German car manufacturers developed the field failure analysis (FFA) process in response to the escalating warranty costs borne by their industry in the early 2000s. In 2006 industry experts estimated that warranty claims totaled between two and four percent of a vehicle’s cost, exceeding $30 billion per annum. By 2014, quality and warranty costs had reached almost $50 billion.
Eager to reduce warranty claims and return those costs to their member’s profit statements, the German Verband der Automobilindustrie (VDA) designed the FFA process to create a comprehensive and collaborative quality management system using a root cause analysis process.
The goal of this article is to give you an idea of how this process works in practice.
What is Field Failure Analysis?
Field failure analysis involves collaboration between customers and suppliers to analyze returned failed components, particularly those with no-fault found reports. It is suitable for the entire supply chain, including original equipment manufacturers (OEM) and suppliers. It provides discrete steps, defined procedures, and a clear allocation of responsibilities.
Field Failure Analysis Process described by VDA. Source: ZVEI
When a component failure occurs ‘in the field,’ the defective part is replaced, and the manufacturer (OEM) or supplier may request their return to allow analysis. There is often no fault found during the analysis.
In the past, suppliers or the OEM took no further action. But that had to change. The objective of the FFA was to establish the reason for removing a field failed part from a vehicle, identify the root cause of the failure, and implement corrective actions. A subsequent process was designed to address the no-fault-found parts once they trigger an agreed threshold.
Despite its automotive roots, field failure analysis is finding its way into other manufacturing industries keen to avoid the costs of product failure.
The Essential Guide to CMMS
Download this helpful guide to everything a CMMS has to offer.
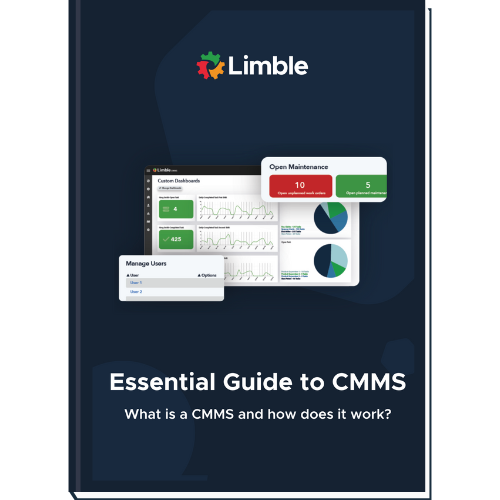
The steps of the FFA process
Field failure analysis follows an escalating test philosophy to ensure a rigorous analysis, but one that can be economically justified.
Phase #1: Part analysis
The FFA process begins upon receipt of a defective part from the field and involves a part analysis. The part analysis takes place in three discrete steps: standard tests, complaint evaluation, and tests under load.
1a: Standard tests
The standard test begins with a comprehensive visual inspection before testing the component at ambient temperatures and in an environment that mirrors in-service conditions, including loads.
All tests must follow accepted test methods and use unambiguous test criteria, with all normal tests fully completed. Identification of a fault is not a reason to prematurely cease testing. The person carrying out the tests should carefully document the process, findings, and observations.
Standard and load tests should not damage the inspected part so it can be re-installed into the machine for further testing. This is why destructive testing is avoided (unless the supplier and the customer specifically agree to it).
1.b: Failure complaint evaluation
An explicit fault description must accompany any part received from the field. After completing the standard test, the testing team will evaluate the complaint or fault description, and any faults found are checked for plausibility against the customer’s complaint.
If the fault is proven, the FFA process proceeds to a problem-solving process. If no faults are detected or the failure found does not align with the original complaint, the testing team will plan additional specific load tests to elicit the original failure.
1.c: Load tests
Proceeding to the load testing phase assumes the standard tests found no fault, or the identified faults do not accord with the customer complaint.
The test plan must be agreed on, based on the component design parameters and requirements specifications. It must ensure the testing is equivalent to the environmental and in-operation conditions, including humidity, speeds, voltages, and physical loads. Extra load parameters should form part of the test plan to evoke the defects highlighted in the complaint.
If a fault is proven, the FFA process proceeds to a product-handling procedure, with the component tagged as ‘not in order,’ or N.I.O. Tagging a part as N.I.O does not mean the customer complaint is proven, simply that testing found a fault.
Those parts with no proven faults are tagged as ‘in order,’ or I.O., based on part analysis. The I.O. tag does not mean the part is serviceable, simply that testing failed to elicit a fault. If the triggering criteria are met for parts tagged as I.O., the defective part proceeds to the NTF or ‘no trouble found’ phase; if not, the part passes to a product handling procedure.
Completing the load tests is an inflection point, determining whether the component proceeds to a product handling procedure as an individual failure or triggers the NTF process to investigate possible systemic or process defects due to the number or importance of the failures.
