:
- Having the ability to quickly schedule work order and notify the right members of your maintenance team
- Speeding up the diagnosing process with instant access to asset maintenance history
- enabling real-time communication and coordination of different members of your maintenance team
- speeding up the repair process with instant access to maintenance checklists, LOTO procedures, step-by-step safety instructions, and similar documents
For an in-depth guide about what is a CMMS check out our What is a CMMS System and How Does it Work guide.
Managing emergency WOs in Limble CMMS
In Limble CMMS, you can manage emergency work requests by creating work orders of the highest priority and adding relevant tags such as “Safety incident”. The system will send out email and push notifications to the assigned technician(s) to resolve the problem.
Let’s see how that looks in practice with a few screenshots.
First, a worker submits the emergency maintenance request.
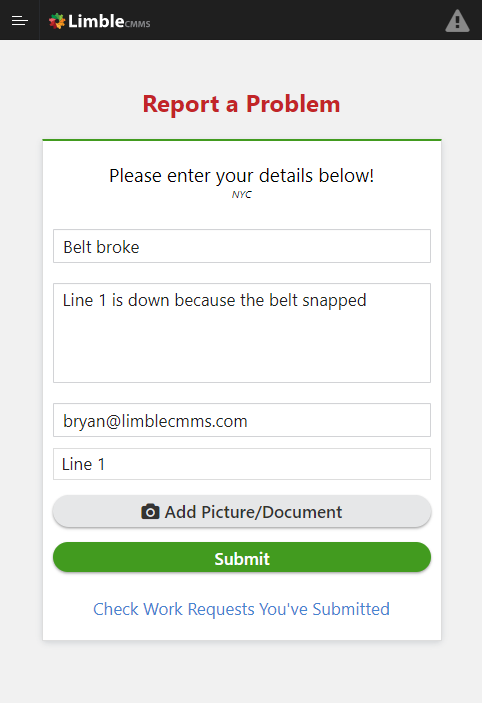
The manager reviews the request and creates an emergency work order. As you can see from a screenshot below, such a WO in Limble would be level 6 and can be tagged with something like @Safety that signals the issue is a safety risk.
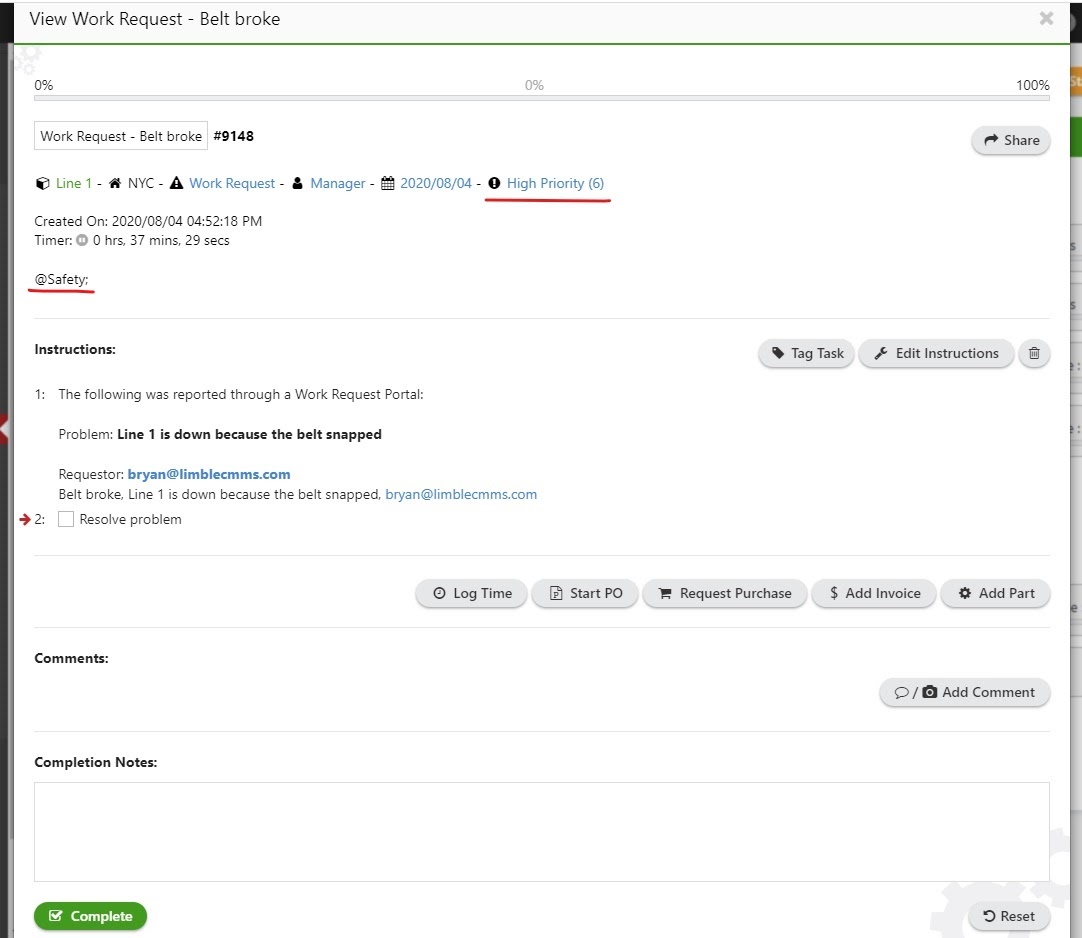
After the WO is scheduled, email and push notifications are sent to the assigned technicians. The technicians can then review the WO and start performing the required work. When the work is finished, they need to close the work order:
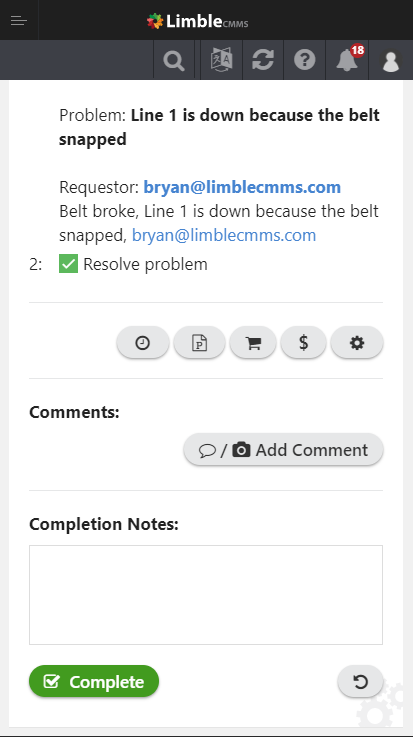
The technicians can leave completion notes, attach pictures and comments, log time it took to complete the WO, and note down how many spare parts they used. All of this helps organizations track how much resources they are spending on emergency repairs.
