Understanding current workforce trends is increasingly important for successful maintenance management. It enables strategic decision-making, ensuring a balanced workload for technicians throughout the year. It also prepares organizations to adapt throughout industry-wide staffing shortages.
In this article, we’ll explore how emerging technologies and shifting workforce dynamics are redefining the maintenance workforce landscape.
1. Declining interest among younger generations in maintenance careers
Recent statistics and studies reveal a concerning trend: younger generations are showing less interest in maintenance careers. The issue extends beyond declining enrollment in technical and vocational programs — it reflects broader career preferences among young people.
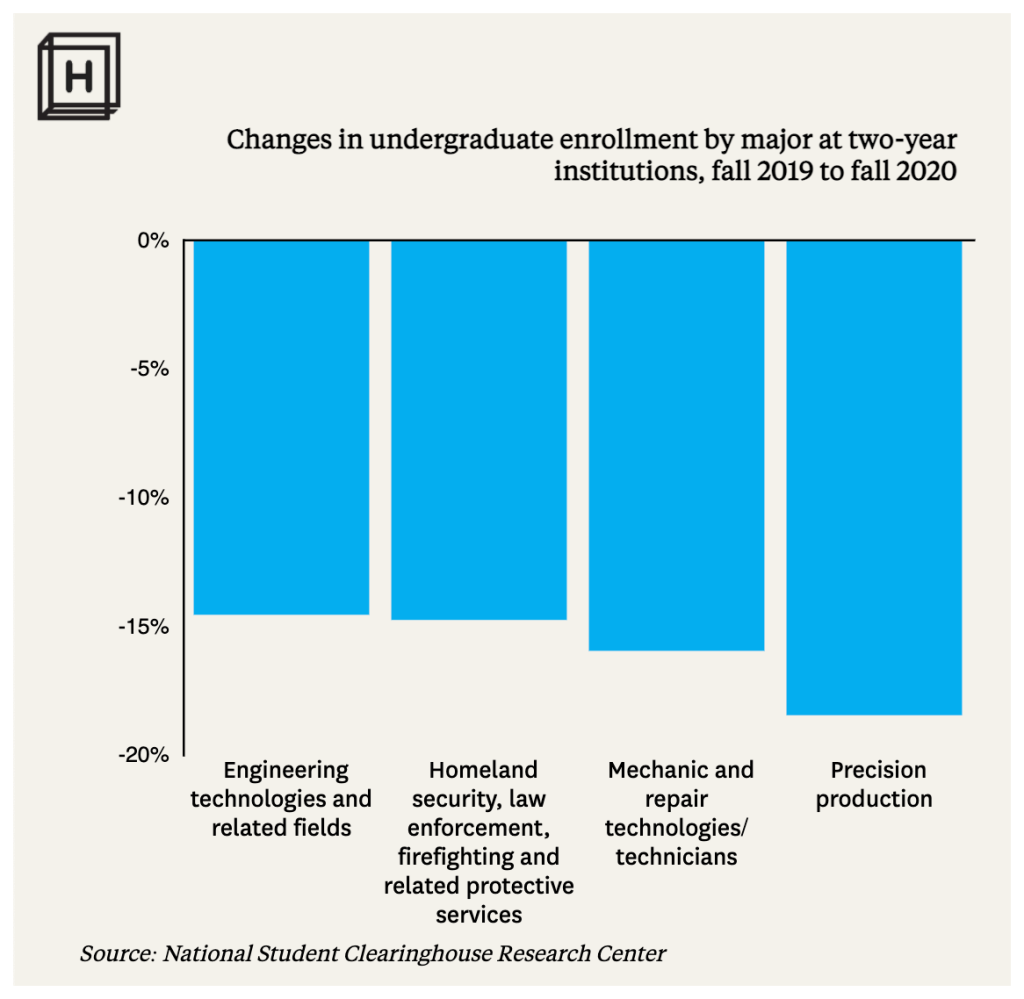
This disinterest in maintenance careers can be attributed to several factors:
- Perception of the industry: Often viewed as less glamorous or promising compared to fields like technology or finance.
- Alternative career paths: Increasing availability of other career options that are perceived as more lucrative or fulfilling.
- Lack of awareness: Many young people are not fully aware of the opportunities and advancements in the maintenance field.
- Educational trends: A shift in educational focus towards more digital-oriented careers, away from traditional maintenance roles.
