On Time Delivery
Measuring on-time delivery tells you how effectively a manufacturing operation sticks to its production and delivery schedules.
What is on time delivery?
On-time delivery is an important metric for understanding and improving the efficiency of manufacturing, warehousing, and supply chain management operations. It describes the total number of orders completed before their promised delivery date within a given period. Tracking the OTD metric offers valuable performance insights for ensuring your team and your assets consistently deliver on your maintenance KPIs.
Table of Contents
- What is on time delivery?
- OTD in Manufacturing
- Checklist for Creating a Preventive Maintenance Plan
- How do you calculate on-time delivery ratios?
- Why is tracking on-time delivery performance important?
- How does on-time delivery relate to maintenance?
- Tips for improving on-time delivery metrics
- The Essential Guide to CMMS
- FAQ
- Related Content
OTD in Manufacturing
For courier services, shippers, and other logistics providers, on-time delivery refers to packages making their ways to customers’ homes. In a manufacturing context, however, successful “delivery performance” could mean a number of things. Delivering could mean sending out a shipment to a customer as well as creating a product or completing a project.
Checklist for Creating a Preventive Maintenance Plan
Following a consistent Preventive Maintenance Plan can make life easier. Use this checklist to create your own!
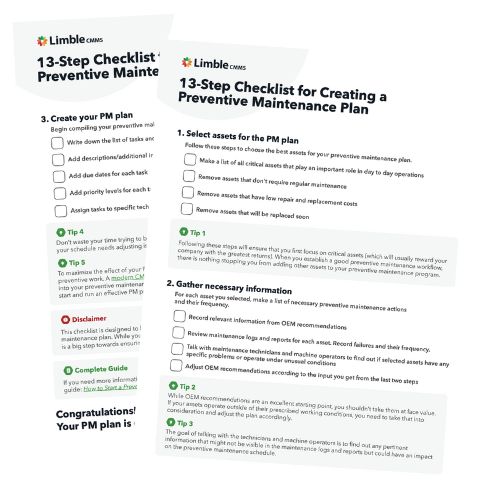
How do you calculate on-time delivery ratios?
You can calculate your on-time delivery rate by first determining the number of on-time deliveries within a specific time frame. Next, you’ll divide this by the total number of deliveries you forecasted or promised to customers. Multiplying this figure by 100 gives you a ratio of on-time deliveries compared to total or expected deliveries.
OTD formula
On-time delivery rate = Total number of on-time deliveries/total number of deliveries x 100
Let’s say you completed 500 projects over a month. During this period, you experienced 50 “late deliveries” by failing to hit your due dates. You ultimately completed 450 projects on time.
450 on-time deliveries/500 total deliveries = .9
.9 x 100 = 90% OTD rate
By following the above formula, we can determine that your on-time delivery rate was 90% for this month. If you completed every project on time during the following month, your OTD rate for the year would rise to 95%.
Why is tracking on-time delivery performance important?
When it’s connected to goals, OTD data is useful for better understanding both internal performance and your suppliers’ ability to meet your needs.
OTD as a Key Performance Indicator (KPI)
You can use OTD data to track the performance of processes and teams within your organization. Digging into low OTD numbers and conducting a root cause analysis is helpful for addressing sources of trouble.
Tracking on-time delivery can also offer insights into your suppliers’ performance. How does their delivery service and the customer experience they offer compare to your standards? When suppliers consistently come up short, it may be time to look into competitors who can better meet your needs. Take care to carefully consider how you’ll balance pricing with customer service in selecting suppliers.
The consequences of low OTD
Consistently low OTD rates can cause problems across a manufacturer’s supply chain. If you’re late in fulfilling customer orders, you’ll risk damaging your relationships and losing business. As public-facing customer complaints accumulate and your reputation suffers.
Late deliveries can become a habit. As your team gets more and more accustomed to underperforming, you may find it increasingly difficult to enforce compliance to established best practices and improve your OTD numbers.
Over time, you may struggle with staff retention if your organization is known for late deliveries and unsatisfied customers. If your OTD numbers are consistently low, chances are your teams are dealing with stress and failing to deliver on other goals.
How does on-time delivery relate to maintenance?
Consistent problems with OTD or failure to execute on delivery-related KPIs could point to problems that more effective and proactive maintenance can help fix.
What’s causing your OTD rates to suffer? Maybe critical pieces of equipment break down too often and cause production bottlenecks. This could result from problems like inefficiencies in your maintenance scheduling or insufficient training for your technicians.
Combined with route optimization efforts and an emphasis on supply chain efficiency, improvements to maintenance operations can have dramatic improvements for order management, delivery performance, and customer satisfaction.
Want to see Limble in action? Get started for free today!
Tips for improving on-time delivery metrics
The following best practices can help your organization improve on-time delivery rates and execute on delivery-related KPIs.
