Protect and support your students and faculty
Limble’s versatile, collaborative CMMS minimizes maintenance emergencies and unplanned work, creating a safe and reliable learning environment for everyone.
Preventive maintenance
Expertly manage PMs to avoid unplanned downtime that impacts patients and providers.
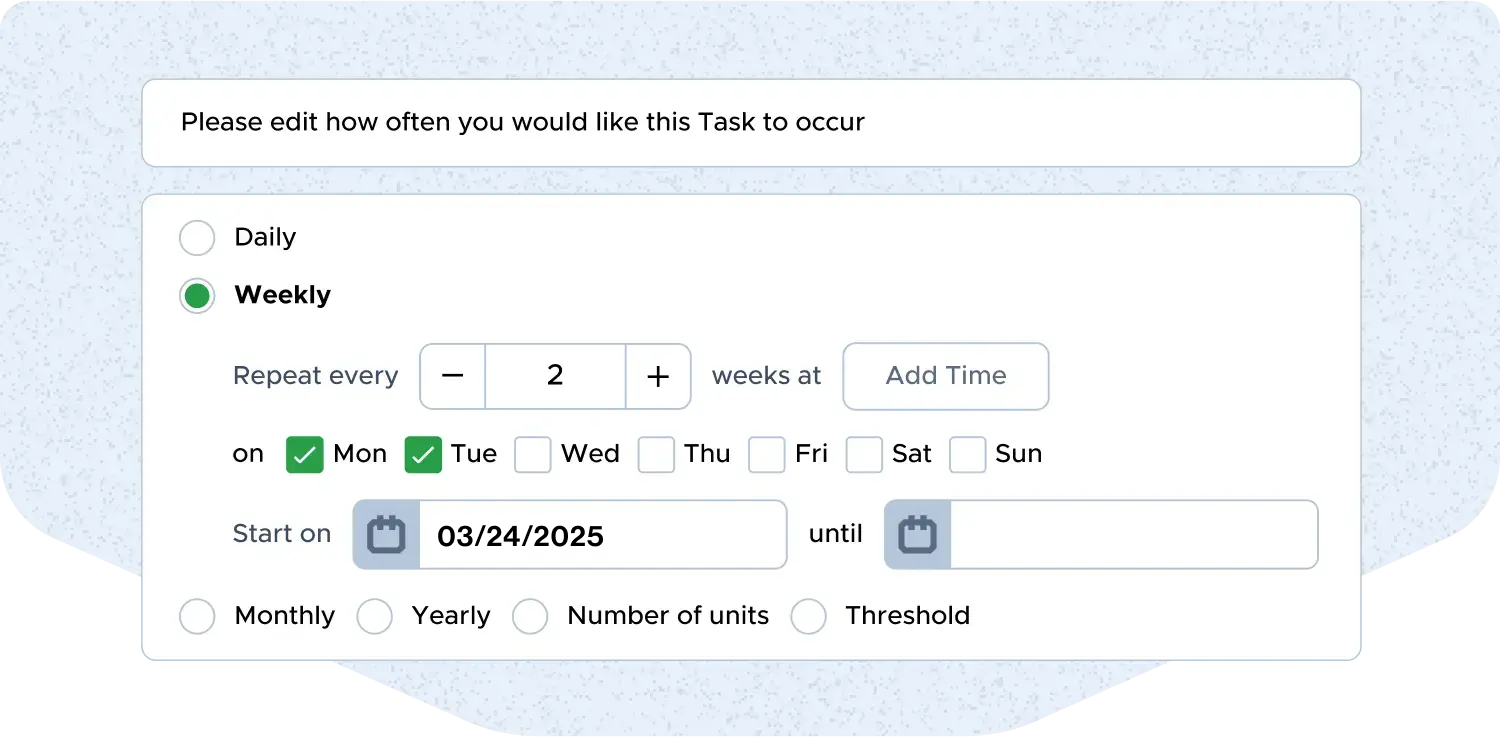
