CNC machines have made manufacturing easier, faster, and more precise. Supported by the development of IoT technology, the CNC machine market is set to experience significant growth.
Join us as we discuss the importance and intricacies of proactive CNC machine maintenance, list common challenges you’ll need to watch out for, and share our best tips for staying on top of CNC machine maintenance.
The importance of proactive CNC machine maintenance
CNC (or Computer Numerical Control) machines are a critical piece of equipment in many manufacturing facilities. When a CNC machine breaks down or experiences a severe fault, the whole manufacturing process has to be halted till the problem is rectified. Unexpected manufacturing downtime reduces productive output, leads to excessive idle time, and causes bottlenecks in the supply chain.
Regular CNC machine maintenance. Source: ExportersIndia
With time, CNC machines that are not regularly maintained will start to output products of lower quality. You can avoid all of that by placing your CNC machines on an adequate preventive maintenance regimen. As an added bonus, a well-maintained machine will spend less energy and have a longer useful life.
Common CNC maintenance challenges
The operations of a CNC machine comprise of:
- Mechanical components
- Electrical equipment
- Electronics components
- Software
CNC machines have lots of moving parts and sensitive mechanical components which require precise maintenance work. In addition to that, you have to ensure the electrical, electronic, and software elements all work as expected.
CNC machining requires precise operations with resolution in the range of 0.0001”. It goes without saying that a machine has to be in excellent condition to deliver such precise outputs.
Here are some of the more common CNC maintenance challenges you need to watch out for.
Time constraints
Regular maintenance of CNC machines is critical to prevent unexpected machine downtime and the associated harmful effects. However, CNC machines are a critical part of the manufacturing process and their inactivity reduces production output.
While scheduling planned downtime is recommended, plant managers might try to postpone routine maintenance tasks to reach certain production numbers. This a common cause of friction between production and maintenance teams.
There is no perfect solution here. Planned downtime is necessary, but the intervals are up for debate. When possible, organizations should try to schedule maintenance around working hours.
Excessive machine vibration
CNC machines need to be extremely precise. Excessive vibrations will introduce error in the final product. These vibrations are often the result of improper installation or faulty components. They need to be investigated and fixed to ensure machine precision.
The root cause of machine vibration (faulty components, inadequate grip of chuck and fixtures…) has to be nipped in the bud before it compounds to functional failure or causes a whole line of defective products.
Overheating
When CNC machines are pushed beyond their limits, various components can overheat. This is a common problem when manufacturers take more orders and machines have to be overworked to meet the orderbook. That being said, the same can happen due to an inadequate coolant level or a fault in coolant delivery.
Nevertheless, overheating accelerates the speed of wear and tear of machine components, reducing their useful life and increasing your spare parts expenditures.
Software issues
Software is integral for smooth operation of CNC machines. There are many software issues that can negatively affect machine output:
- Improper synchronization of the software with the CNC machine
- Alignment and indentation errors caused by inaccurate software calibrations
- Error in handling software, especially by untrained employees
Power supply issues
CNC machines require precise power input to each component to function properly. If there is any error in the overall power input (trouble with power socket, internal inverters, etc.), the output of the machine will be affected.
Sometimes, all mechanical components can work as expected, but faults in the electrical supply introduce defects in the output.
Checklist for Creating a Preventive Maintenance Plan
Following a consistent Preventive Maintenance Plan can make life easier. Use this checklist to create your own!
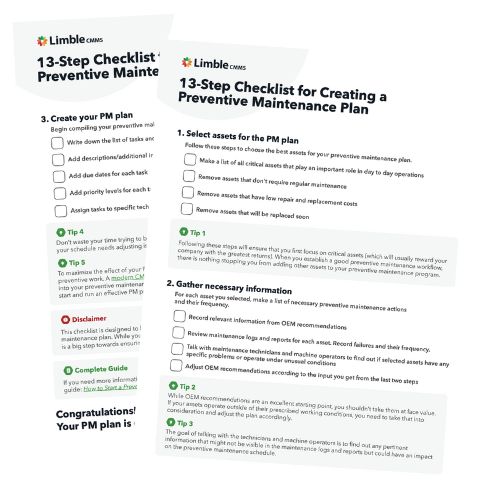
Tips and best practices for the maintenance of CNC machines
You should be very diligent when it comes to planning and executing the maintenance of CNC machines. Here are some additional tips and best practices:
- Maintain thorough maintenance records. Cloud-based CMMS software like Limble will help you automate data collection and ensure quick and easy access to maintenance history for each of your machines.