Better safe than sorry
While it is hard to ever be fully prepared for emergency maintenance, things we discussed in this article will hopefully help you not to get caught with your pants down.
Having a strong proactive maintenance strategy and properly trained employees are the two most important factors for avoiding preventable maintenance emergencies. The best you can do is to have a clear plan in place people can follow when an emergency maintenance request is generated.
Through Limble CMMS, we have helped numerous businesses win their battles against emergency maintenance. Reach out to learn more.
[/vc_column_text][/vc_column][/vc_row]
Note that whatever the situation, the top priority for all parties should be preserving health and safety. Only when the danger is over can emergency maintenance work begin. At that point, the maintenance team can assess the damage and plan out the repair process.
#4) Speed up emergency maintenance response with a mobile CMMS
Apart from incidents that are caused by natural disasters, emergencies in buildings can usually be attributed to a failure resulting from human error, unexpected machine failure, or procedural flaws.
Automating maintenance with computerized maintenance management system will help to minimize the fallout consequences and speed up the emergency response process by:
- Having the ability to quickly schedule work order and notify the right members of your maintenance team
- Speeding up the diagnosing process with instant access to asset maintenance history
- enabling real-time communication and coordination of different members of your maintenance team
- speeding up the repair process with instant access to maintenance checklists, LOTO procedures, step-by-step safety instructions, and similar documents
For an in-depth guide about what is a CMMS check out our What is a CMMS System and How Does it Work guide.
Managing emergency WOs in Limble CMMS
In Limble CMMS, you can manage emergency work requests by creating work orders of the highest priority and adding relevant tags such as “Safety incident”. The system will send out email and push notifications to the assigned technician(s) to resolve the problem.
Let’s see how that looks in practice with a few screenshots.
First, a worker submits the emergency maintenance request.
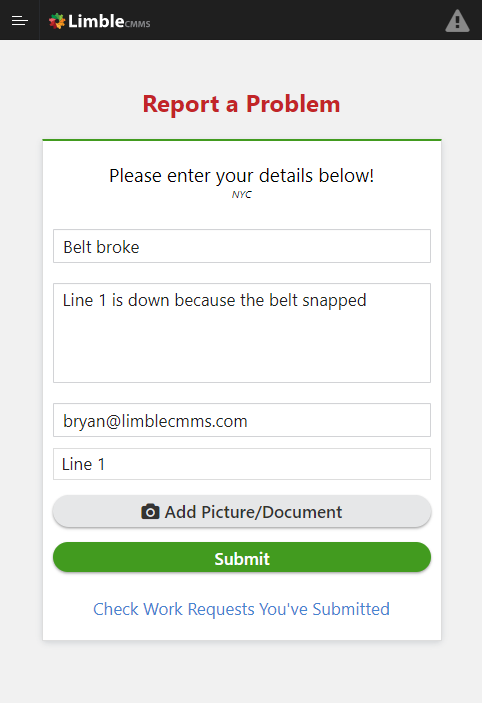
The manager reviews the request and creates an emergency work order. As you can see from a screenshot below, such a WO in Limble would be level 6 and can be tagged with something like @Safety that signals the issue is a safety risk.
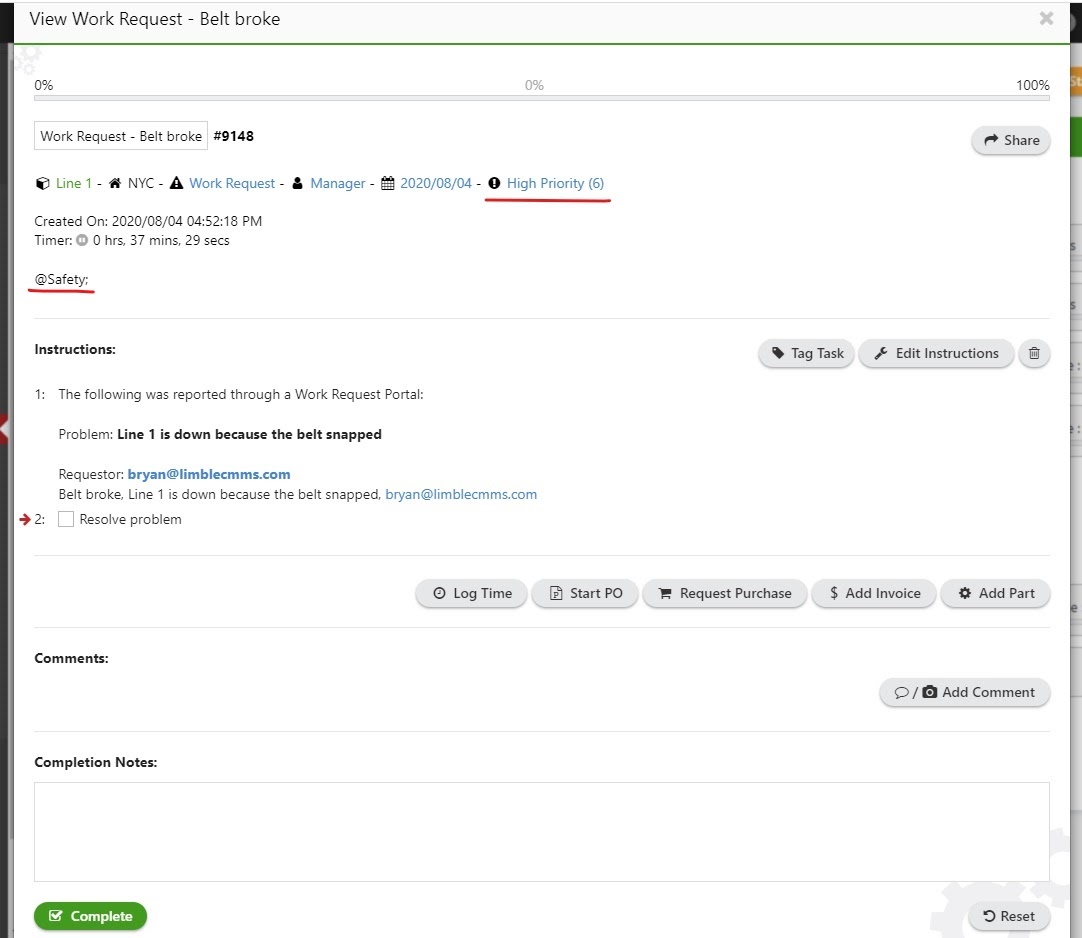
After the WO is scheduled, email and push notifications are sent to the assigned technicians. The technicians can then review the WO and start performing the required work. When the work is finished, they need to close the work order:
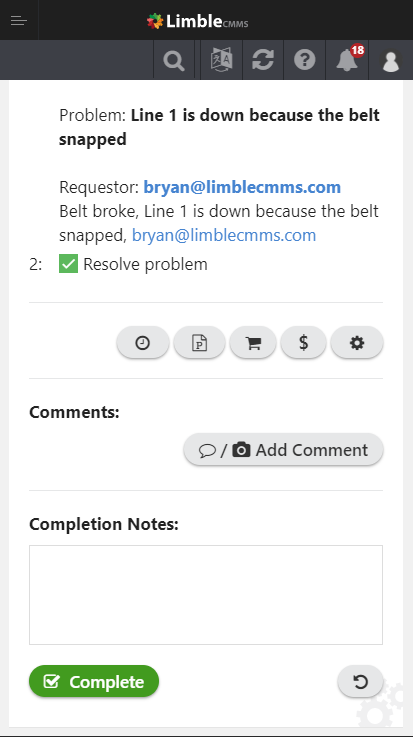
The technicians can leave completion notes, attach pictures and comments, log time it took to complete the WO, and note down how many spare parts they used. All of this helps organizations track how much resources they are spending on emergency repairs.
