Work orders (WO) are more than just documents. They serve as the foundation of effective maintenance strategies. A WO guides your maintenance team through their tasks to ensure equipment and facilities remain productive, safe, and efficient.
What to include in a work order
A WO should include all the details necessary for completing a task, including:
- Clear, step-by-step instructions
- Equipment diagrams and manuals
- A priority level for the task
- Location details
- A list of any tools or equipment the maintenance technician will need
- A list of any special skills required
- Details on the authorizing party
- Details on the technicians assigned to the task
- Details on safety procedures for the task
- The creation date and submission date for the work order
- An expected completion date or due date based on data
- An estimate of the hours necessary to complete the task
- Checklists to confirm successful completion
Work orders may also include a troubleshooting guide for common issues and space for technicians to leave complete notes.
Different types of work orders
Maintenance programs use various types of work order forms. Depending on their size and industry, certain organizations may be especially likely to use work orders from certain types of categories especially often.
Corrective maintenance work orders
These documents describe reactive maintenance tasks. The corrective workflow begins after a technician notices a problem while conducting an inspection, executing another type of work order, or carrying out daily operations. A typical work order involves repairing or replacing malfunctioning components to avoid more serious trouble.
Emergency maintenance work orders
Emergency work orders deal with high-priority creative tasks. Maintenance departments issue these when critical assets break down and the organization experiences significant production delays or safety issues.
Preventive maintenance work orders
Preventive (or preventative) maintenance work orders help to plan and schedule maintenance work ahead of time. By preemptively servicing their critical assets, organizations can ensure equipment stays reliable and avoid costly breakdowns.
Inspection work orders
Another type of preventive work order, these WOs dispatch technicians to audit and inspect equipment as part of routine maintenance operations. The goal is to spot potential maintenance issues early and follow up with corrective action before a serious breakdown occurs.
Safety work orders
These emergency maintenance work orders specifically aim to keep people and facilities safe from hazards. Depending on the type of facilities and assets you manage, workplace hazards might include spills, fires, or dangerous fumes.
Electrical work orders
Facilities management and maintenance teams fill out these work orders to assign resources for tasks related to electrical systems.
General work orders
These WOs cover maintenance and asset management tasks that don’t fall into the above categories. For instance, you might complete a general work order to instruct a team member on decommissioning an asset.
The work order lifecycle
Whatever their category, work orders typically follow a prescribed workflow. Here’s what the work order management process usually looks like from beginning to end.
- Identifying a task: The work order lifecycle begins when someone recognizes a maintenance issue that technicians can help to address. In some cases, the task is recognized proactively and kickstarts a preventive maintenance work order process. These may become part of routine maintenance schedules for specific pieces of equipment. Alternatively, your team members may discover an imminent breakdown or another type of emergency and trigger a corrective or emergency work order. These too may lead you to introduce new routine work requests to keep equipment running.
- Submitting a work order request: Work orders begin life as different types of documents: maintenance work requests. These provide an initial notification to your maintenance team, while work orders provide the necessary information to carry through on requests. Maintenance requests include the preliminary details that eventually contribute to comprehensive work orders.
- Evaluating the maintenance request and creating a work order: Next, the relevant maintenance manager reviews the request. If approved, they’ll build out a work order before planning and scheduling it based on priority. They’ll determine priority based on factors including the likelihood and potential cost of downtime and the asset’s criticality.
- Assigning and distributing the work order: After prioritizing and scheduling the work order, you’ll assign it to a qualified technician. Make sure the work order includes all the necessary information listed above.
- Completing and tracking the work order: Then, the technician completes the work order. Their responsibilities may be simple or involve a complicated, multi-part process. Once they’ve finished their work, the technician submits the complete work order and completes any follow-up activities. Tracking work order completion over time will make it simpler to proactively identify potential bottlenecks and intervene to support struggling maintenance technicians. If you look at metrics like Mean Time to Repair and schedule compliance, you can set KPIs and work toward building a more innovative and efficient maintenance department.
Work order management best practices
Whatever the size, structure, and capabilities of your maintenance team, these best practices for managing work orders can help promote efficiency and streamline your maintenance staff’s daily work.
- Standardize your process: Establish clear standard operating procedures with input from relevant stakeholders to promote consistency and efficiency. Requesting, creating, distributing, closing, and reviewing new work orders should look the same every time – regardless of the task in question.