This trend will have far-reaching effects. A talent shortage that is already causing headaches for maintenance and facility managers is bound to lead to higher operational costs which will translate into increased prices for products and services. Reversing this trend will require a broad, strategic approach to make maintenance careers more attractive to the younger generation.
2. The rising importance of basic digital skills
As maintenance departments start digitizing internal processes, workers must become adept at using different digital tools and platforms.
The prime culprit is an increasing adoption of cloud-based maintenance software. These solutions offer a lot of promise in the field of maintenance and can be accessed on phones and tablets, streamlining all aspects of maintenance for technicians directly from the field. However, to reap all of those benefits, staff first need to know how to properly use the software.
On top of that, a growing reliance on predictive analytics, augmented and virtual reality, and other advanced technologies necessitates a workforce proficient not just in basic digital skills, but also in using these sophisticated tools in their daily work.
Here are some strategies that industrial companies are implementing to address the digital skills gap in the maintenance sector:
- Regular training sessions: Offering workshops or online courses to enhance digital literacy among existing staff.
- Digital proficiency in recruitment: Updating job descriptions to include digital skills and incorporating assessments in the hiring process.
- Mentorship programs: Pairing experienced employees with newer staff to facilitate digital skills transfer.
- Partnerships with educational institutions: Collaborating with technical schools and universities to align curriculum with industry needs.
Hopefully, these actions will ensure the maintenance workforce is well-equipped for a more digital environment.
3. Aging workforce and knowledge transfer
An aging workforce in the maintenance sector is a big challenge. With experienced workers nearing retirement, the risk of losing critical knowledge and skills is high. Effective knowledge transfer, mentorship, and succession planning are essential to ensure continuity and preserve this expertise.
Organizations have a few options to do that, each addressing different aspects of the process:
- Developing targeted training programs: Implementing training initiatives to ensure the sharing of expert knowledge and standardization of procedures.
- Creating digital manuals: Assembling knowledge and best practices into digital formats for easy accessibility and reference.
- Mentorship and shadowing programs: Establishing programs where experienced workers guide and mentor juniors, fostering a culture of learning and knowledge sharing.
- Integrating maintenance software: Utilizing maintenance software as a key tool within these strategies, particularly for recording and sharing expert knowledge. This will also help maintain consistency in maintenance practices and procedures.
Using a mix of these strategies will ensure you preserve the vital knowledge within your organization.
4. The impact of automation and AI
Automation and AI are revolutionizing maintenance work, enhancing efficiency, predicting problems, and helping with resource allocation.
Balancing technology and the human workforce in maintenance involves addressing several challenges and seizing opportunities:
- Training for new technologies: Equipping workers with the skills to handle advanced technologies and automation.
- Job role redefinition: Adjusting job descriptions to reflect the integration of technology in maintenance tasks.
- Human-technology collaboration: Finding ways for workers and automated systems to complement each other effectively.
- Addressing job displacement concerns: Implementing strategies to reskill workers whose roles are affected by automation.
Preparing the workforce for a technologically integrated future involves targeted training and education initiatives. Developing adaptability and skills in areas like data analysis and machine learning is the right step toward equipping the workforce to thrive in this new landscape.
5. Greater emphasis on interdisciplinary skills
As the equipment and systems used in various industries get more complex, so do the skills required to maintain them. This trend is driven by technological integration, where mechanical systems are increasingly combined with electronic and digital components. In such a context, maintenance workers need a mix of mechanical, electrical, and basic IT skills to effectively manage modern equipment.
A greater emphasis on interdisciplinary skills will reshape job descriptions and training requirements. Some maintenance roles already demand a combination of mechanical, electrical, and IT skills. This shift will impact recruitment the most, requiring a focus on multi-skilled candidates who understand the interconnectedness of different systems like CMMS, ERP, and more.
6. A shift to more flexible working arrangements
The growing demand for better work-life balance and flexible working conditions is reshaping the maintenance sector. Employees seek arrangements that offer flexibility and support their lifestyle needs.
Flexible working arrangements — although still uncommon in industrial sectors — have a significant impact on scheduling and employee satisfaction. Companies that are able to respond to these preferences with more flexible shifts and remote maintenance capabilities will have a big advantage in attracting and retaining skilled maintenance workers.
Parting thoughts
Responding proactively to these workforce trends is essential for facility and maintenance managers. Staying ahead of the curve, embracing new technologies, and investing in employee development are the key strategies for building a dynamic, skilled, and adaptable maintenance workforce.
Collaboration among stakeholders — including employers, educators, and policymakers — will be key in ensuring the industry’s ability to meet market and operational demands.