Better safe than sorry
While it is hard to ever be fully prepared for emergency maintenance, things we discussed in this article will hopefully help you not to get caught with your pants down.
Having a strong proactive maintenance strategy and properly trained employees are the two most important factors for avoiding preventable maintenance emergencies. The best you can do is to have a clear plan in place people can follow when an emergency maintenance request is generated.
Through Limble CMMS, we have helped numerous businesses win their battles against emergency maintenance. Reach out to learn more.
[/vc_column_text][/vc_column][/vc_row]
A list of general steps (applicable to most situations) to help your team deal with emergencies could look something like this:
- Isolate the immediate source of danger to prevent collateral damage.
- Notify the chain of command and all employees that might be affected.
- If necessary, initiate lockout tagout (LOTO) procedures.
- Assess the extent of damage and the condition of the asset.
- Plan the repair process.
- Execute repair process.
Note that whatever the situation, the top priority for all parties should be preserving health and safety. Only when the danger is over can emergency maintenance work begin. At that point, the maintenance team can assess the damage and plan out the repair process.
#4) Speed up emergency maintenance response with a mobile CMMS
Apart from incidents that are caused by natural disasters, emergencies in buildings can usually be attributed to a failure resulting from human error, unexpected machine failure, or procedural flaws.
Automating maintenance with computerized maintenance management system will help to minimize the fallout consequences and speed up the emergency response process by:
- Having the ability to quickly schedule work order and notify the right members of your maintenance team
- Speeding up the diagnosing process with instant access to asset maintenance history
- enabling real-time communication and coordination of different members of your maintenance team
- speeding up the repair process with instant access to maintenance checklists, LOTO procedures, step-by-step safety instructions, and similar documents
For an in-depth guide about what is a CMMS check out our What is a CMMS System and How Does it Work guide.
Managing emergency WOs in Limble CMMS
In Limble CMMS, you can manage emergency work requests by creating work orders of the highest priority and adding relevant tags such as “Safety incident”. The system will send out email and push notifications to the assigned technician(s) to resolve the problem.
Let’s see how that looks in practice with a few screenshots.
First, a worker submits the emergency maintenance request.
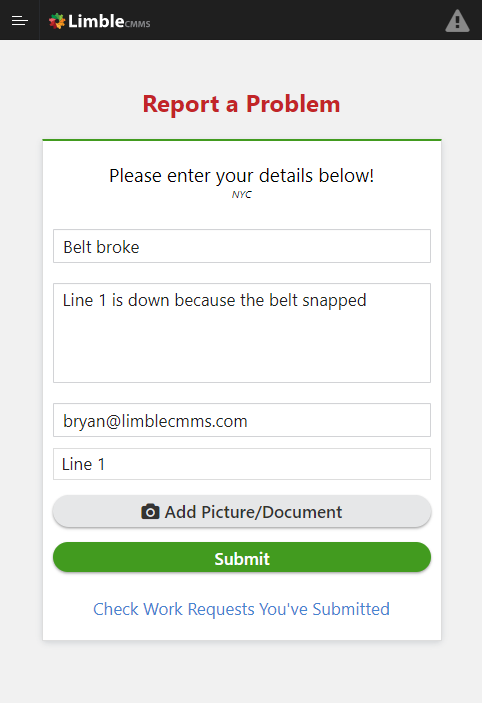
The manager reviews the request and creates an emergency work order. As you can see from a screenshot below, such a WO in Limble would be level 6 and can be tagged with something like @Safety that signals the issue is a safety risk.
