Emergency Maintenance
Everything you ever needed to know about emergency maintenance
What is emergency maintenance?
Emergency maintenance is a reactive maintenance approach aimed at addressing unexpected malfunctions or equipment failures. The goal of emergency maintenance is to return malfunctioning equipment to normal working conditions as quickly and safely as possible. Beyond restoring equipment to proper working order, the imperative of emergency maintenance is to reduce the likelihood of recurrence and take steps to extend the lifespan of the asset in question.
As with preventive maintenance, an effective emergency maintenance policy should include comprehensive training, clearly articulated standard operating procedures (SOPs), and proper safety protocols. The effectiveness of your emergency maintenance strategy will depend largely on the preparation that you put into it before emergencies occur.
It’s also important to ensure that your maintenance technicians are prepared to act quickly and decisively in a wide range of scenarios.
Reactive to Preventive Maintenance Transition Guide
How to plan your transition to Preventive Maintenance and avoid the common pitfalls while implementing a PM program
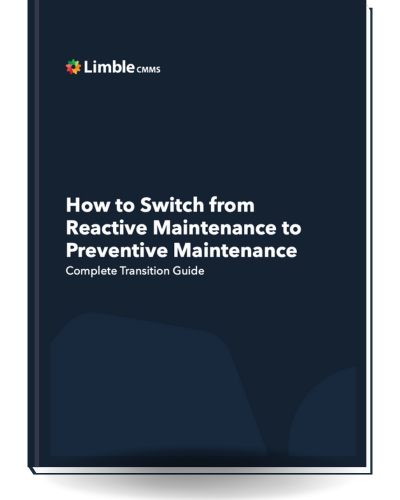
Table of Contents
- Everything you ever needed to know about emergency maintenance
- What is emergency maintenance?
- Why is Emergency Maintenance Important?
- Emergency maintenance vs. corrective maintenance and reactive maintenance
- Tips for effective emergency maintenance programs
- Avoiding common maintenance emergencies
- Related Content
Why is Emergency Maintenance Important?
Implementing proactive maintenance strategies may help your organization reduce the likelihood and frequency of emergencies, but no amount of prevention is 100% foolproof. To the point, let’s first consider a few hypothetical scenarios in which emergency maintenance might be required.
- The air conditioning unit in your healthcare facility overloads during a heat wave, compromising the health, safety, and comfort of your patients.
- An unexpected power outage in your company’s data center leads to data loss, disrupted services, and significant financial costs for your clients.
- A broken water main under an office building causes massive water damage, electrical hazards, and potential safety risks for employees.
In each of these examples, it’s not clear that there are any steps your maintenance personnel might have taken to prevent the emergency events that transpired. It’s only clear that these situations require rapid response and effective resolution. This is why it’s so important for your organization to adopt proven strategies for addressing emergency maintenance needs.
In the guide that follows, we’ll discuss the vital role of emergency maintenance in your overall asset management strategy and we’ll discuss the benefits of a structured emergency maintenance plan.
Common emergency maintenance scenarios
The following are some common emergency maintenance scenarios that might require the immediate attention of your maintenance personnel.
- Unexpected equipment failures can halt production, lead to prolonged downtime, and cause financial losses.
- Immediate safety hazards such as gas leaks, faulty electrical wiring, or structural damage, can cause accidents, injuries, and fatalities.
- Environmental control failures, such as HVAC system breakdowns, can impact the health, safety, and comfort of occupants and cause damage to products and equipment.
- Utility disruptions, such as broken water lines, electricity blackouts, and damage to your natural gas line, may cause the suspension of operations throughout your facility.
- IT outages can disrupt internal communication systems, impede customer service, prevent the completion of financial transactions, and compromise data security.
Typical workflow for addressing emergency maintenance
While specialized training is required to prepare your maintenance team for the full range of possible emergency incidents, there should also be some common protocols in place for addressing emergencies of every kind.
One way to ensure an effective emergency management strategy is to establish a clear workflow for addressing emergency maintenance tasks. A typical workflow for handling emergency maintenance tasks may include the following steps:
- Detection, which may be initiated using condition-monitoring technology, routine inspections, or direct observations from team members.
- Emergency maintenance requests, ideally through dedicated channels to initiate action from your organization’s designated emergency response unit.