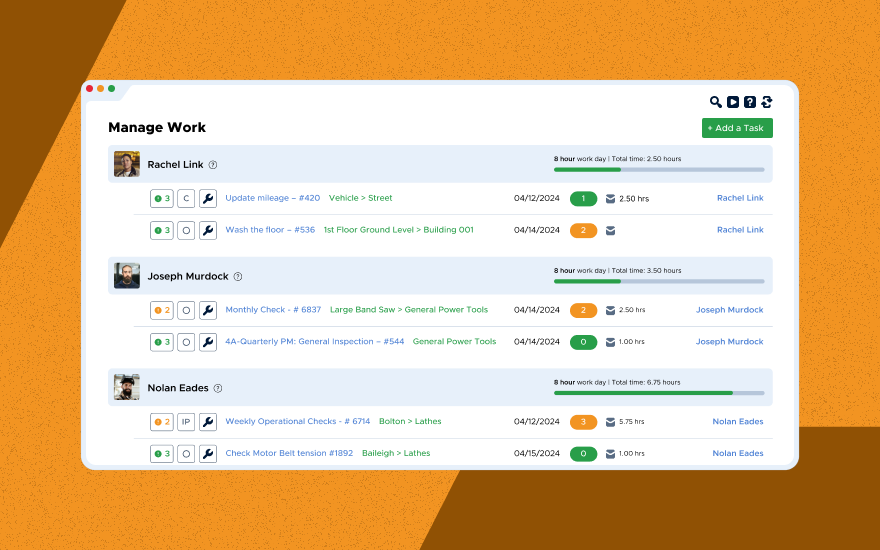
Empower campus staff to submit work requests
Let any employee submit a work request without having to log in. Just share a link to your Limble work request portal and new tasks will automatically be assigned to the appropriate maintenance team member.
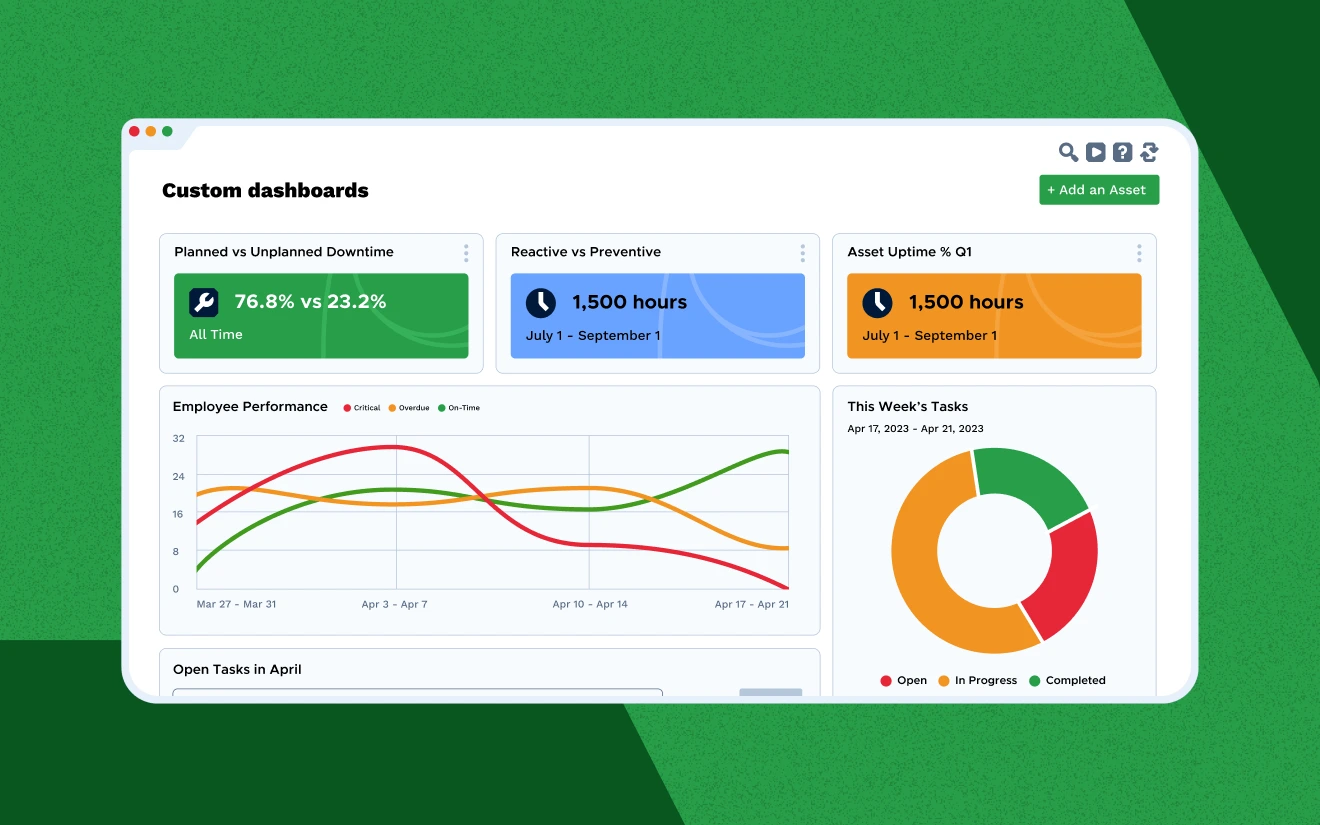