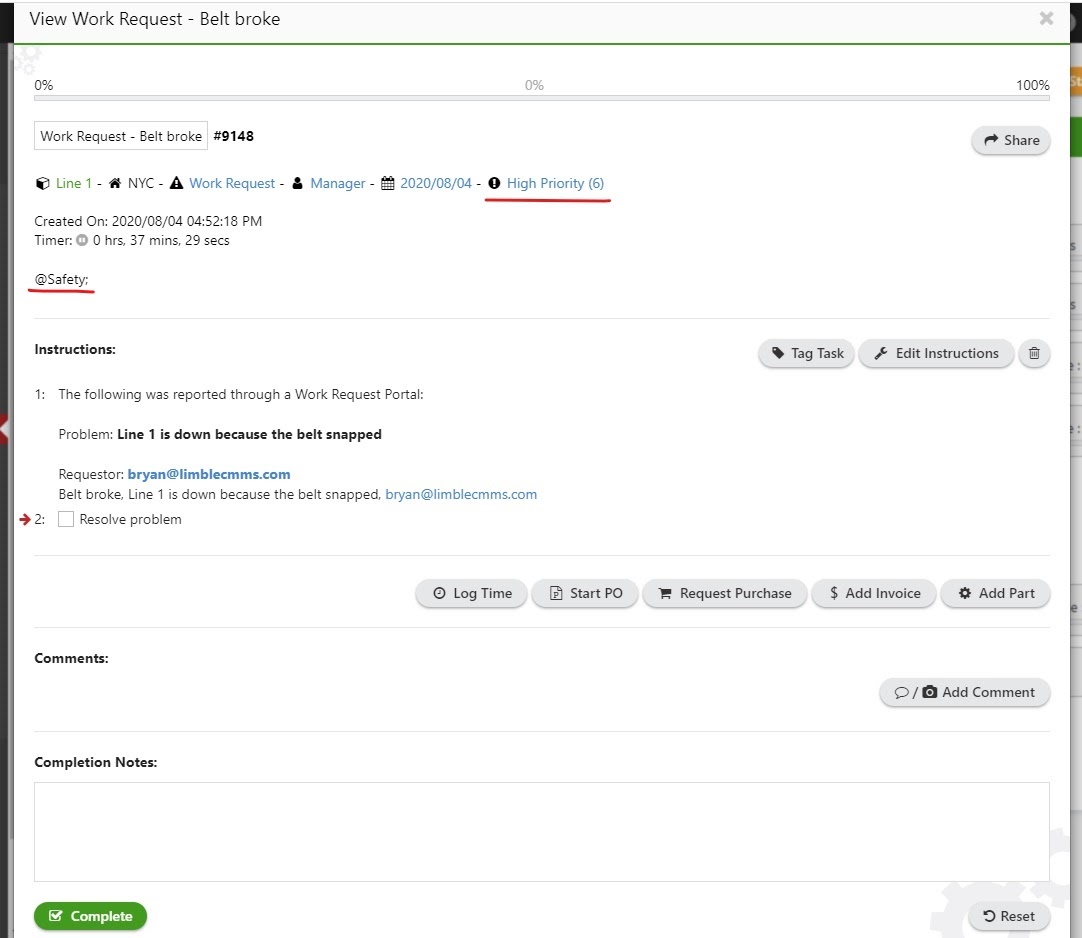
After the WO is scheduled, email and push notifications are sent to the assigned technicians. The technicians can then review the WO and start performing the required work. When the work is finished, they need to close the work order:
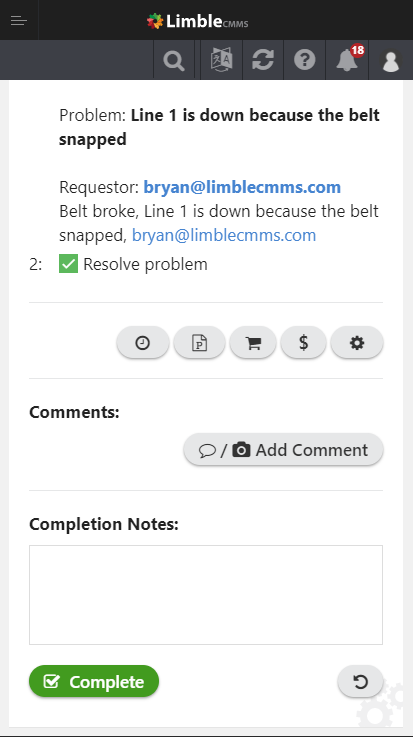
The technicians can leave completion notes, attach pictures and comments, log time it took to complete the WO, and note down how many spare parts they used. All of this helps organizations track how much resources they are spending on emergency repairs.
Better safe than sorry
While it is hard to ever be fully prepared for emergency maintenance, things we discussed in this article will hopefully help you not to get caught with your pants down.
Having a strong proactive maintenance strategy and properly trained employees are the two most important factors for avoiding preventable maintenance emergencies. The best you can do is to have a clear plan in place people can follow when an emergency maintenance request is generated.
Through Limble CMMS, we have helped numerous businesses win their battles against emergency maintenance. Reach out to learn more.
[/vc_column_text][/vc_column][/vc_row]
Whichever kind of response that an organization uses, there must be a system – usually a CMMS – that serves to record these incidents thereby building a digital trail of emergency maintenance over time. Among other things, this provides valuable information for continuous improvement going forward. Again, a CMMS facilitates and simplifies the processing of each emergency maintenance request whether it was reported manually or automatically.
#3) Outline emergency maintenance procedures
As a result of the risk assessment conducted in step #1, you can pinpoint potential emergencies based on specific equipment failures and then list steps that maintenance technicians will need to follow in each case.
That being said, listing exact steps for every scenario is not necessary. Instead, employees should have a general idea of what to do when addressing emergency maintenance requests in general (this doesn’t stop you from creating the exact list of steps for a few “most likely to happen” scenarios).
A list of general steps (applicable to most situations) to help your team deal with emergencies could look something like this:
- Isolate the immediate source of danger to prevent collateral damage.
- Notify the chain of command and all employees that might be affected.
- If necessary, initiate lockout tagout (LOTO) procedures.
- Assess the extent of damage and the condition of the asset.
- Plan the repair process.
- Execute repair process.
Note that whatever the situation, the top priority for all parties should be preserving health and safety. Only when the danger is over can emergency maintenance work begin. At that point, the maintenance team can assess the damage and plan out the repair process.
#4) Speed up emergency maintenance response with a mobile CMMS
Apart from incidents that are caused by natural disasters, emergencies in buildings can usually be attributed to a failure resulting from human error, unexpected machine failure, or procedural flaws.
Automating maintenance with computerized maintenance management system will help to minimize the fallout consequences and speed up the emergency response process by:
- Having the ability to quickly schedule work order and notify the right members of your maintenance team
- Speeding up the diagnosing process with instant access to asset maintenance history
- enabling real-time communication and coordination of different members of your maintenance team
- speeding up the repair process with instant access to maintenance checklists, LOTO procedures, step-by-step safety instructions, and similar documents
For an in-depth guide about what is a CMMS check out our What is a CMMS System and How Does it Work guide.
Managing emergency WOs in Limble CMMS
In Limble CMMS, you can manage emergency work requests by creating work orders of the highest priority and adding relevant tags such as “Safety incident”. The system will send out email and push notifications to the assigned technician(s) to resolve the problem.