- Initial assessment, with designated personnel evaluating the incident to determine its severity and its potential impact on the safety and operational capacity of your workspace.
- Resource allocation, mobilizing the necessary personnel, tools, and spare parts needed to complete emergency repairs.
- Communication, ensuring emergency maintenance personnel are briefed on the nature of the issue, are given clear instructions for resolving the problem, and fully understand the safety protocols in place.
- Emergency repairs, with an initial emphasis on restoring malfunctioning equipment to immediate working condition, whether employing temporary or long-term solutions.
- Root Cause Analysis (RCA), using real-time data, maintenance records, and failure mode analysis to identify the source of the breakdown.
- Comprehensive repairs, aimed at addressing root causes, imposing long-term solutions, incorporating additional safeguards, and preventing recurrence.
- Verification and testing to ensure the system or equipment is operating correctly, safely, and in a manner that reduces the likelihood of recurrence.
- Documentation, including detailed records of the incident, actions taken, resources used, and outcomes yielded.
- Post-incident review, identifying areas for improvement, updating emergency maintenance protocols if necessary, and using lessons learned to promote continuous improvement.
Types of emergency maintenance
The workflow outlined above is applicable across a wide variety of industries. However, many emergency maintenance functions are industry-specific. For instance:
- Manufacturing industry maintenance teams must be prepared for the sudden breakdown of critical equipment. Unexpected failure of production machinery or assembly line robotics can bring production to a standstill and, consequently, cascade into production loss, missed delivery deadlines, and a diminished reputation with clients.
- Production facility maintenance teams must be fully trained to handle hazardous chemical leaks or spills, which can pose health risks to employees, threaten environmental contamination, result in facility shutdowns, and trigger regulatory penalties.
- Power plant maintenance teams must be prepared for the sudden breakdown of heavy-duty equipment such as turbines, transformers, and circuit breakers. When these components fail, they can impact many thousands of residential, commercial, and industrial customers. Prolonged disruptions in electrical services can lead to massive amounts of lost productivity, widespread health and safety risks for the populations impacted by outage, and legal liability as a consequence of these events.
- Data service center maintenance teams must have the knowledge and technological understanding to manage application crashes and lead efforts to recover data and functionality. When data servers or applications crash unexpectedly, the results may include service outages, data loss, and security breaches, as well as diminished customer dissatisfaction and financial losses.
- Airline maintenance teams have the vital responsibility of managing aircraft mechanical failures whether they occur in-flight or on the ground. These emergency incidents can lead to flight delays and cancellations or, in more extreme circumstances, safety risks, emergency landings, and potential loss of life.
Emergency maintenance work orders vs. proactive work orders
Emergency maintenance is inherently reactive. That means emergency maintenance tasks are only triggered in reaction to equipment malfunction or failure. This differs from forms of maintenance such as preventive maintenance, predictive maintenance, and condition-based maintenance. Each of these is a proactive strategy, which means that the methods employed are meant to reduce the likelihood and frequency of failure events and preempt emergency incidents.
Given these important distinctions, there are some fundamental differences in how emergency work orders are issued and managed relative to the tasks associated with proactive maintenance strategies.
- Emergency Maintenance Work Orders are triggered by indications of equipment malfunction or failure, whether through direct observation, formal report, or quality assessment.
- Preventive Maintenance Work Orders are planned and scheduled in advance and are typically generated by a maintenance management system.
- Predictive Maintenance Work Orders will be generated based on the actual condition of equipment and will therefore be triggered by data analysis and predictive models indicating potential issues and sources of future failure.
- Condition-Based Maintenance Work Orders are performed based on the real-time data from condition-monitoring tools and techniques and will therefore be triggered by specific condition thresholds or deviations from normal function.
Core components of an emergency maintenance program
Emergency repairs are typically conducted under less-than-ideal conditions. Maintenance workers face added pressure to complete their work quickly, safely, and successfully. It’s important to support your maintenance team with a clearly-articulated emergency maintenance program. At a minimum, this program should include the following core components:
- Emergency response plan that includes clearly defined procedures for identifying, reporting, assessing, and responding to emergencies; delegates specific roles and responsibilities; and establishes channels for timely and effective communication during emergency maintenance situations.
- Continuous training and education on internal emergency protocols and standard operating procedures; instructions for handling hazardous materials or malfunctioning equipment; and up-to-date information on regulatory conditions and compliance responsibilities.