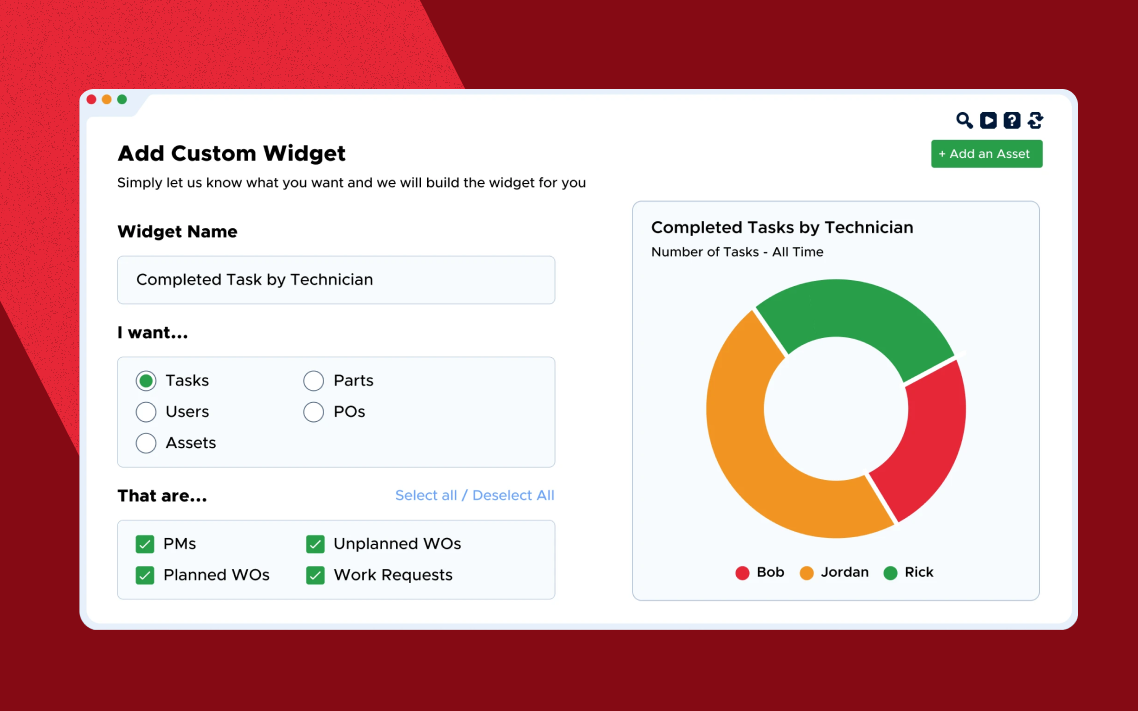
Seamless maintenance management for multi-campus schools
Limble provides the ultimate flexibility and scale for large, multi-property campuses and school districts. Track work orders and PMs across many facilities, assets, and parts and configure Limble templates and workflows to fit your needs.
