Autonomous Maintenance
Everything you ever needed to know about autonomous maintenance.
What is autonomous maintenance?
Autonomous maintenance is the first step in the process of implementing Total Productive Maintenance. It represents an approach to maintenance where machine operators take the responsibility for basic maintenance tasks away from maintenance personnel.
In practice, this means that actions like safety checks, cleaning, and lubrication are performed by machine operators, which gives maintenance techs the freedom to concentrate on more complex maintenance tasks.
When implemented correctly, autonomous maintenance can bring many additional benefits. We will discuss the biggest ones next.
What are the main benefits of autonomous maintenance?
- Ensuring equipment is properly cleaned and lubricated. When many big repairs are going around, and maintenance techs are in a hurry, simple tasks like cleaning and lubrication often don’t get the attention they deserve. With autonomous maintenance, machine operators can take over and ensure those tasks are carried out in a proper and timely manner.
- Noticing issues before they lead to critical failures. When machine operators have an in-depth knowledge of the equipment they work with, they can recognize the early signs of equipment deterioration and malfunction and initiate corrective actions.
- Freeing maintenance personnel for higher-level tasks. AM does not render the maintenance staff redundant. Instead, it frees them up to focus, plan better, and prioritize their specialist skills for more critical equipment-related issues.
- Improving employee participation and a sense of relevance in the bigger picture. Shared responsibility for equipment upkeep, combined with a company culture that encourages feedback from staff, further motivates employees to take ownership of their machinery and is known to have a positive effect on overall productivity.
- Improving overall safety. Due to the continuous upkeep of machinery, as well as cleaner and better-organized surroundings, there are fewer risks of injuries due to littered tools, clutter, and other forms of disorderliness.
Overall, all these improvements help you maximize equipment effectiveness and safety, eliminate waste, and boost workforce productivity.
If you’re looking to implement autonomous maintenance or any of the practices it preaches, we can show you how a CMMS can help with the transition process. Contact us for more info.
Checklist for Creating a Preventive Maintenance Plan
Following a consistent Preventive Maintenance Plan can make life easier. Use this checklist to create your own!
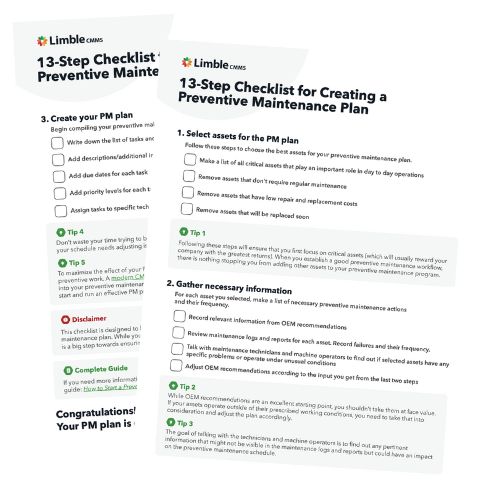
What does autonomous maintenance training encompass?
The additional responsibilities that operators will take on under autonomous maintenance demand that they undergo dedicated training. This training will ensure that operators’ skills increase, it will teach them what they need to know, and possibly even empower them to improve the equipment with time.
What does the AM training cover?
Operators are taught basic maintenance tasks with a focus on being proactive and responsive to machine problems. Those facilitating these training sessions will mainly be maintenance technicians and engineers.
Typically, they’ll learn equipment cleaning, inspection, lubrication, adjustments, quick repairs, identifying signs of deterioration, safety, and when they need to involve maintenance staff.
Mediums for autonomous maintenance training
There are several mediums for knowledge transfer during autonomous maintenance training. The most commonly used are formal classroom training and on-the-job training.
Formal classroom training
At the very beginning, training can start with some formal classroom lessons, especially where trainees need to view the information through audio-visual devices or where they need access to computers. For instance, operators handling very complex or sensitive equipment can be trained at first using technologies like virtual simulations.
The classroom setting is also a good venue for dissecting documents like OEM manuals, equipment history, and relevant data coming from sources like a computerized maintenance management system (CMMS) if they have one.
Once the trainers confirm that the information has been well received and that the operators can perform these maintenance tasks, the lessons can move to the plant floor. That takes us to the next training medium.
On-the-job training (OJT)
This is where the operators get practical guidance on the plant floor about what they need to do. Technicians will demonstrate to them everything they were taught in the classroom setting. This process should never be rushed. The maintenance personnel should be patient and check that the operator understands what to do under different scenarios before handing over the asset.
Want to see Limble in action? Get started for free today!
Key takeaway
Looking at everything stated above, it is easy to understand how implementing autonomous maintenance is a lot of work.
I am not here to convince you otherwise. As a part of TPM, the push for autonomous maintenance is a big organizational effort. But that doesn’t mean you can’t steal certain practices and use them to improve your maintenance department.
Teaching machine operators to look for specific wear and tear signs that lead to critical failures is just one simple thing that could reduce the number of unexpected breakdowns later down the line. Do not underestimate the power of incremental improvements.
If you have any further questions about the role of a CMMS in implementing autonomous maintenance and TPM, get in touch via our contact form.