The NTF trigger is an agreed metric between the parties involved, usually the supplier and OEM. It may be an agreed threshold of parts reported as ‘in order’ following the part analysis, based on the number of complaints received from a customer or any faults that arise from a new component or product launch.
Phase #2: The NTF process
The NTF process comprises of three distinct but highly iterative stages, making it incorrect to consider them a linear progression. Instead, you should look at them as three corners of a triangle, in the center of which lies the answer.
2a: Data collection and evaluation
The data collection and evaluation stage involves each party in the NTF process carrying out data collection and evaluation related to their area of responsibility.
This stage is wide-ranging and may include failure databases, the geographic specificity of failure, service and repair data, or production process information. Evaluation techniques can include statistical analysis, equipment history, correlations between failure rates and production changes, or failures due to mileage.
2b: System tests
The system tests are a more comprehensive and wider-ranging version of the load tests. They may include involvement from outside testing laboratories, aging tests, functional tests under varying loads, or tests in the vehicle producing the problems.
Rather than focus solely on the component, the system tests investigate relationships and active connections within the system.
2c: Process study
The process study investigates interface issues between organizations and systemic problems in programming, diagnosis, or equipment and parts manuals. It may also investigate possible influences from peripheral components that might impact the failure, such as seals, hoses, clamps, or electrical connectors.
If the NTF process has failed to identify an issue, all parties must agree whether to continue with further analysis or document and conclude the process. If the NTF process identifies the problem, the FFA proceeds to the problem-solving stage.
Phase #3: Problem solving
The automobile industry uses the 8D method for sustainable problem-solving. However, for this stage, an organization may use any of the standard root-cause analysis processes they are familiar with.
The 8D method uses the following steps:
- Assemble the team
- Describe the problem
- Contain the problem – isolate from client impact
- Carry out a root cause analysis
- Plan permanent corrective actions
- Implement and validate permanent corrective actions
- Prevent recurrence
- Recognize team contributions
Who initiates and conducts field failure analysis?
The OEM will usually initiate the FFA process, as they will receive the warranty returns or defective parts. However, the supplier should begin their part of the process the moment they receive defective parts into their stores’ system. Under the FFA procedure, a supplier has strict responsibilities to quarantine, document, track, and preserve the defective parts to ensure a rigorous chain of custody.
The FFA procedure is collaborative and depends on the context of the failure, with all parties agreeing on who will lead the process and who will take part, as well as the responsibilities and deliverables of all parties. Much of the process will require the involvement of all parties, with one nominated to take the lead.
Data management and evidence preservation
The data management and collection process underpins the integrity of the FFA process. This process revolves around two principles:
- The first is a rigorous and documented chain of custody and evidence preservation management system that starts upon receipt of the part from the field and does not end until its disposal.
- The second principle is that once a part failure is found, at any point in the FFA process, it is declared defective regardless of whether the failure can or cannot be reproduced.
To ensure a meaningful analysis, upon receipt of a defective part, the supplier or OEM must implement a system of traceability that will follow the part through the FFA and which may be examined at any point to understand the component’s test status.
Tagging or bar-coding an item allows a CMMS to control the process and pinpoint the component’s precise location while tracking and updating each action taken under the FFA procedure.
The item must be reliably marked and retained in a quarantine area to prevent it from being returned to service, sold, or destroyed. To prevent affecting the investigation process, the supplier or OEM must exercise care not to clean, modify, or damage the component, unless such cleaning or modification forms part of the formal FFA procedure agreed upon by the parties.
Field failure analysis case study
An automobile manufacturer initiated an FFA to investigate a high failure rate it was experiencing for an oxygen sensor on a vehicle. The vehicle controller monitors the sensor, which forms part of the vehicle’s exhaust system, and displays a dashboard message if a fault is detected. 78% of the failures occurred within the first 5,000 miles of use.
The OEM performed the standard test following the initiation of the FFA process. The unit did not evidence any failure, was marked I.O., and passed to the testing-under-load phase.
Testing under load also did not show any failure, so the unit was marked I.O. and passed to the NTF process, which was triggered due to the high number of failures occurring in the field.
During the NTF process, the team found that the contact blades used by the connecting cable were scratched. They proceeded to investigate the manufacturing process for the contacts and found that there is a risk of a bad cable connection.
The NTF process team passed the information to the NTF test team, who devised a test focusing on the possibility of intermittent electrical contact. The test confirmed the risk of failure, with the sensor tagged N.I.O.
In the subsequent problem-solving phase, the team used root cause analysis techniques to optimize the manufacturing process for the sensor plug contacts. The sensor failure rate was resolved as a result of the corrective action, with the failure root cause corrected 90 days after it first occurred in a vehicle.
Building quality into existing products
The outlined field failure analysis process provides a useful template for other industries and manufacturers who wish to stop spending money on warranty returns and product recalls.
Implementing such a strictly controlled and documented process removes subjectivity and external influence from product investigations and testing. It provides a scientific and systematic approach for applying corrective actions and building quality into existing products.