Hear it from our customers
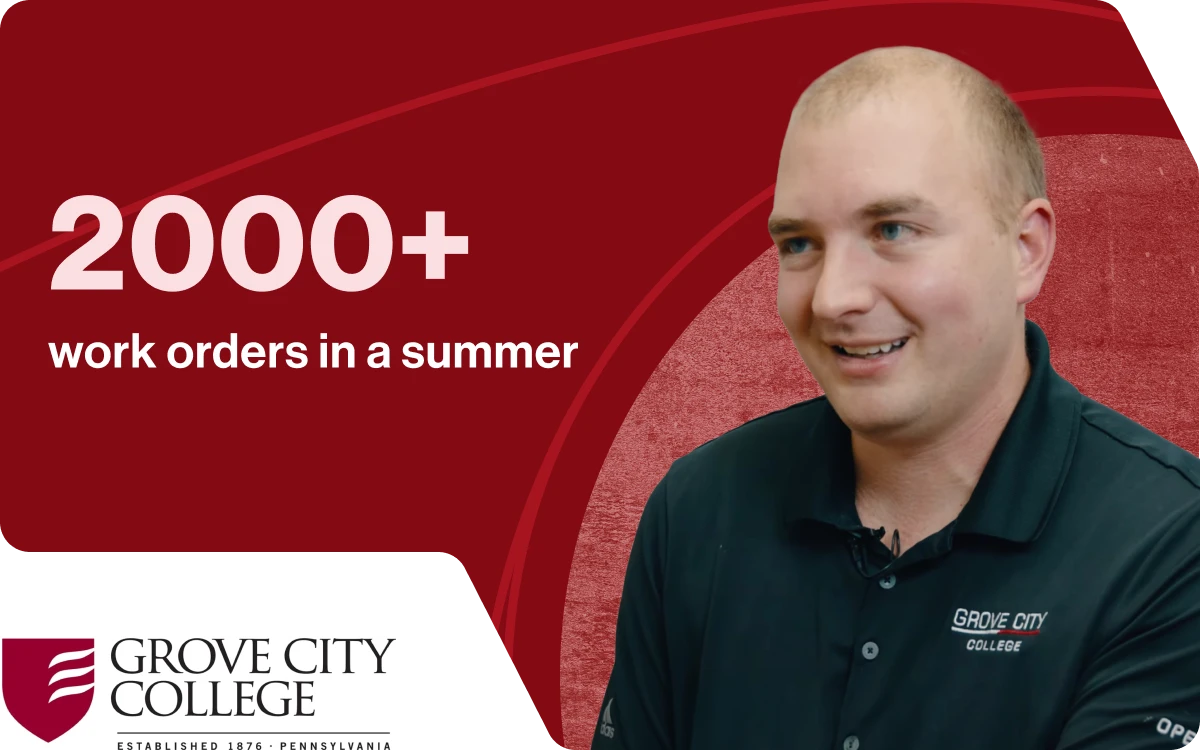
Migrating to Limble
Grove City College took its maintenance program from chaos to clarity when it upgraded an out-of-date CMMS.
