Business theory suggests that a manufacturer’s production and maintenance departments are united in a common goal. Unfortunately, as the famous Marvel villain Thanos likes to point out: reality is often disappointing. Rather than being linked through interdependence, you find obstructive rivalry, finger-pointing, and counterproductive behaviors.
Such a culture sabotages your business, costs money, and reduces competitiveness. Let’s see how to improve the relationship between maintenance and production teams.
The Essential Guide to CMMS
Download this helpful guide to everything a CMMS has to offer.
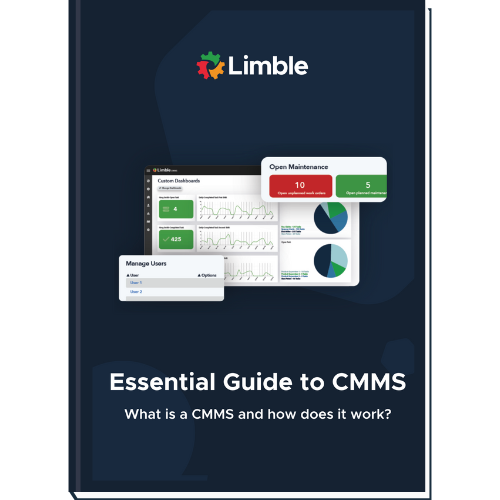
Six tips for uniting your production and maintenance departments
The following tips help you audit your business. When you spot signs of dysfunction, use the outlined suggestions as a guide to effective solutions.
Tip #1: Realign departmental incentives
Problem
Competitiveness or obstructive behavior is rarely driven by malicious intent but rather a desire to protect personal gain. When incentive structures for two departments reward opposing outcomes, you have pitted two departments against each other.
Solutions
A good example is a refinery connecting a new process facility to an operating plant. There are two parties, the external contractors and personnel from the refinery. The team from the refinery is allocated to assist the contractors with the connections. They are to liaise with their colleagues for refinery shutdowns, allowing the contractors to make the necessary connections.
However, the promised planned shutdowns repeatedly fail to occur, being canceled at the last minute. With team relationships breaking down, an audit reveals that the refinery team is still incentivized for tons of production. The contractor’s incentives depend on connections achieved and the deadlines for completion. Aligning both teams’ incentives to reward connections and deadlines would remove that friction.
Check the incentives you’re applying to your production and maintenance teams. You are driving opposing behaviors if you’re rewarding actions that conflict, such as measuring units manufactured for operators and planned maintenance tasks for maintenance. Centralizing incentives around overall equipment effectiveness (OEE) aligns both parties behind a metric that adds business value.
Tip #2: Remove destructive rivalry
Problem
Some managers feel rivalry is a good thing, and it can be in small, benign cases. However, it’s more often destructive and signals poor supervision and weak management. You need alignment between your teams, with each team supporting the other, not tearing each other down.
Solutions
Lean manufacturing emphasizes a Gemba walk. A Gemba walk is when managers get out of the office and walk the floor with their ears and eyes open, talking to teams and watching operations. Not as a manager exerting power, but as someone willing to listen and learn.
Check for signs, symbols, and language that may indicate unhealthy rivalry or a lack of respect between teams. How do operators refer to maintenance personnel? Do they use us-and-them language? Is there obvious segregation between the two teams? What formal or informal notices do you see on notice boards or in lunchrooms? When breakdowns occur, how are they described to you?
If rivalry exists, your managers and supervisors are failing you. You don’t pay them to support dysfunctional behavior, you pay them to address it. Poor supervision supports and reinforces behaviors that lead to becoming partisan, feeling their job is to defend their teams. It’s not.
The role of a supervisor or manager is to model team behaviors. Pejorative discussions regarding the other team should be stopped, just like with any other actions that are counter-productive to business success.
If issues need to be addressed, the managers can talk privately to reach a compromise. Set clear expectations for your supervisory staff and reward them for correct behaviors.
Tip #3: Plan shutdown schedules together
Problem
If shutdown schedules are ‘owned’ by one department, any actions by another team to delay or change that schedule will be met with fierce resistance. You often find each department runs its shutdown schedule independently of others. What a waste of opportunity!
Solutions
Planning a line or factory stoppage must form one consolidated shutdown. Every department that wishes to perform specific tasks (like routine maintenance) within that period must be an equal partner in the planning of that shutdown.
