Wear and Tear
Everything you ever needed to know about wear and tear
What is wear and tear?
“Wear and tear” describes the gradual deterioration or damage that occurs to a physical asset over time.
Mechanical wear naturally occurs in individual machine parts because of abrasion, corrosion, or damage — even with normal use of your equipment.
However, wear and tear of machines can be slowed down with proactive maintenance and can increase the lifespan of your equipment.
Example of wear and tear of machines
Worn tracks on an excavator are a great example of wear and tear. They operate in harsh, dirty, and wet environments and are subject to severe strain during operation.
Badly worn tracks can impact the operation of the excavator, reducing traction or power and creating safety hazards that may hurt the operator or the machine.
The operator must inspect their tracks regularly to identify cracking and measure wear. Once the tracks reach a certain wear limit, they must be replaced.
Other types of wear you may see in your equipment include:
- Worn ball bearings
- Worn gear teeth
- Worn tire treads
- Lubricant viscosity too thick or thin
Checklist for Creating a Preventive Maintenance Plan
Following a consistent Preventive Maintenance Plan can make life easier. Use this checklist to create your own!
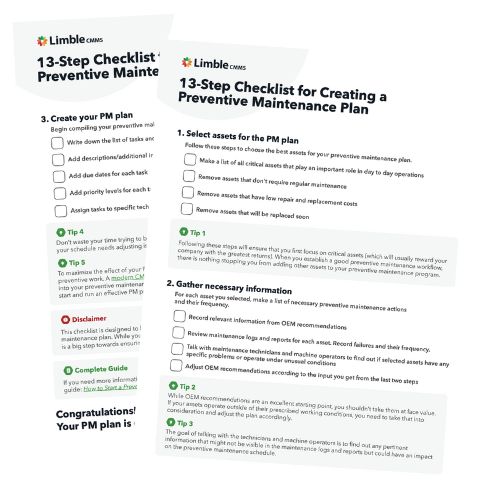
Wear and tear vs. damage
“Damage” refers to harming the condition of an asset due to an:
- Event (flood)
- Action (operator error)
- Inaction (lack of routine maintenance)
Hence, damage falls outside the normal definition of wear and tear — it is not a part of normal operation and lifecycle of properly operated and maintained equipment.
Consider a bearing shell that suffers rubbing, melting, or smearing due to insufficient lubricant, excessive load, or misalignment.
That is classed as damage. An event has caused the bearing’s deterioration, shortening its life and requiring premature replacement.
How does a business treat wear and tear?
Accountants use financial methods to reduce asset values as wear and tear occurs.
Each year of ownership will see the value of an asset reduced because you have used some of its life. It does not have the same value as it did at the time of purchase. (Vehicles are a great example of this).
A reduction in book value by removing a percentage of the asset’s value each year is known as asset depreciation. The asset initially worth $11,000 will be worth only scrap or salvage value after four years.
An example of a straight line equipment depreciation method.
Typically, normal “wear and tear” is explicitly excluded from any warranty claim. After all, it’s not a defect — it’s the normal deterioration expected to occur when the asset is carefully used and maintained.
Your warranty will only be honored if the deterioration experienced is far more extreme than the expected wear and tear.
How to minimize wear and tear
While we can’t prevent wear and tear, we can minimize its impact through correct operation, handling, and maintenance.
Apply proper lubrication and lubricants
Lubricants perform several tasks:
- Create a barrier surface between two friction surfaces
- Help cool the equipment
- Carry away different contaminants
Oils and greases break down due to time, heat, and pressure, losing their effectiveness. This is where asset wear starts to accelerate.
Using the correct, OEM-recommended lubricant, changing the oil and filters at the recommended frequencies, and refraining from using cheap alternatives will allow the asset to operate with minimal wear and tear.
Perform regular preventive maintenance
Preventive maintenance involves the regular inspection and servicing of an asset to slow its rate of deterioration. As equipment wears, deterioration will accelerate further, and the asset’s life will shorten rapidly.
This is why every original equipment manufacturer (OEM) will suggest basic preventative maintenance schedules for their equipment.
Start with these OEM schedules, then adjust them by extending or reducing the frequencies to suit your operation.
Operate assets within their design parameters
Use your machinery only for its designed application and within design parameters like temperature, pressure, or speed.
If you step outside the equipment manufacturer’s intended use, you can expect an increase in asset wear and tear — and a refusal from the supplier should you attempt to claim a warranty on breakages or premature failure.
Monitor the operating environment
The operation and maintenance manual provided by the OEM is a generic document that covers average use.
If you are operating an asset in extreme environments, you must adjust your servicing and maintenance schedule to account for an expected increase in wear and tear.
A simple example is an air filter on a vehicle.
- Regular highway operation: expect to change it at the manufacturer’s recommended service interval
- Off-road use in dusty environments: replace the filter more often
Ensure correct asset handling throughout its lifecycle
Rough handling, poor storage, and improper use will dramatically shorten the lifespan of assets through accelerated wear and tear.
Correct handling techniques will improve operator safety and extend the equipment’s operating life, reducing wear and tear while providing more efficient and effective operation.
Ensure all equipment operators get training in the correct handling, storage, transport, and use of equipment.
Want to see Limble in action? Get started for free today!
Don’t let maintenance tasks wear you down
The degree of wear and tear of machines in your organization is directly influenced by how well you treat your equipment.
Use poor practices, and you can expect to spend more on maintenance, suffer reduced availability and operation, and decrease the useful life of your assets.
Make sure that doesn’t happen by implementing a modern CMMS like Limble. Start a free trial or request a product demo and get on top of your maintenance tasks.