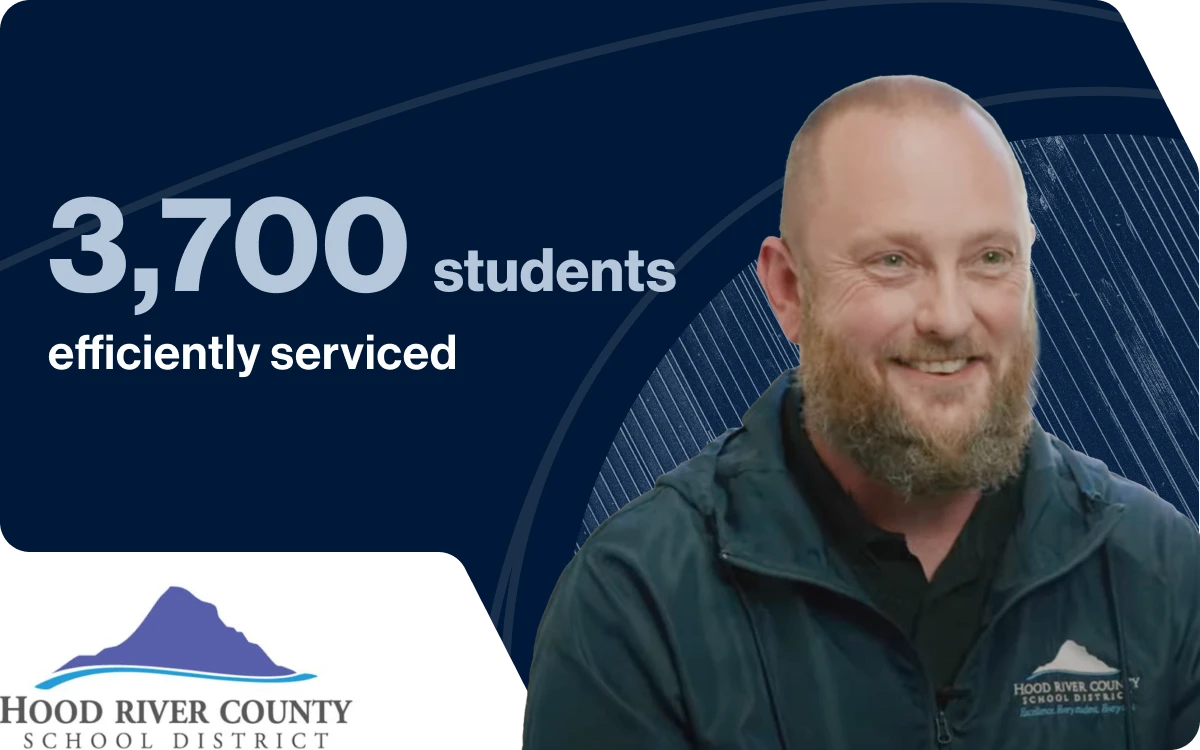
Improving efficiency metrics
Hood River County School District increased efficiency, job satisfaction, and money saved in the first year.
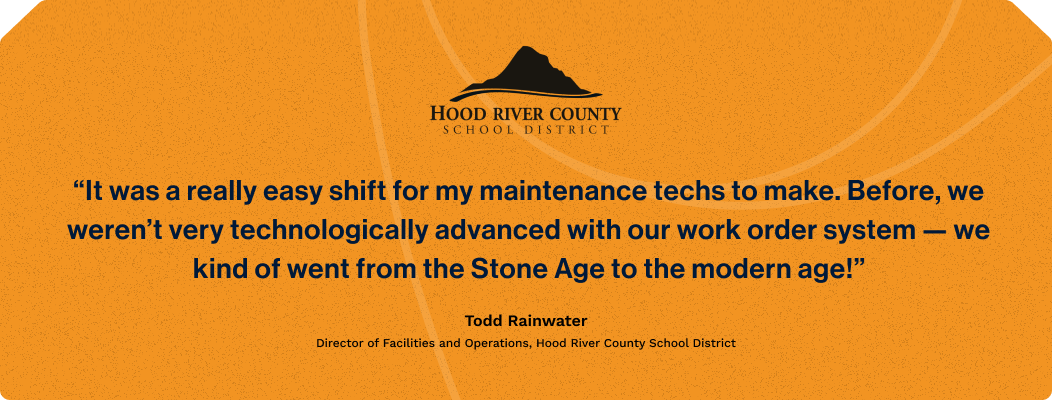
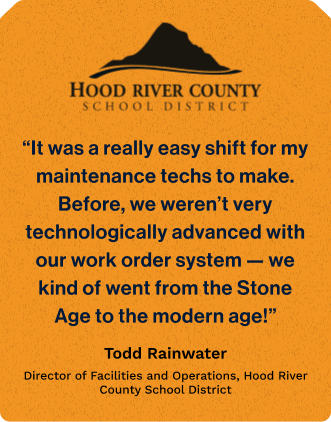