- Define success and set appropriate goals: Begin by conducting an assessment of your team’s performance to gain a baseline understanding of your current state and define what improvement and success would look like. Next, set actionable and realistic goals to help you achieve success. Define the KPIs that will quantify success and guide you on your journey. Finally, select the metrics that matter to your team and introduce programs for measuring and tracking your performance.
- Outline roles and responsibilities: Establishing clear roles and responsibilities across your department for each phase in the work order lifecycle will promote efficiency, and discourage rework, non-compliance, or an excess backlog of incomplete tasks.
- Take a proactive approach: Where cost-effective, you should aim for more proactive and predictive maintenance and asset management. Addressing signs of trouble preemptively always pays off by helping maintenance teams avoid unplanned downtime, last-minute runs for parts, or workplace hazards.
- Implement a Computerized Maintenance Management System (CMMS): CMMS software allows for digital work order management and inventory management. Their suites of features make it easier for maintenance teams to reach their potential, reducing costs and manual workloads along the way.
Free Maintenance Work Order Template
Free customizable work order template with best practices gained from thousands of customers that will help you standardized work orders.
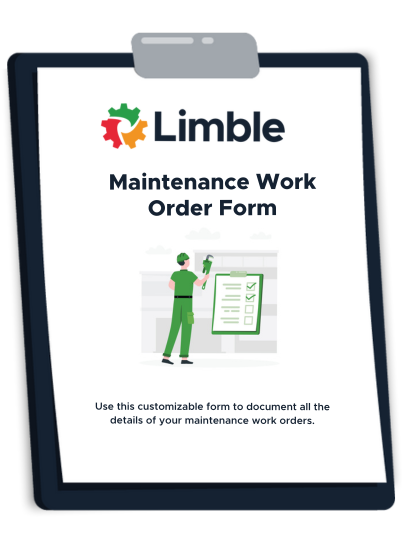
Explore our free maintenance templates library
9 Tips for writing a good work order
- Requestor’s name and contact details: Who initiated the work order? Including their name and contact information makes it easy to ask follow-up questions.
- Approver’s name and contact details: Tracking WO approval promotes accountability across your maintenance program and simplifies scheduling.
- Assigned technician’s name and contact details: Whether you’re assigning a task to a single team member or a team of technicians, including their details ensures you can track their performance and connect for follow-up conversations.
- Details on the affected piece of equipment: Your team is responsible for maintaining dozens or even hundreds of assets, potentially spread across numerous locations. To avoid wasted time, bar codes, serial numbers, or QR codes can help ensure they know how and where to find the asset they need.
- Description of task: Include a step-by-step guide for seeing the task through. Try to address any questions that might arise by including answers to FAQs on your work order. A maintenance checklist can help technicians ensure they’ve completed the task correctly.
- Relevant dates: In addition to the dates you opened and assigned the request, make sure to include a clear due date and space for the technician to note their actual completion date.
- Urgency: Some maintenance tasks should never go into your maintenance backlog. Details on urgency will help managers organize their priorities accordingly to eliminate safety risks or mitigate the impact of shutdowns.
- Required parts and materials: You don’t want your technicians stopping and starting because they don’t have everything they need. Make sure your work order lists all the necessary tools for completing the task. Learn how building maintenance kits can make equipping your team simpler.
- Images: Illustrations and photos can help make it simpler to both create and carry out work orders.
Benefits of work order management software
The work order tracking and managing features of CMMS platforms like Limble offer distinct advantages over paper work orders, whiteboards, and Excel spreadsheets.
- A centralized location for data and documents: A quality CMMS platform offers a single location for managing your full maintenance and work order management program. With Limble, your team can even access these dashboards, manage their service requests, and execute maintenance tasks from their mobile devices.
- More access to real-time data: CMMS platforms put both historical and real-time data at your maintenance staff’s fingertips. This improves decision-making, drives positive changes, and makes it possible to continually eliminate inefficiencies.
- Simplified regulatory compliance: Keeping maintenance histories handy and automating routine inspections takes the stress and hard work of passing internal and industrial audits.
Improve work order management today
Ready to improve your approach to work order management? Standardize your WO format and workflow with the help of these customizable work order templates. Better yet, learn more about digitizing, automating, and optimizing work order management with Limble.
Comments are closed.