Proactive Maintenance
Everything you ever needed to know about proactive maintenance.
What is proactive maintenance?
Proactive maintenance is a strategy that aims at identifying the root cause of machine issues before they become a more complex problem or an equipment failure. The goal of this type of maintenance approach is to reduce unplanned downtime, decrease the risks associated with operating unreliable assets, reduce maintenance costs, and extend equipment lifespans.
Different from the run-to-failure (RTF) maintenance approach, in which service is performed after an asset breaks down, proactive maintenance addresses potential problems in advance. RTF maintenance is not bad, but for most assets, it is not the most cost-effective approach. For most organizations, a balance between proactive and reactive maintenance should be considered.
Proactive maintenance programs can be implemented in small companies to large enterprises. Larger organizations tend to need more resources, such as modern CMMS or EAM software to organize the data and help with maintenance activities schedule.
Why is a proactive approach Important?
Degradation is a normal part of an asset’s lifecycle. Along with asset depreciation, comes some operational inefficiencies. Pieces of equipment operating in poor conditions use more energy than machines operating in proper conditions. Not to mention the risk of having machine failures when they are operating at a faulty performance.
A solid proactive maintenance strategy extends assets lifespan and ensures that they are constantly operating at their peak performance.
Checklist for Creating a Preventive Maintenance Plan
Following a consistent Preventive Maintenance Plan can make life easier. Use this checklist to create your own!
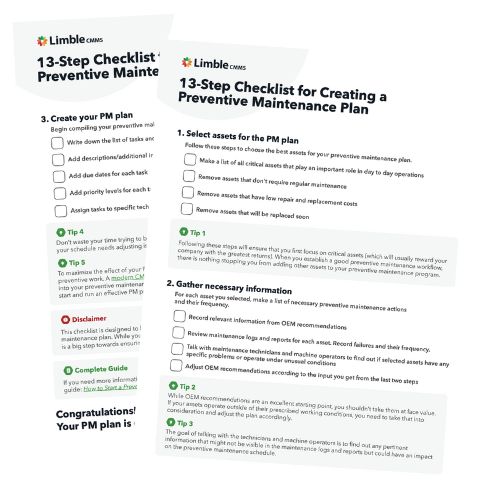
Types of proactive maintenance
Most proactive maintenance programs include a mix of time-based strategies and condition-based strategies. As the name implies, a time-based technique schedules regular maintenance activities over a pre-set period of time. A condition-based technique, on the other hand, organizes the maintenance schedule based on the equipment’s condition. Let’s look at both methods further:
Preventive maintenance
This time-based approach aims to keep assets at optimal operating conditions through frequent preventive services in every critical asset. Maintenance activities are scheduled from time-to-time even if the machine does not show any sign of wear-off. Depending on the equipment’s nature, technicians check on the machine every week, month, quarter, or year.
Also known as preventative maintenance, this approach is relatively cheap to be implemented. Maintenance managers usually create a checklist to be followed by maintenance technicians, who submit a maintenance report after the service. Most companies use a CMMS to streamline scheduling, assignment, and data tracking.
Predictive maintenance
The focus of this approach is to leverage condition monitoring technology to detect minor anomalies on the machines and with that, have the maintenance team take the necessary corrective actions before the machine breaks or needs more complex maintenance.
Because this approach relies on precise data and historical data, it makes it possible to schedule the exact amount of maintenance tasks that a piece of equipment needs — not too much or too little.
This maintenance technique has larger implementation costs when compared with preventative maintenance. That is because predictive maintenance (PdM) requires the implementation of sensors into the assets. These assets collect real-time data and send it to a CMMS database. CMMS software uses the Internet of Things (IoT) along with historical data to form predictive models. With that, maintenance managers are able to create an optimal condition-based maintenance schedule.
The functionality of the built-in sensors varies depending on the machine they are installed. Vibration analysis sensors, for example, are most often used on rotating machinery. They indicate when it is time for lubrication. Infrared analysis sensors, on the other hand, are used within pieces of equipment where the temperature is a good indicator of potential failure. There are also ultrasound analysis sensors, motor circuit analysis sensors, microphones, and others.
How to set up a proactive maintenance strategy
There are multiple ways to build a successful proactive maintenance strategy.
Although the outcomes are generally similar, the maintenance approach often changes based on the company size, goals, asset types, and maintenance team capabilities.
Let’s go over a few steps of the implementation process:
- Set Clear Goals
The first step in creating an effective maintenance program with a proactive nature is to set clear goals. Think about what your company wants to achieve or to avoid with maintenance management.
Some common goals are to:
- Increase assets’ useful life
- Increase risk management efficacy by decreasing dangerous reactive operations
- Predict failures before they occur to increase the financial return on machines
- Decrease the operational risk of crucial equipment to avoid costly downtime
- Prioritize Assets
Once your maintenance goals are outlined, the next step is to select which assets you will need to include in the maintenance program.
All of the company’s assets are important and play an important role. However, it is a good idea to categorize assets based on vitality.
- Machines can be prioritized based on the following queries:
- How crucial is the asset to the organization’s operations? Think about the impact of downtime.
- What is the financial impact of possible reactive maintenance on the asset? Think about the direct costs with maintenance if the machine breaks down.
- How difficult is it for maintenance technicians to access asset parts to verify conditions? If the access is hard, predictive maintenance can help assess conditions without having to shut the equipment down.
- Select the Type of Maintenance
This is where you decide whether you will invest in preventive maintenance, predictive maintenance, or a combination of both.
While predictive maintenance involves larger costs, it brings a larger ROI due to its preciseness. This makes it a great alternative for the most important assets. Preventive maintenance on the other hand is a great option for assets that can easily go through maintenance, without needing to shutdown.
- Choose an Efficient CMMS Software
A computerized maintenance management system (CMMS) is the platform that receives, integrates, and organizes assets data while also offering a complete dashboard with scheduling features.
Some modern CMMS solutions, such as Limble CMMS, offer both a predictive maintenance module and a preventive maintenance module, along with other maintenance solutions.
CMMS software can automatically send notifications to the designated team members when maintenance managers add a maintenance activity to the calendar. Managers also receive notifications when the PdM sensors detect any abnormality on the assets.
Limble CMMS software allows managers to program the system to automatically create work orders as the algorithm determines a potential failure.
This notification system streamlines communication and productivity as maintenance technicians receive the work order request automatically and can access the dataset through the mobile app to verify the details of the service needed.
Want to see Limble in action? Get started for free today!
Streamline maintenance with a proactive approach
If you want to promote successful operations, the first step is avoiding equipment failures.
Having your maintenance team constantly reacting to machine failure not only is an indication of organization dysfunction but also can affect the organization’s bottom line. Reactive maintenance can also represent a safety risk to the team.
Maintenance departments can improve equipment reliability, reduce unplanned downtime, and keep costs low by implementing proactive maintenance plans that fix small problems before they become big ones.
If you are interested in learning more about the best way to approach proactive maintenance, book a demo with one of our team members. We would love to hear more about your company’s needs, goals, and help you outline the best solution.