Lean Manufacturing
Lean manufacturing processes focus on reducing waste, delivering value to customers, and enabling continuous improvement.
What is lean manufacturing?
Lean manufacturing is a production philosophy that aims to minimize waste while maximizing productivity and customer satisfaction. “Going lean” may involve implementing a number of different productivity-driving methods and tools to achieve continuous improvement.
A brief history of lean manufacturing
The principles behind lean manufacturing have their origins at Toyota. Taiichi Ohno’s work to develop the Toyota Production System helped the auto manufacturer set itself apart from competitors in Japan and across the globe. In 1990, James Womack’s book The Machine that Changed the World introduced Toyota’s methodology to a wider audience and popularized the term lean production.
Toyota later codified the principles behind their unique culture and approach to production. Published in a book titled The Toyota Way, they include:
- Managers should prioritize the long term when making decisions, even at the expense of short-term profits.
- Through continuous improvement (kaizen), processes should eliminate sources of waste (muda) like overproduction and downtime.
- Balancing workloads (heijunka) helps to avoid uneven production levels (mura) and overburdened people or equipment.
- While you should spend time deliberating on decisions and consider every option, you should act on your decisions quickly.
- You should emphasize professional development to build effective teams and foster an excellent culture.
- Rather than chasing the latest technology trend, you should take care to leverage only tested, trusted tools.
The 5 principles of lean manufacturing systems
At its core, successful lean manufacturing relies on a five-step process for implementing core principles:
- Defining value
- Mapping the value stream
- Creating flow
- Establishing a pull system
- Seeking perfection through continuous improvement
Defining value
Lean thinking emphasizes the need for understanding your customer’s unique definition of value. The meaning of value goes far beyond price. Your conception of value should take everything your customer is willing to pay for into account.
Mapping the value stream
Next, lean enterprises map out their value streams. This should factor in all of the processes that turn your raw materials into finished products. The goal of value stream mapping is to determine which processes bring value to the customer and which ones contribute to waste.
Creating flow
Once you’ve eliminated unnecessary waste, it’s time to establish flow between your remaining production processes. Creating continuous flow involves addressing delays, mistakes, downtime, and other disruptions at their source.
Establishing a pull system
A push manufacturing system produces a certain quantity of products for storage. Lean manufacturing works on a pull system, aiming to limit inventory. Pull-based manufacturing synchronizes raw material inputs on a just-in-time (JIT) basis to meet customer demand. Managing a pull system requires close communication with suppliers and customers combined with efficient processes and well-trained teams.
Seeking perfection through continuous improvement
The lean mindset instills the value of small, incremental changes. You should encourage each member of your team to commit themselves to improving workplace culture and production performance.
Lean manufacturing eliminates 8 types of waste
Lean thinking views any process or task that fails to provide value for customers as wasteful. Some waste is unavoidable. You cannot eliminate sources of necessary waste, but lean principles demand that you eliminate all sources of unnecessary waste.
- Unnecessary transportation: Wasteful transportation can lead to handling damage, create bottlenecks in the production flow, and contribute to poor communication. One way to remove unnecessary transportation is to map out raw material and parts through your facilities. Ensure that flow is product oriented, that overall travel distance is minimized, and that your team is not involved in non-value-adding tasks.
- Overproduction: It’s nice to sit on a surplus, but overproducing can deplete essential resources and cost you money. Lean manufacturing calls for producing just what the customer demands.
- Unnecessary motion: Unnecessary, repetitive movements can affect employee health and productivity. When your team is uncomfortable they are more likely to mishandle products and contribute to quality concerns. Try mapping the tasks necessary for each process to identify sources of unnecessary bending, stretching, lifting, or walking. Talk to your operators to get their input on how you can make them safer, more comfortable, and more efficient.
- Excess inventory: Poor planning, inefficient changeover times, and unbalanced production processes can all leave you dealing with excess inventory. Carrying more inventory than necessary ties up resources and could pose a host of additional costs. You can avoid excess inventory by streamlining production flows and introducing just-in-time delivery for raw materials.
- Idle time: Wait time adds up when production events are poorly synchronized. This reduces throughput and can lead to unnecessary expenses. To address excess waiting, you need to track the issue to its source. Poor equipment maintenance, missing tools, or process inconsistencies could be causing your trouble.
- Overprocessing: You should strive to eliminate any redundant tasks that don’t contribute to the value of your product. Mapping out your process should highlight repetitive, unnecessary, or unclear tasks that could contribute to waste.
- Defects: When products fail to meet the necessary specifications, you’ll need to spend time and money scrapping, reworking, or repairing them. Lean manufacturing aims for zero-defect production. Root cause analysis can help to pinpoint the causes of defects so you can take corrective steps.