Let’s see how that looks in practice with a few screenshots.
First, a worker submits the emergency maintenance request.
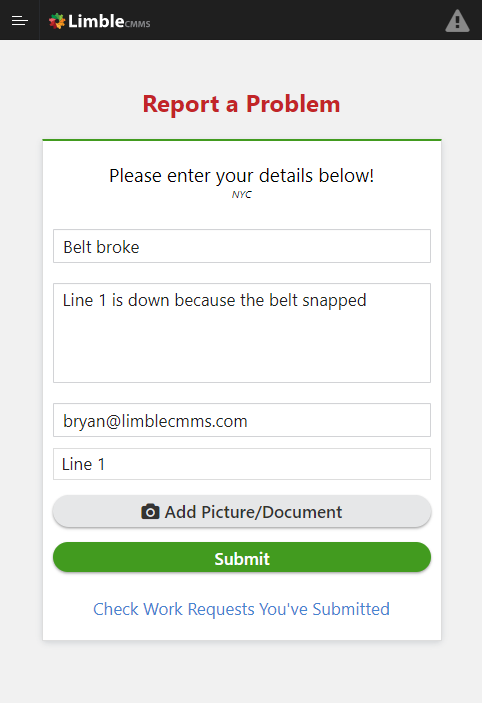
The manager reviews the request and creates an emergency work order. As you can see from a screenshot below, such a WO in Limble would be level 6 and can be tagged with something like @Safety that signals the issue is a safety risk.
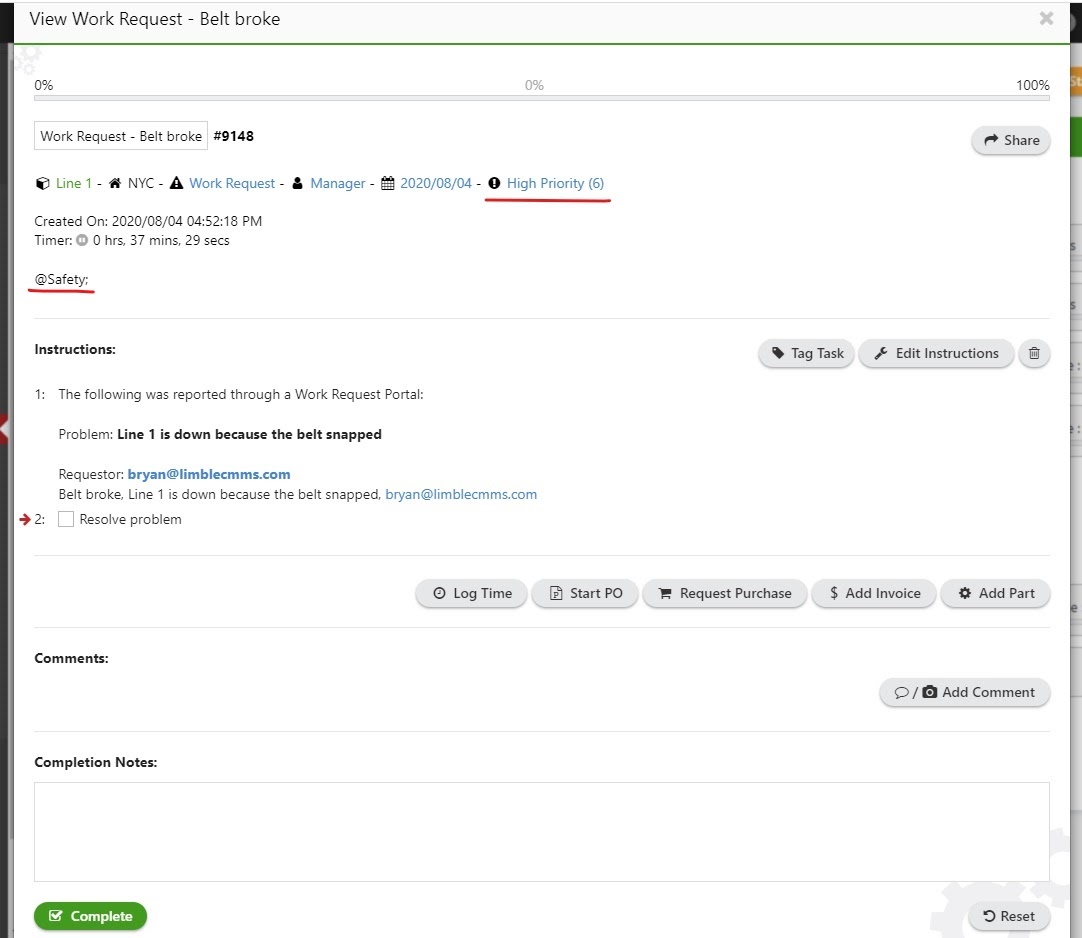
After the WO is scheduled, email and push notifications are sent to the assigned technicians. The technicians can then review the WO and start performing the required work. When the work is finished, they need to close the work order:
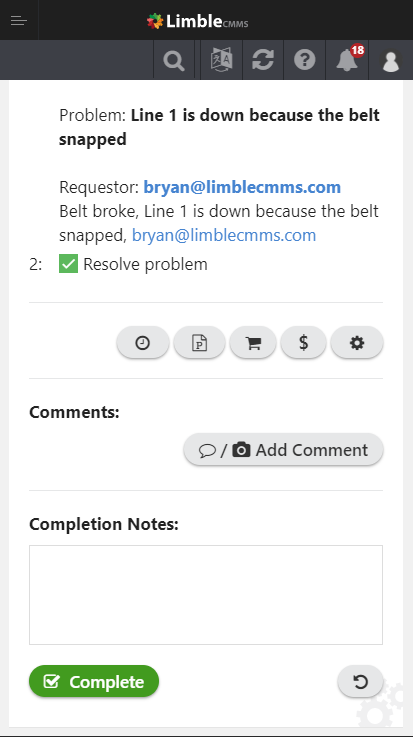
The technicians can leave completion notes, attach pictures and comments, log time it took to complete the WO, and note down how many spare parts they used. All of this helps organizations track how much resources they are spending on emergency repairs.
Better safe than sorry
While it is hard to ever be fully prepared for emergency maintenance, things we discussed in this article will hopefully help you not to get caught with your pants down.
Having a strong proactive maintenance strategy and properly trained employees are the two most important factors for avoiding preventable maintenance emergencies. The best you can do is to have a clear plan in place people can follow when an emergency maintenance request is generated.
