Maintenance was a fairly straightforward concept in the early days of industrial production. Machines tended to be big, extremely rugged, and simply designed. Production demand was far more relaxed and downtime was not as critical.
But these days, industrial maintenance is facing drastically different circumstances. Machines are far more sophisticated, with many moving parts that are prone to frequent breakdowns.
The solution? Proactive maintenance.
In this article, we explore the modern tools and technologies that facilitate proactive maintenance strategies that both predict and prevent breakdowns.
What is proactive maintenance?
The first thing to note about proactive maintenance is that it is not a specific strategy. Rather, it is more of an umbrella term under which a diverse mix of maintenance strategies has evolved over time.
The traditional approach to maintenance, for many years, was reactive. Reactive maintenance accepts equipment failure as inevitable. Repairs are carried out when a machine stops functioning properly. Downtime is almost certain – the focus is on trying to get the production/operation restarted as soon as possible through emergency repairs.
Proactive maintenance is the polar opposite of such an approach. Every proactive maintenance strategy focuses on avoiding machine failure and downtimes as much as possible. Instead of treating the symptoms, they try to identify the underlying causes of the malfunctions/breakdowns – and fix or prevent them in advance.
Options for proactive maintenance management
This list of proactive maintenance strategies is set up to go from the cheapest and simplest to implement, to more advanced and complex approaches:
- Preventive maintenance (PM) is the most popular proactive maintenance strategy. Maintenance work is performed at regular intervals. The intervals are either calendar-based or usage-based.
- Condition-based maintenance (CBM) is a maintenance methodology where the condition of the asset is monitored through condition monitoring technology. Maintenance work is performed when sensors (or tests performed with handheld equipment) show that the asset is experiencing an issue.
- Predictive maintenance (PdM) uses a combination of condition monitoring sensors and machine learning to forecast when a machine is likely to fail. It works like an early warning system that gives maintenance personnel alerts, notifications, and enough time to plan and schedule repair/servicing before failure occurs.
- Prescriptive maintenance goes one step beyond PdM. With prescriptive maintenance, the machines use sensors and analytics to perform self-diagnosis and present technicians with a few solutions on how to deal with the identified issue(s).
On top of each of those strategies, companies that strive to create a leaner maintenance department can implement concepts like autonomous maintenance and total productive maintenance (TPM).
Addressing root causes of equipment failures
You can’t address issues you do not know exist. Proactive maintenance focuses on identifying the root causes of equipment failure and breakdowns on the production floor. In a modern industrial setting, many potential causes can come up.
Here is a quick list of the most common culprits:
- Use of poor-quality spares and substandard supplies in maintenance.
- Misuse of equipment, or operator errors – often due to poor training.
- Lack of strict adherence to essential maintenance schedules.
- Mistakes by maintenance teams – also due to a lack of training.
- Over-extension of equipment for peak production.
- Assets reaching the end of their useful life.
Many of these causes have straightforward, cost-effective solutions. Proper training, use of high-quality spares, not skipping maintenance schedules, and replacing equipment at the right time can help reduce the incidence of equipment failure considerably.
Proactive maintenance is beneficial here, as it prompts the organization to seek out these root causes, instead of merely performing repairs to paper over the cracks.
Advantages and disadvantages of proactive maintenance
Shifting to proactive maintenance can bring the following key advantages to an organization:
- Reduced downtime due to fewer instances of malfunctions and breakdowns.
- Improved equipment reliability, availability, and uptime.
- Reduced long-term maintenance costs – both in repair costs and labor costs.
- Fewer productivity and safety issues.
- Increased longevity of equipment, resulting in further savings.
In the long term, proactive maintenance can result in significant advantages to a business, with increased productivity, savings, and reduced maintenance costs.
The main downside of proactive maintenance strategies is that it does take some planning, effort, and investment to implement them. Different proactive maintenance strategies have vastly different implementation requirements.
Guide to Moving from Reactive to Preventive Maintenance
Want to transition away from costly reactive maintenance but don't know where to start? This guide has everything you need to know.
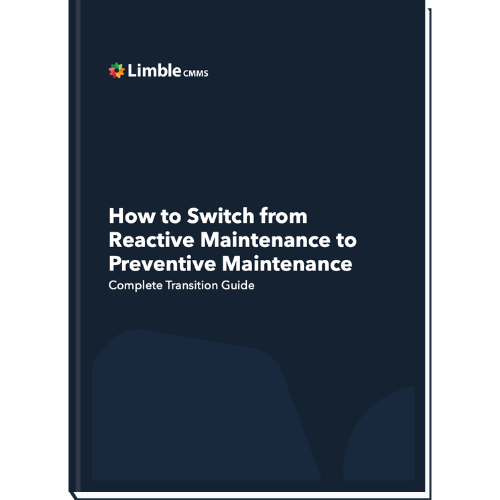
Basic requirements for implementing proactive maintenance
The biggest challenges of proactive maintenance come in the early stages of adoption. The shift from traditional reactive maintenance to a proactive approach can be challenging. Especially if maintenance techs are resistant to change.
The following factors are essential to the success of a proactive maintenance strategy in any organization:
Commitment from top-level management
Switch to a proactive approach will eat into your maintenance budget. Employee retraining, recruiting new staff for analysis, CMMS software, condition monitoring equipment – none of these things are free.
If the budget is really tight, preventive maintenance, as the cheapest and simplest proactive maintenance strategy, is a great place to start.
Without the total commitment from top-level business leadership, any attempt to shift to proactive maintenance will fail. The leadership needs to be fully on board for the plan to succeed. Since it involves profound changes across the organization, the pressure to implement a proactive maintenance plan has to come from the top.