Senior managers must convey the need for flexibility and mutual support to shutdown participants. When one party strikes problems and delays, the others should rally around and support them, not throw rocks and point fingers.
Tip #4: Include operators in basic maintenance and servicing tasks
Problem
Dysfunctional operations involve rigid silos. When something goes wrong, people from one silo step back and wait impatiently for someone from another unit to turn up and ‘do their job’. The ‘it’s-not-my-job’ attitude has no place in a modern business and is a sign of serious cultural problems.
Equipment operators must know, own, and care for their equipment. A simple example is a company van. If others are responsible for cleaning it, people using the van are more likely to treat it with disrespect, dropping rubbish and leaving it dirty. Yet, when the driver is responsible for the daily cleaning, they treat the van with more respect.
Solution
Daily involvement in basic inspection, care, and light maintenance tasks assists operators in identifying with both the equipment and the maintainers. Greater operator involvement means greater insight into working methods and improved understanding when something doesn’t seem right. Trending faults are identified early, while lubrication or inspection tasks are removed from the maintenance technicians’ schedules, freeing them for more value-adding tasks.
Conversely, maintainers must treat operator concerns seriously, investigating and reporting on their findings. Operators spend long hours with the equipment, and if they feel something is not right, maintainers must acknowledge that intuition. Instead of feeling threatened by greater operator involvement, maintainers should welcome the opportunity to pass on knowledge, empowering operators to assist with optimum equipment maintenance.
Putting this into practice basically means implementing autonomous maintenance.
Tip #5: Ensure a free flow of information regarding production plans
Problem
The belief that production plans are the sole domain of production and excluding all departments supporting and enabling optimum operation drives an us-and-them mentality. Every department exists to support production goals. They are not subservient to the production process in client/supplier relationships but equal partners in making the business successful.
Many businesses communicate the production plan once a week at a meeting. Yet, production plans change regularly and should be updated.
Solution
Maintain an immediate and ongoing dialogue with the maintenance department when changes occur in the production plan. While maintenance may choose not to use every opportunity, these updates make them an equal partner.
Such changes might allow maintenance tasks to be completed in a less disruptive manner, reducing the volume of work on imminent shuts and allowing production to resume earlier than planned.
Maintenance planners can use a CMMS system to organize maintenance work, as well as have the ability to quickly reschedule maintenance assignments when the production team notifies them about an open time slot.
Tip #6: Train operators on equipment priorities and redundancies
Problem
Every equipment failure or malfunction is often considered a priority by operators. Urgent work requests are sent to maintenance, demanding an immediate rectification of the problem.
Operators should be aware that their maintenance colleagues have to continuously balance conflicting priorities, and incorrect work prioritization requests impede optimal asset maintenance. You do not want to pull technicians from longer running but critical maintenance operations to attend maintenance tickets of lower criticality.
Such actions reduce maintenance effectiveness while adding costs through unnecessary callouts and after-hours work. It leads to unproductive friction and resentment between production and maintenance teams. If every task is always urgent, it devalues the point of prioritization.
Solution
Training is paramount. Maintenance and operating personnel must come together to identify equipment redundancies and prioritize operating states.
In aviation, aircrafts have what’s known as a minimum equipment list. It identifies equipment that must be fully or partially operational for the aircraft to continue operation. Failure of a non-essential part may drive changes in operation but doesn’t stop the aircraft from flying, allowing rectification by maintenance personnel within a prescribed time frame. Failure of a critical item immediately grounds the aircraft until maintenance has resolved the issue.
Help operators understand when equipment can continue operating, either through amended operating procedures or switching to backup equipment. Such knowledge should help operators to appropriately prioritize work requests.
Correct use of prioritization reduces unnecessary callouts and uses maintenance budgets more effectively, creating a more supportive relationship between maintenance and production.
Unite maintenance and production towards a common goal
Creating hierarchies of importance or silos between production and maintenance is wasteful, costly, and counter-productive to good business management. There is a reason why lean manufacturing emphasizes each employee’s role in optimizing business performance by eliminating waste.
By breaking down barriers and poor attitudes between the maintenance and production departments, you create a culture of synergy and partnership that adds real value to your business through improved OEE and reduced operational costs.
Lastly, do not forget that there are digital tools out there like CMMS and MES systems that improve accountability and ensure both teams have access to relevant information as soon as possible.