Through Limble CMMS, we have helped numerous businesses win their battles against emergency maintenance. Reach out to learn more.
[/vc_column_text][/vc_column][/vc_row]
Decide how emergency maintenance situations will be reported, recorded, and processed from start to finish. Usually, this can be done with either of the following or a combination of both:
- Manual response: The problem is reported by an employee. The maintenance manager or supervisor reviews the work request and generates a work order to track the entire repair and restoration process.
- Automated response: A system is in place to detect anomalies in high-risk installations and take certain actions without human intervention. The actions of an automated emergency response system can include shutting down the immediate source of danger and generating electronic maintenance requests.
Whichever kind of response that an organization uses, there must be a system – usually a CMMS – that serves to record these incidents thereby building a digital trail of emergency maintenance over time. Among other things, this provides valuable information for continuous improvement going forward. Again, a CMMS facilitates and simplifies the processing of each emergency maintenance request whether it was reported manually or automatically.
#3) Outline emergency maintenance procedures
As a result of the risk assessment conducted in step #1, you can pinpoint potential emergencies based on specific equipment failures and then list steps that maintenance technicians will need to follow in each case.
That being said, listing exact steps for every scenario is not necessary. Instead, employees should have a general idea of what to do when addressing emergency maintenance requests in general (this doesn’t stop you from creating the exact list of steps for a few “most likely to happen” scenarios).
A list of general steps (applicable to most situations) to help your team deal with emergencies could look something like this:
- Isolate the immediate source of danger to prevent collateral damage.
- Notify the chain of command and all employees that might be affected.
- If necessary, initiate lockout tagout (LOTO) procedures.
- Assess the extent of damage and the condition of the asset.
- Plan the repair process.
- Execute repair process.
Note that whatever the situation, the top priority for all parties should be preserving health and safety. Only when the danger is over can emergency maintenance work begin. At that point, the maintenance team can assess the damage and plan out the repair process.
#4) Speed up emergency maintenance response with a mobile CMMS
Apart from incidents that are caused by natural disasters, emergencies in buildings can usually be attributed to a failure resulting from human error, unexpected machine failure, or procedural flaws.
Automating maintenance with computerized maintenance management system will help to minimize the fallout consequences and speed up the emergency response process by:
- Having the ability to quickly schedule work order and notify the right members of your maintenance team
- Speeding up the diagnosing process with instant access to asset maintenance history
- enabling real-time communication and coordination of different members of your maintenance team
- speeding up the repair process with instant access to maintenance checklists, LOTO procedures, step-by-step safety instructions, and similar documents
For an in-depth guide about what is a CMMS check out our What is a CMMS System and How Does it Work guide.
Managing emergency WOs in Limble CMMS
In Limble CMMS, you can manage emergency work requests by creating work orders of the highest priority and adding relevant tags such as “Safety incident”. The system will send out email and push notifications to the assigned technician(s) to resolve the problem.
Let’s see how that looks in practice with a few screenshots.
First, a worker submits the emergency maintenance request.
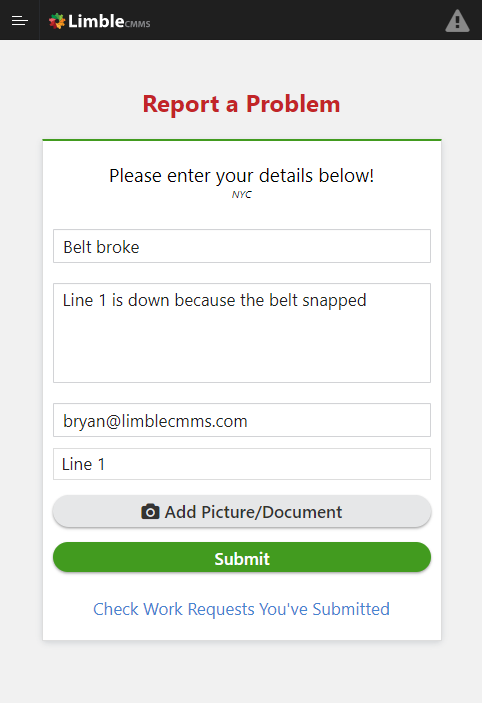
The manager reviews the request and creates an emergency work order. As you can see from a screenshot below, such a WO in Limble would be level 6 and can be tagged with something like @Safety that signals the issue is a safety risk.
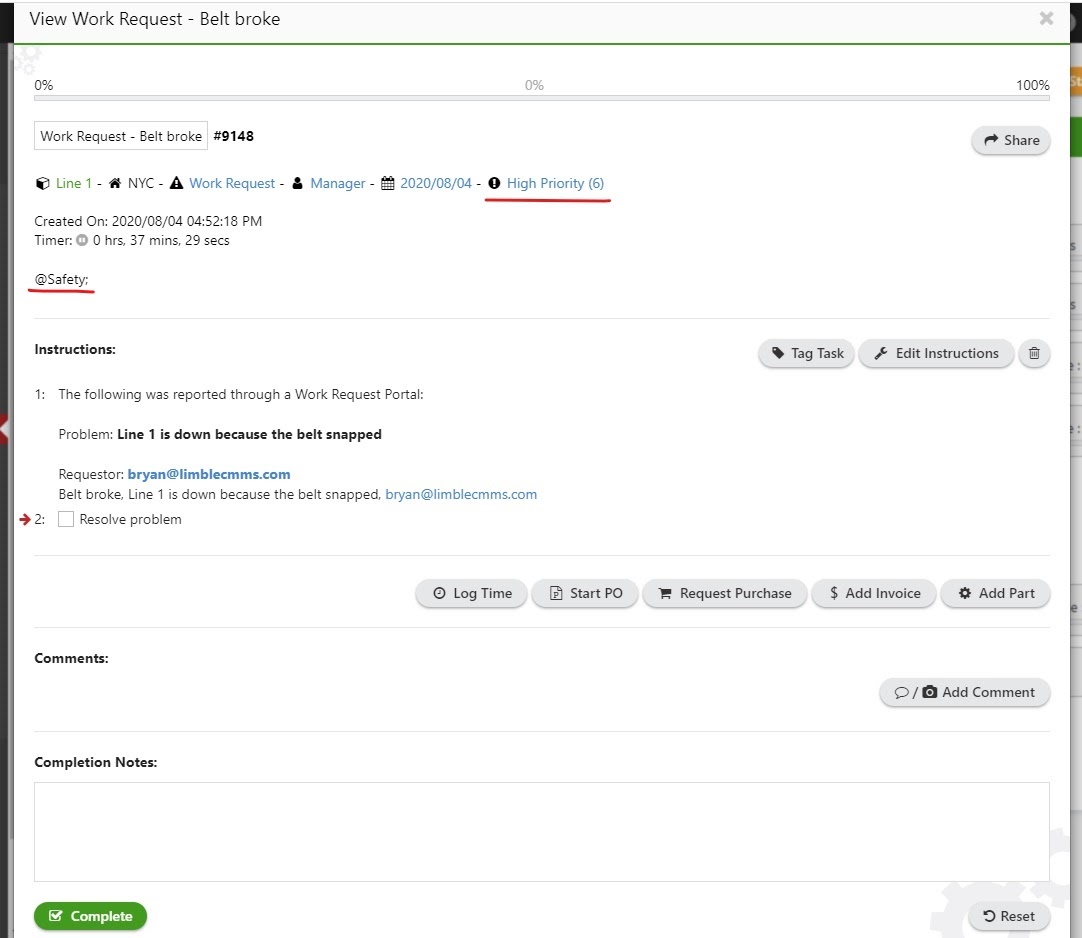
After the WO is scheduled, email and push notifications are sent to the assigned technicians. The technicians can then review the WO and start performing the required work. When the work is finished, they need to close the work order:
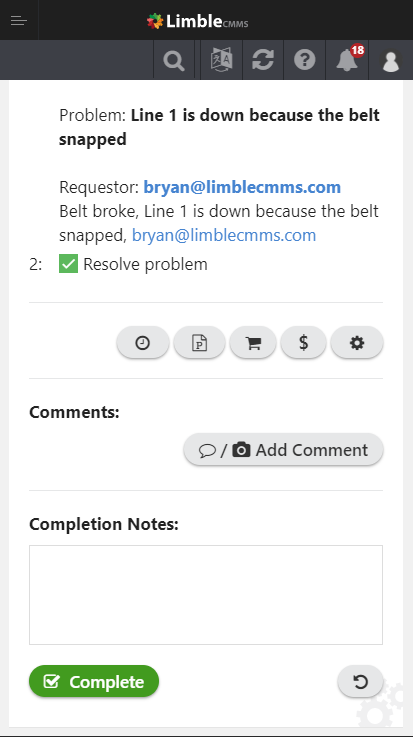
The technicians can leave completion notes, attach pictures and comments, log time it took to complete the WO, and note down how many spare parts they used. All of this helps organizations track how much resources they are spending on emergency repairs.