- Unutilized and underutilized talent: Poor talent utilization can lead to excess labor costs and leave your team struggling to meet its goals. Regular talent mapping and frequent conversations with employees can help you gauge their satisfaction and identify instances of underutilization. Supervisors should always seek out opportunities to improve processes and better harness the talents of their teams.
Lean manufacturing principles help businesses address all sources of unnecessary waste.
The Essential Guide to CMMS
Download this helpful guide to everything a CMMS has to offer.
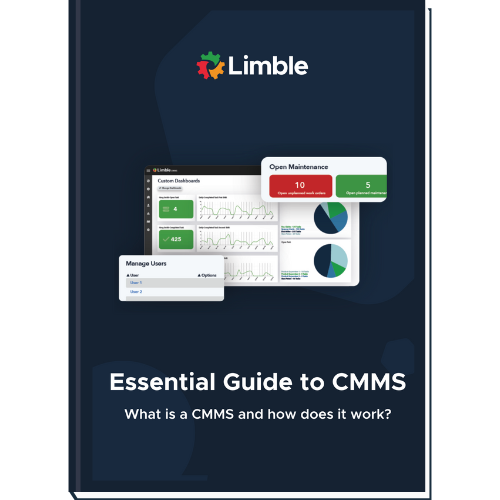
Lean manufacturing tools and techniques
As more and more industries have embraced the lean mindset, they’ve developed a broad range of tools and techniques for applying lean principles to their unique production processes. These are just a few of the ways you might introduce process improvements and build a culture of continuous improvement:
- 5S: This organizational method contributes to safe and uncluttered facilities. In addition to preventing accidents, it boosts efficiency and productivity.
- Single-Minute Exchange of Die (SMED): If changeover times are affecting your overall equipment efficiency (OEE), implementing SMED could help. The process involves breaking down each step of the changeover process into elements. External elements are those that operators can carry out while the equipment is operational. Internal elements, on the other hand, are those that require a shutdown. Once you’ve broken the process down, analyze its elements. By identifying opportunities for transferring internal elements to external ones you can potentially streamline the process.
- Kanban: Developed by Toyota in the early days of lean manufacturing, kanban helps to visualize workflows to optimize quality control, resource allocation, and efficiency.
- Poka-yoke: This Japanese term means “preventing inadvertent errors.” As a philosophy, it means identifying and correcting errors as they occur rather than inspecting for them after the fact.
Establishing a lean production process
10 steps for introducing a lean production system to your business.
Introducing a lean management system for your manufacturing operation does not necessarily mean overhauling your entire organization. Lean production is more than just a set of tools and techniques – it’s a mindset.
These steps can help you carefully and strategically establish lean processes and instill the principles of lean manufacturing across your organization:
- Deploy your strategy: Start by choosing a small number of production processes with room for improvement. Develop a set of relevant metrics and goals for each process. Make it clear how you’ll apply lean principles, how you’ll measure success, and how you’ll iterate on performance data.
- Map the value stream: Analyze your current processes and identify sources of waste. Next, draw a future state map to illustrate what you’d like to see. Then, develop an implementation plan for reaching this future state.
- Organize your workspaces: Cleaning and reorganizing makes it easier to locate essential items and keep core processes running smoothly. It keeps your team safer too!
- Review your process flow: Identify bottlenecks and waste in your process flow. Next, change the design to facilitate improvements.
- Target process downtime: Causes of process downtime may include changeovers, shutdowns for routine maintenance, wait time, or equipment failure. Analyze these potential causes and develop an iterative process for correcting them.
- Implement a pull system: Allow process station demand and customer demand alone to drive your material flow.
- Level workflows: Work to develop a balanced workload in which average production quantities meet customer requirements while avoiding peaks and troughs.
- Standardize your work processes: Alongside your employees, develop best practices with the appropriate documentation and SOPs.
- Introduce processes for continuous improvement: Educate your team on the value of continuous improvement and begin introducing processes to promote it.
- Partner with your suppliers and customers: Work with suppliers and customers to make your entire supply chain more lean.
Remember that incremental improvement is at the heart of lean manufacturing. You don’t need to optimize your processes overnight to create a more lean production environment.
Want to see Limble in action? Get started for free today!
Lean manufacturing and lean maintenance
Your approach to maintenance and your approach to manufacturing go hand in hand. Introducing a computerized maintenance management system (CMMS) can smooth the transition to more proactive processes and establish a culture that embraces lean thinking.
Start your free trial of Limble today or schedule a free demo to learn more about how our platform paves the way for process improvement, downtime reduction, and a less reactive, more productive team.