Equipment failure is a common phenomenon in the industrial setting. It can result in higher repair costs, production downtime, health and safety implications for workers, and affect production and delivery of services. The International Society of Automation indicates that factories lose anywhere from 5% to 20% of their productivity due to downtime – equivalent to thousands and even millions of dollars in some cases.
Implementing a defense against failure and ensuing downtime requires a thorough understanding of machine failures and their mechanisms. This includes analyzing failure causes and their consequences, so we can devise appropriate mitigation strategies.
A quick definition of equipment failure
Simply put, equipment failure is the condition in which a piece of equipment does not operate as intended. Based on the severity of the problem and functionality of the equipment, we can differentiate between two broad categories:
- Complete failure
- Partial failure
Any event that leads to a complete loss of value from equipment is a complete failure and an event that leads to a partial loss of value represents a partial failure.
Complete failure is easy to recognize, as it makes the asset practically unusable. Common examples of complete equipment failure include vessel, pipe, or valve ruptures, engine breakdowns, breakdown of a propeller in a turbine, severe boiler or HVAC malfunctions, bearing failure, etc.
There may be some conditions when the equipment functionally operates, but can only partially meet its intended performance. This is a sign of a partial failure. For example, due to motor speed control malfunction, the conveyor belt operates at a slower speed, leading to the failure of plant synchronization.
Other examples of partial failure include problems like wear and tear, corrosion, dirty air filters, lack of proper lubrication, and similar occurrences. In many cases, it is enough to perform corrective maintenance to return the machine to optimal working condition.
Failures come in various degrees and you can’t catch them all. However, with the right tools and a proactive approach to maintenance, most can be prevented and addressed before they lead to serious issues and cause expensive downtime.
Common causes of machine failure and preventative measures
There is no one-size-fits-all strategy to prevent equipment failures. The failure prevention strategy should be designed differently for different pieces of equipment, operating within their context and definition of its expected value.
There are various maintenance strategies available to prevent machine failures, such as preventive maintenance, condition-based maintenance, and predictive maintenance. Choosing the right one depends on many factors and is often a trade-off between the required investment and reaching reliability, availability, maintainability, and safety (RAMS) objectives.
There are various reasons behind equipment breakdowns, which can seem unpredictable at times. Several reasons can cause the machine to fail or underperform. The following are some of the most frequent causes of machine failure and tips on how to prevent them from happening.
1) Regular wear and tear
It is the most common cause and happens in all types of equipment. Repeated use of machinery, even when following the best practices, will eventually lead to wear and tear (also known as ‘metal fatigue’). Several reasons can speed up machinery failure, such as bad operating conditions, lack of routine maintenance, improper usage, and poor storage conditions. When left unaddressed, the damage that happens due to wear and tear can be catastrophic.
How to prevent it
One of the common ideas of preventing wear and tear in rotary machines is lubrication. Regular lubrication of the machine parts reduces friction within moving elements and controls unnecessary wear and tears within the machines. For other types of equipment, periodic inspections and preventive/predictive maintenance of the machine parts, including replacements of belts, hoses, bearings, filters, cleaning up dust and dirt, and being mindful of contaminants, can also further reduce the probability of machine failure caused by wear and tear.
2) Lack of routine and preventive maintenance
Due to limited budgets, many organizations are still using breakdown maintenance. While this approach works for some equipment, they are not well suited for complex and critical equipment. Lack of routine and preventive maintenance leads to huge deferred maintenance backlogs – and all operational issues and costs that come with that.
Time-based preventative maintenance is not a perfect solution either. Depending upon the failure mechanism, the equipment tends to fail more often as it approaches its end of useful life. Since most of the equipment is maintained at fixed regular intervals throughout its lifespan, it often tends to be under-maintained at later stages of its asset lifecycle.
How to prevent it
As you can imagine, implementing a proactive maintenance strategy is a solution to this problem. The easiest way to do that is to use a CMMS, as it will help you manage all of the resources that need to be managed with a proactive strategy – assets, work orders, calendars, schedules, vendors, and inventory.
It is much easier to lead an organized maintenance team when you have all of the required information in one place.