- Streamlined resource management including an updated inventory of spare parts and tools; a real-time look into stock levels; and strong, stable supplier relationships.
- Comprehensive safety protocols including guidelines on the proper use, storage, cleaning, and maintenance of Personal Protective Equipment (PPE); procedures for hazard identification and risk assessment; and industry-specific safety standards.
- Advanced maintenance management software, which can help you track, manage, and prioritize emergency work orders; implement condition monitoring systems; automate inventory functions, and more.
Emergency maintenance vs. corrective maintenance and reactive maintenance
Emergency maintenance, much like corrective maintenance and reactive maintenance, is only triggered after equipment malfunctions or fails. There are, however, several important distinctions between emergency maintenance and these other terms.
- Emergency maintenance describes an urgent response to a failure or breakdown, one that poses an immediate and significant risk to safety, productivity, or the longevity of the assets themselves. The goal of emergency maintenance is to restore equipment to normal functionality and minimize the severity of impact.
- Corrective maintenance is likewise performed after a fault is detected and with the same aim of restoring equipment or systems to proper working conditions. In contrast to emergency maintenance, corrective maintenance lacks urgency. Corrective maintenance issues will typically be identified, assessed, and scheduled for repair.
- Reactive maintenance is an umbrella term that encompasses both emergency and corrective maintenance. Like the aforementioned terms, reactive maintenance refers to repairs that are triggered only after equipment or systems have failed. The resulting repairs can include both emergency and non-emergency repairs.
It is also worth noting that reactive maintenance may be used as a default term to describe maintenance programs that do not employ preventive maintenance strategies, and which therefore are more likely to be tasked with both emergency and corrective maintenance tasks.
Tips for effective emergency maintenance programs
You may not be able to predict emergencies, but you can prepare for them. There are a number of steps you can take to ensure that your maintenance team is ready to handle any emergency quickly, accurately, and safely. Below, we spotlight a few best practices that can help your maintenance team mount more effective emergency response efforts:
- Enhance your training program by conducting regular drills simulating various emergency scenarios; encouraging personnel to seek emergency response and safety management certifications; and cross-training employees in multiple emergency management skills to ensure flexibility and availability during emergencies.
- Streamline internal communication by establishing clear protocols for reporting and responding to emergencies; setting up dedicated emergency hotlines or communication channels; and implementing systems for instant alerts (SMS, email, app notifications) to quickly notify relevant personnel of emergencies.
- Invest proactively in technology including predictive IoT sensors; automated preventive maintenance scheduling tools; and advanced data analytics to reduce the likelihood and severity of emergency incidents.
- Conduct regular inspections and audits to identify and address potential issues before they escalate into emergencies, and periodically invite independent third-party auditors to provide objective findings on the condition and functionality of your physical assets.
- Utilize maintenance management software to track emergency work orders, compile data on equipment performance, ensure the availability of critical inventory, receive customized alerts, and more.
Want to see Limble in action? Get started for free today!
Avoiding common maintenance emergencies
In a recent webinar, we discussed effective strategies for avoiding common maintenance emergencies. Below are a few key insights from this illuminating discussion.
- Preventive Maintenance (PM) strategies such as routine scheduled maintenance, regular system checks, and equipment cleaning can help maintenance teams identify and address potential issues before they escalate into emergencies.
- Advanced Predictive Maintenance (PdM) technologies can be used to monitor equipment performance in real time, better anticipate potential failures, and intervene before they become emergency maintenance issues.
- Effective spare parts inventory is essential to ensure that your maintenance team has timely access to the tools, materials, and parts required to handle repair tasks.
- Continuous training is vital to a successful proactive maintenance strategy and ensures that your maintenance technicians remain current on the newest technology, industry best practices, and regulatory conditions.
- Leading-edge technology like Limble’s Computerized Maintenance Management Systems (CMMS) can help streamline maintenance processes, automate work order management, document equipment history, automate preventive maintenance scheduling, and more.
With additional features like automated inventory management, real-time monitoring, and integrative versatility, Limble’s CMMS is an invaluable tool for better managing emergency maintenance tasks and, just as importantly, an invaluable tool for preventing emergency maintenance incidents from happening in the first place.
To learn more, we encourage you to check out the whole Webinar here.