Better safe than sorry
While it is hard to ever be fully prepared for emergency maintenance, things we discussed in this article will hopefully help you not to get caught with your pants down.
Having a strong proactive maintenance strategy and properly trained employees are the two most important factors for avoiding preventable maintenance emergencies. The best you can do is to have a clear plan in place people can follow when an emergency maintenance request is generated.
Through Limble CMMS, we have helped numerous businesses win their battles against emergency maintenance. Reach out to learn more.
[/vc_column_text][/vc_column][/vc_row]
Of course, the scenarios that you should look at are only those that have some chance of happening. One way to estimate which failure scenario is more likely to happen is to conduct the risk assessment on your critical assets.
#2) Define emergency maintenance workflow
Decide how emergency maintenance situations will be reported, recorded, and processed from start to finish. Usually, this can be done with either of the following or a combination of both:
- Manual response: The problem is reported by an employee. The maintenance manager or supervisor reviews the work request and generates a work order to track the entire repair and restoration process.
- Automated response: A system is in place to detect anomalies in high-risk installations and take certain actions without human intervention. The actions of an automated emergency response system can include shutting down the immediate source of danger and generating electronic maintenance requests.
Whichever kind of response that an organization uses, there must be a system – usually a CMMS – that serves to record these incidents thereby building a digital trail of emergency maintenance over time. Among other things, this provides valuable information for continuous improvement going forward. Again, a CMMS facilitates and simplifies the processing of each emergency maintenance request whether it was reported manually or automatically.
#3) Outline emergency maintenance procedures
As a result of the risk assessment conducted in step #1, you can pinpoint potential emergencies based on specific equipment failures and then list steps that maintenance technicians will need to follow in each case.
That being said, listing exact steps for every scenario is not necessary. Instead, employees should have a general idea of what to do when addressing emergency maintenance requests in general (this doesn’t stop you from creating the exact list of steps for a few “most likely to happen” scenarios).
A list of general steps (applicable to most situations) to help your team deal with emergencies could look something like this:
- Isolate the immediate source of danger to prevent collateral damage.
- Notify the chain of command and all employees that might be affected.
- If necessary, initiate lockout tagout (LOTO) procedures.
- Assess the extent of damage and the condition of the asset.
- Plan the repair process.
- Execute repair process.
Note that whatever the situation, the top priority for all parties should be preserving health and safety. Only when the danger is over can emergency maintenance work begin. At that point, the maintenance team can assess the damage and plan out the repair process.
#4) Speed up emergency maintenance response with a mobile CMMS
Apart from incidents that are caused by natural disasters, emergencies in buildings can usually be attributed to a failure resulting from human error, unexpected machine failure, or procedural flaws.
Automating maintenance with computerized maintenance management system will help to minimize the fallout consequences and speed up the emergency response process by:
- Having the ability to quickly schedule work order and notify the right members of your maintenance team
- Speeding up the diagnosing process with instant access to asset maintenance history
- enabling real-time communication and coordination of different members of your maintenance team
- speeding up the repair process with instant access to maintenance checklists, LOTO procedures, step-by-step safety instructions, and similar documents
For an in-depth guide about what is a CMMS check out our What is a CMMS System and How Does it Work guide.
Managing emergency WOs in Limble CMMS
In Limble CMMS, you can manage emergency work requests by creating work orders of the highest priority and adding relevant tags such as “Safety incident”. The system will send out email and push notifications to the assigned technician(s) to resolve the problem.
Let’s see how that looks in practice with a few screenshots.
First, a worker submits the emergency maintenance request.