Checklist for Creating a Preventive Maintenance Plan
Following a consistent Preventive Maintenance Plan can make life easier. Use this checklist to create your own!
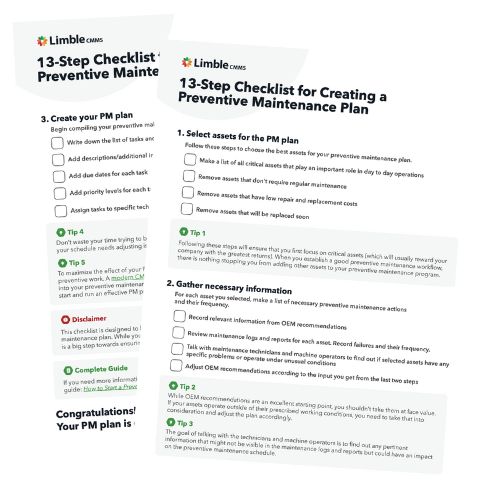
3) Improper use and operator errors
Operator/human error is defined as the cause of unexpected consequences due to distraction, bad decisions, deviation from the actual process (doing extra tasks or not following the task sequence). It can cause various problems that range from operational downtime to severe safety incidents.
How to prevent it
Machine operator training is one of the most effective tools to avoid improper use or mishandling. Most industries will define a minimum level of necessary training for different assets. They might also look to issue training certificates to maintain the desired level of competency for operating specific machines.
While it happens less often, a piece of equipment can also be damaged during the maintenance process. Many organizations create operation and maintenance manuals, SOPs, and maintenance checklists so that anyone who interacts with the equipment knows exactly what to do.
4) Poor reliability culture
In some organizations, the management may have a distorted definition of plant reliability. They may see any plant, where a piece of equipment is immediately fixed upon failure, as reliable. While a quick fix may improve the plant availability and MTTR – it is not a good reflection of plant reliability.
Moreover, due to budget limitations, some businesses hesitate to invest in improving reliability culture, not seeing the immediate benefits it has on asset management. This is because reliability improvement is a long-term benefit, so it can take a while to see significant ROI. Since many small and medium-sized organizations also lack long-term planning habits, they fail to understand the true benefit of incorporating a reliability-driven culture.
How to address it
There are many efficient and cost-effective reliability improvement solutions available on the market. One of the effective solutions is a modern, mobile CMMS. It offers a substantial improvement for manufacturing businesses and helps them embrace a transformation in their reliability culture. Organizations that are hard stuck in the reactive mindset will have to put more effort into change management in order to get their organization on the right track.
Departments that are seriously interested in improving their reliability efforts should look into techniques like RCM, RCA, and FMEA. They can help them assess common failure modes for specific assets, and decide which maintenance strategy should be applied to each asset.
Manage and prevent equipment failures with a modern CMMS
CMMS software can be easily deployed to simplify, automate, and organize preventive and predictive maintenance tasks. After all, its main purpose is to help organizations be proactive.
Here is a list of ways in which CMMS can help manage and prevent machine failures:
- It helps managers and supervisors to develop routine maintenance schedules
- It features a maintenance calendar for easier tracking and managing of incoming tasks
- It keeps technicians accountable for performed maintenance work
- It helps you monitor and plan spare parts inventory
- It can serve as a centralized repository for maintenance history, SOPs, checklists, safety procedures, and other guidelines for asset management
- It can integrate with condition-monitoring technology, to automatically trigger work orders based on real-time data
- In the worst-case scenario, it can help you optimize and coordinate emergency maintenance and other types of reactive work, based on its priority
This is by no means an exhaustive list of what CMMS can do, only the things that are closely tied to preventative equipment maintenance.
Key takeaway
Even without reading this article, most maintenance professionals are aware that the lack of preventive maintenance is the source of most of their headaches. While we do not like to tut our own horn, the solution is obvious – implement a CMMS and use it as a foundation for developing a preventive maintenance plan.
Even if the budget is tight, modern maintenance software is not particularly expensive and provides a good ROI that won’t impact your bottom line significantly. For more info about Limble CMMS pricing or starting a trial, click here.