A proactive maintenance culture
A shift from reactive to proactive maintenance requires fundamental changes in the maintenance culture of the organization. People tend to be quite resistant to change – be it in terms of adopting new technologies, operational parameters, or workplace culture/mindset.
A shift to a new maintenance culture can be a major hurdle, especially if your maintenance teams do not see the purpose and benefits of the changes you are making. For successful implementation, it is imperative to get all the stakeholders on board.
Understanding current capabilities of the maintenance department
Before making a transition to proactive maintenance, it is important to understand the current capabilities of the maintenance department. An in-depth analysis of existing maintenance processes, technologies, and skill levels is needed for optimal planning.
Having access to the right kinds of performance data and maintenance metrics can make a world of difference for running proactive strategies. Only firms that already have a computerized maintenance management system (CMMS) have access to such data, which brings us to the next key ingredient.
Cloud-based CMMS solution
Proactive maintenance strategies rely on tracking and analyzing a ton of data. This is only possible if the organization conducts maintenance operations using CMMS software. With the software, firms can easily track maintenance schedules, asset failure patterns, service history, and other key performance indicators. It helps firms organize, automate, and streamline maintenance work.
Basic proactive strategies like preventive maintenance and predictive maintenance rely on the insights delivered by a CMMS. If an organization does not already use CMMS, it should be the priority when a shift to proactive maintenance is being considered.
Core steps for setting up an effective proactive maintenance program
Once you have the basic requirements in place, it is time to get started with proactive maintenance. It requires careful planning and a measured approach. The following are the core steps for an effective proactive maintenance program:
1. Pick a project leader
For a project of this magnitude and complexity, you need someone who has an intimate knowledge of maintenance in your organization. Ideally, it should be a senior supervisor, maintenance manager, or planner/inventory manager. It is the role of the project leader to oversee all planning and implementation aspects of a proactive maintenance schedule.
2. Create a comprehensive asset registry
Proactive maintenance will cover all the important assets owned by an organization. So creating an asset registry is important – it will make the planning process much easier, giving quick access to the service records and other metrics.
Usually, a CMMS will help maintain a fully up-to-date asset registry and help with your asset inventory management efforts.
3. Consult all stakeholders
You need inputs from all your frontline maintenance technicians who perform routine maintenance of the assets. They, along with others who work on these assets – operators, engineers, safety managers, OEM vendors – can give you critical insights into the performance and maintenance aspects of the assets.
The success of a proactive maintenance schedule hinges on creating practical and efficient maintenance schedules that address the right failure modes.
4. Identify the critical assets based on inputs
Usually, organizations will have a handful of critical assets that play a huge role on the production floor. Most of these assets can be quickly identified – it is common knowledge across the organization.
Larger facilities with dozens or hundreds of assets can perform risk-based maintenance (RbM) analysis to find the most critical assets that should get the most attention.
5. Find the ideal proactive maintenance strategy for each critical asset
Once you have the list of your assets and their criticality, you have to create an individual maintenance schedule for each asset. This can be a complex endeavor where a CMMS database makes a huge difference.
If you do not have access to much data because of lost documents and/or poor record-keeping practices, you will have to rely on equipment manuals and inputs from experienced maintenance staff.
In large organizations with many expensive assets, running reliability-centered maintenance analysis is never a bad idea. It helps identify the most common failure modes and select the right prevention methods.
6. Invest in the right tools and technologies
Different maintenance strategies require different levels of access to modern tech:
- Preventive maintenance can be run with just a CMMS software
- Condition-based maintenance also needs sensors and other condition monitoring tools (which are sometimes classified under IIoT tech)
- Predictive maintenance needs all of that plus someone to develop and maintain predictive algorithms
- The same goes for prescriptive maintenance, it is just that their algorithms are even more complex
Long story short, if you want to run advanced maintenance strategies, you may have to invest in industrial sensors and IoT connective capabilities, or even custom-made technology for maintaining your assets.
7. Create detailed documentation for selected maintenance processes
As any other, maintenance teams should strive for continuous improvement. Whenever new strategies are pursued, it is essential to create standard operating procedures (SOPs) and maintain exhaustive records of all planned maintenance processes and work orders. Creating detailed, step-by-step instructions ensures that the teams carry out maintenance up to required standards – with a little bit of (re)training.
Again, CMMS will help execute and coordinate everything, while leaving room for appropriate improvements and tweaks when necessary.
8. Implement a proactive maintenance schedule
Once all the factors are in place, it is time to start the proactive maintenance schedule. Ideally, a schedule should have maintenance tasks mapped out for at least a year – looking at a fully annual maintenance cycle, taking into account the various peaks and troughs in production demands, as well as planned shutdowns.
But this cycle may be longer or shorter, depending on your organization.
The actual implementation of a proactive maintenance program will take some time, ranging from a few days to several months, depending on the size and scale of your facility.
Proactivity reduces unpredictability
Business thrives on stability and predictability. Frequent asset failures and unexpected downtime lead to increased operating costs and productivity issues. Proactive maintenance can help you get out of a vicious cycle of constant repairs and breakdowns. The long-term benefits of such an approach are self-evident.
Yes, the upfront costs can be significant in terms of time, training, and technological investments. But the systems will pay for themselves several times over in short order, with cost savings and improved productivity.
Having a CMMS system in place can be critical in the early stage, making the transition to proactive maintenance smooth and painless.
Contact us to learn more about Limble CMMS and how you can use it to support your proactive maintenance efforts.