- Ensure adequate employee training. Make sure that people who use, maintain, and interact with CNC machines are adequately trained for their levels of responsibility.
- Ensure that the machine operates in a clean environment. Accumulating dust and debris cause machine degradation. CNC machines, as well as the space they operate in, should be regularly cleaned.
- Keep an eye out for anomalies in machine operations. These could be machine vibrations, anomalous sounds, etc. Train employees to note and report such anomalies.
- Schedule regular breaks in CNC machine operation. When machines run incessantly, they are more likely to overheat and suffer serious damage. Establish standard breaks for CNC operation.
- Create standard operating procedures and maintenance checklists to ensure the machine is properly operated and maintained.
Let’s focus more on this last bullet point list in the next section.
CNC machine maintenance checklists
Maintenance checklists help technicians and operators perform their tasks safely and efficiently.
The following sections cover the maintenance tasks that should be performed at different times (daily to annually). These checklists assume that CNC machines undergo eight hours of operations every day, with sufficient breaks.
You need to adjust the time period of your maintenance in accordance with usage hours, after consulting with machine OEM guidelines. Use the following checklists as a starting point to create a preventive maintenance plan that takes into account the needs and requirements of your manufacturing operation.
Daily maintenance checklist
The following tasks have to be done every day, assuming regular usage hours:
- Inspect the pressure and level of lubricant. Top up if required.
- Check coolant level. Use a coolant refractometer to ensure coolant and oil ratio is maintained.
- Clean out the coolant disposal tray.
- Check for moisture in pneumatic air. Drain moisture if it is detected.
- Check pressure of pneumatic air with the pneumatic pressure gauge.
- Wipe the complete machine with a clean rag.
- Check the output of the voltage stabilizer. Ensure it adheres to the required specifications.
- Check panel cooler temperature.
- Observe noises, bangs, or any other anomalies in machine operation.
- Watch out for for any overheating signs during machine operation.
Weekly maintenance checklists
The following maintenance tasks have to be done on a weekly basis:
- Clean the complete machine shop, especially the area surrounding the machine.
- Check for any evidence of lubricant, oil, or coolant leakage.
- Check and ensure all cooling fans are working properly. These include spindle motor fans, cooling system fans, and hydraulic motor fans.
- Perform visual inspection of machine components. Apply grease or appropriate lubricant to parts that seem dry.
- Check whether tool heads are held securely in the tool changer.
- Lubricate v-groove, plungers, slider cap, extractor forks, keys, and springs of the tool changer.
- Check if all electrical components such as switches and lights are working properly.
Monthly maintenance checklists
Maintenance checks that should be done every month include the following:
- Clean out the chip collector close to the coolant tank.
- Inspect, remove, and adjust jaws, chucks, and fixtures.
- Clean or replace air filters as required.
- Check the condition of tool heads and change them if necessary.
- Inspect, lubricate, tighten, and adjust chains and conveyors in the machine.
- Clean various fans of the machine to prevent dust accumulations.
- Inspect the logs of oil, lubricant, and coolant. Check for any anomalous consumption.
- Clean radiator grills of dust and debris.
Annual maintenance checklists
CNC machine maintenance checks that need to be done annually:
- Remove coolant cylinder tank for inspection.
- Clean out the coolant cylinder for debris, inspect for bacteria or fungal growth, and clean the tank.
- Drain used lubricant, clean lubricant housing, and refill it.
- Inspect for presence of contaminants in pneumatic oil. Change it if required.
- Replace all oil filters.
- Run software simulations to check the alignment and indentation of tools.
- Use software to quickly reverse the axis of the toolhead to check for backlash. If the toolhead experiences a backlash effect, further maintenance is required.
Use CMMS software and stay on top of machine shop maintenance
Planning and organizing machine tools maintenance is too important to do be done haphazardly. At the very minimum, you should be able to schedule the right amount of preventive work, manage spare parts inventory, have quick access to maintenance history, and be able to track machine condition in real-time.
You can do all of that and much more with Limble CMMS. Let us help you become more precise with your maintenance work. Request a demo today.