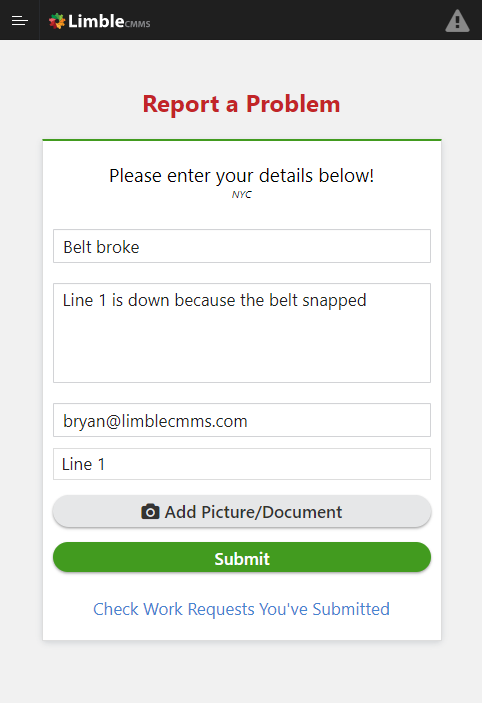
The manager reviews the request and creates an emergency work order. As you can see from a screenshot below, such a WO in Limble would be level 6 and can be tagged with something like @Safety that signals the issue is a safety risk.
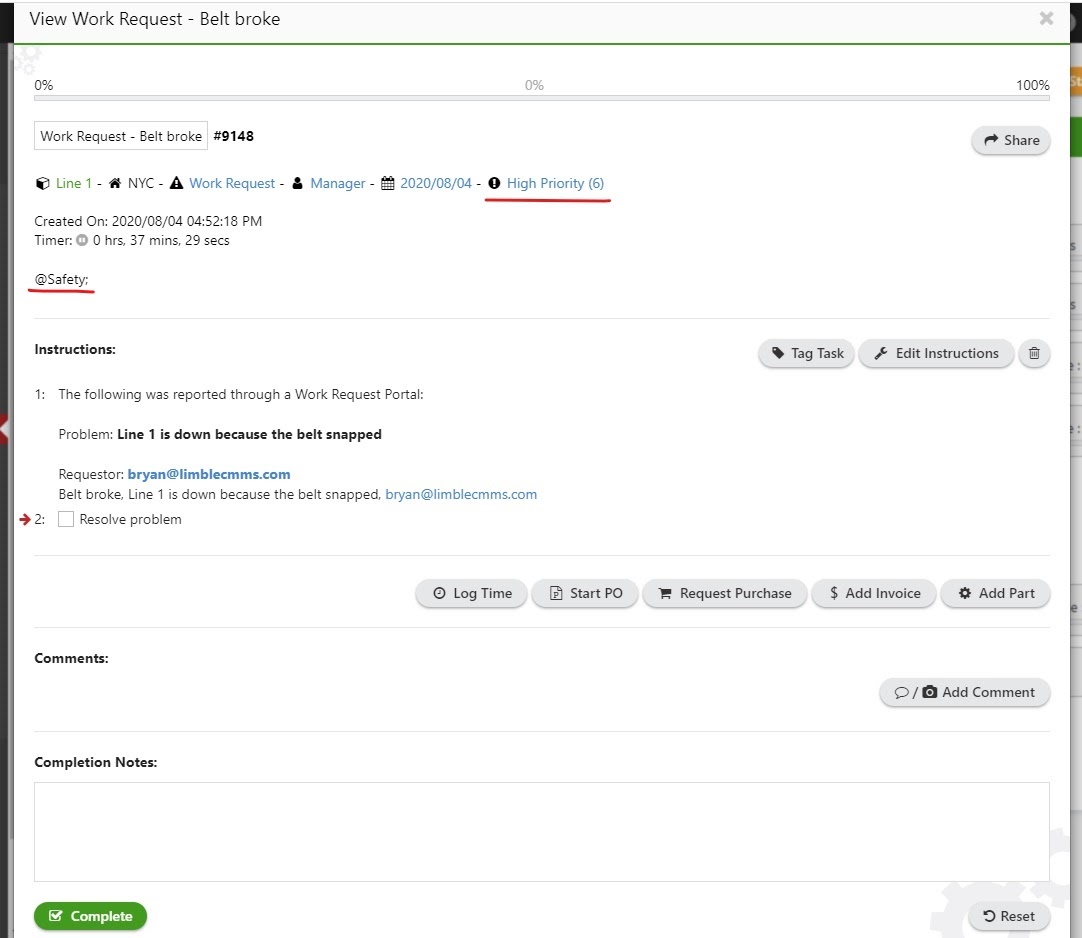
After the WO is scheduled, email and push notifications are sent to the assigned technicians. The technicians can then review the WO and start performing the required work. When the work is finished, they need to close the work order:
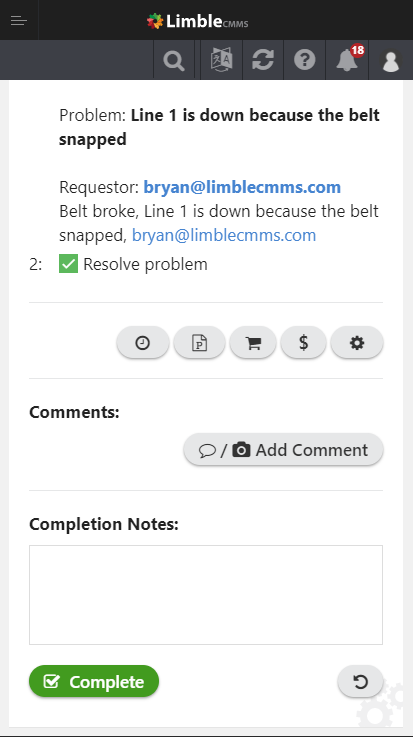
The technicians can leave completion notes, attach pictures and comments, log time it took to complete the WO, and note down how many spare parts they used. All of this helps organizations track how much resources they are spending on emergency repairs.
Better safe than sorry
While it is hard to ever be fully prepared for emergency maintenance, things we discussed in this article will hopefully help you not to get caught with your pants down.
Having a strong proactive maintenance strategy and properly trained employees are the two most important factors for avoiding preventable maintenance emergencies. The best you can do is to have a clear plan in place people can follow when an emergency maintenance request is generated.
Through Limble CMMS, we have helped numerous businesses win their battles against emergency maintenance. Reach out to learn more.
[/vc_column_text][/vc_column][/vc_row]