Transition from reactive to proactive maintenance
Taking more proactive steps to keep assets performing effectively and refine maintenance processes can support high OTD by eliminating bottlenecks and other sources of slow-down. Make the switch to preventive maintenance strategies and you’ll see benefits across the organization including reduced maintenance costs, more efficient processes, and a more engaged, productive team.
Develop effective maintenance training programs
Dependable training programs and materials are an essential component of any effective preventive maintenance program. Instilling the right values early and investing in professional development will pay off in a productive, efficient, motivated, and safe team.
Emphasize the value of communication
Encourage your employees to share best practices with each other and continually share their feedback on your policies, priorities, and standard operating procedures. Look for opportunities to engage your suppliers and customers too – what do they have to say about the state of your supply chain?
Analyze, refine, and improve consistently
Maintenance and programs shouldn’t be static. Your organization’s needs, resources, and goals will evolve over time and so should your approach to promoting success. A culture of continuous improvement helps encourage functionality, efficiency, and cost reduction.
Keep OTD rates high with a CMMS
Introducing a computerized maintenance management system (CMMS) empowers the unsung heroes in maintenance to track their performance in real time to make data-driven insights that help the whole business achieve its inventory management and order fulfillment goals.
Learn more about the value of boosting visibility, simplifying reporting, and automating key processes in our essential guide to CMMS platforms.
The Essential Guide to CMMS
Download this helpful guide to everything a CMMS has to offer.
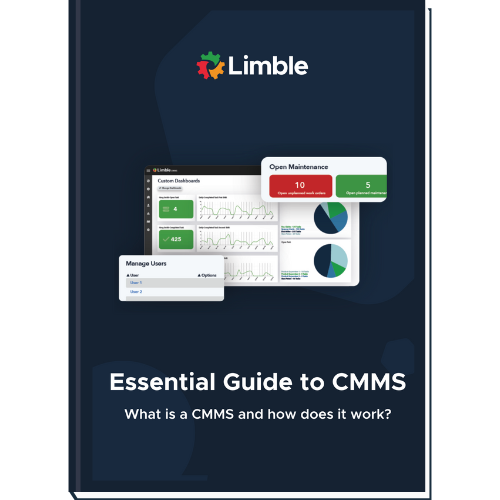
FAQ
Why use CMMS software to track maintenance metrics?
Using CMMS software simplifies tracking complex maintenance metrics, fosters data-driven decisions, enhancing efficiency, reducing downtime, and aiding in regulatory compliance all in one.
Table of Contents
- What is on time delivery?
- OTD in Manufacturing
- Checklist for Creating a Preventive Maintenance Plan
- How do you calculate on-time delivery ratios?
- Why is tracking on-time delivery performance important?
- How does on-time delivery relate to maintenance?
- Tips for improving on-time delivery metrics
- The Essential Guide to CMMS
- FAQ
- Related Content
Is Limble Mobile CMMS app user friendly?
Limble is consistently rated Easiest-to-Use CMMS on review sites like G2, Capterra, and Software Advice. And our customers agree. With our mobile CMMS app, teams experience 30%+ better productivity, on average, requiring little to no training or ramp-up time. Our CMMS app can travel with your team, no matter where they go! Visit our App Store or Google Play for more information.
Table of Contents
- What is on time delivery?
- OTD in Manufacturing
- Checklist for Creating a Preventive Maintenance Plan
- How do you calculate on-time delivery ratios?
- Why is tracking on-time delivery performance important?
- How does on-time delivery relate to maintenance?
- Tips for improving on-time delivery metrics
- The Essential Guide to CMMS
- FAQ
- Related Content
Can I connect to other systems?
Limble provides seamless, pre-built CMMS Integrations with the most widely used software systems. That means no help from a developer or your IT team is required. Learn more about our integrations.
Table of Contents
- What is on time delivery?
- OTD in Manufacturing
- Checklist for Creating a Preventive Maintenance Plan
- How do you calculate on-time delivery ratios?
- Why is tracking on-time delivery performance important?
- How does on-time delivery relate to maintenance?
- Tips for improving on-time delivery metrics
- The Essential Guide to CMMS
- FAQ
- Related Content
How secure is the Limble CMMS platform?
At Limble, our world-class data security practices ensure your account information is safe. We use state-of-the-art technologies and industry best practices to maintain a secure infrastructure, including SOC-II Type II certification, regular penetration testing, and continuous security training for our staff.
Table of Contents
- What is on time delivery?
- OTD in Manufacturing
- Checklist for Creating a Preventive Maintenance Plan
- How do you calculate on-time delivery ratios?
- Why is tracking on-time delivery performance important?
- How does on-time delivery relate to maintenance?
- Tips for improving on-time delivery metrics
- The Essential Guide to CMMS
- FAQ
- Related Content