Mean Time To Repair (MTTR)
Mean Time to Repair (MTTR) measures the average time your maintenance team spends getting an asset or system up and running after a failure.
Mean Time to Repair is one of the essential maintenance metrics. It measures the average amount of time it takes for your technicians to repair equipment and systems. As part of a strategic maintenance program, it helps you assess the maintainability of assets.
The repair process includes everything from diagnosing the problem through bringing the equipment back into normal operation. The metric does not account for the time you spend waiting on spare parts.Â
Low-MTTR assets take less time to service and are considered highly maintainable. Alternatively, assets with high MTTR values typically indicate room for improvement.Â
Table of Contents
- Mean Time to Repair (MTTR) measures the average time your maintenance team spends getting an asset or system up and running after a failure.
- MTTR and MTBF
- Calculating MTTR
- MTTR formula
- Benefits of MTTR
- Challenges in measuring MTTR
- When is calculating Mean Time to Repair useful?
- More essential maintenance metrics
- Different types of MTTR
- Six best practices for improving Mean Time to Repair
- The Essential Guide to CMMS
- FAQ
- Related Content
MTTR and MTBF
MTTR is often used alongside Mean Time Between Failures (MTBF) to measure the availability and reliability of assets. MTBF refers to the average amount of time machinery remains operational before failing. Tracking both metrics can help to identify system-wide failures and promote a more proactive approach to maintenance.Â
Calculating MTTR
To calculate the MTTR value for an asset, you’ll need three types of data:Â
- The total number of repairs the asset has required over a given period of time
- Total labor hours spent on repairs throughout that time frame
It is important to factor in the time you spend detecting a problem, the time you spend diagnosing its root cause, and the time you spend on actual repairs. Â
MTTR formula
The MTTR formula involves dividing the total time spent on repairs over a specific time period by the total number of incidents.Â
For example, let’s say you experienced four system failures in the last month and these failures led to four hours of total maintenance time.Â
4 hours of maintenance time / 4 total repairs = 1 hourÂ
MTTR = 1 hour
The formula for calculating MTTR to assess the maintainability of key assets.
Your ideal MTTR value will depend on your industry and your organization’s unique goal. Maintenance teams should stove to keep the figure low by boosting efficiency and adopting more proactive methods. Â
Benefits of MTTR
Tracking, reporting on, and improving MTTR values brings many benefits to maintenance teams and their organizations.Â
- Benchmark your maintenance team’s performance: Paying closer attention to metrics like MTTR offers a useful benchmark for assessing your team’s performance and iterating on improvements.Â
- Reduce downtime: Tracking MTTR helps to identify trends that could point to roadblocks in the repair process.  Â
- Maximize uptime: Identifying and correcting the factors that lead to protracted repair times will have a direct impact on machine uptime.Â
- Save on repairs: Lengthy repairs typically present a host of direct and indirect costs. Driving down MTTR could mean significant cost savings.Â
- Boost system reliability and performance: Addressing failure-prone assets and components will improve the overall maintainability, reliability, and performance of entire systems.Â
- Satisfy customers: More efficient systems with less unplanned downtime mean higher quality products and improvements to customer satisfaction and loyalty.
- Make better decisions: With more performance data at your disposal, you’ll make more informed decisions about improving the efficiency of your systems and the maintainability of your assets.
Challenges in measuring MTTR
Several factors may complicate your attempts to calculate MTTR.
- Data availability concerns: To dependably measure MTTR you need a method for consistently collecting the relevant data.Â
- Defining the word repair: What exactly qualifies as repair time? Do you start the clock when technicians first detect a problem or when their hands-on work begins in earnest? Aligning on the definition of repair is essential for achieving accurate calculations.Â
- Multiple failures at once: If a system or asset experiences numerous failures at the same time, you may struggle to distinguish between the various related repair tasks and assign start and end times.Â
When is calculating Mean Time to Repair useful?
Paying close attention to MTTR pays off in big ways. Here are just a few examples of how your team might use these calculations.
- Repair vs. replace discussions: When you’re trying to decide between repairing an asset or replacing it altogether, MTTR calculations can offer plenty of guidance. If you notice increases in MTTR for legacy equipment, replacement may prove more cost effective.Â
- Improving inventory management: Consistently high MTTR values may signify an inefficient approach to ordering and inventory management for spare parts. If you can trace a significant amount of downtime to specific sections of your plant or specific types of machinery, consider auditing your spare parts inventory to ensure technicians always have access to high-quality, clearly labeled tools.Â
- Refining schedules for preventive maintenance: Evaluating reacting maintenance through MTTR calculations can help you improve your approach to preventive maintenance. High MTTR values may point out issues with your processes for issuing preventive maintenance work orders.
More essential maintenance metrics
MTTR is just one of the maintenance KPIs your organization should track to gauge its performance and identify opportunities to make positive changes.Â
- Mean Time to Failure (MTTF): Similar to MTBF, this metric is used to track the average operating time of non-repairable assets.Â
- Mean Time to Acknowledge (MTTA): This incident metric deals with the time between a defect alert and the start of hands-on maintenance.Â
- Overall Equipment Effectiveness (OEE): This combination of availability, performance, and quality gives organizations a sense of their overall productivity and is a key component of lean manufacturing.
- Idle time: Distinct from downtime, this metric deals with the time operational machinery spends out of commission.
Different types of MTTR
Though Mean Time to Repair is the most common definition of MTTR used by maintenance professionals, you may encounter other metrics known by the same acronym.Â
- Mean Time to Recovery: This metric tells you how quickly you recover from breakdowns and outages. It offers a high-level overview of your repair and recovery processes’ effectiveness. It does not, however, help identify the root cause of equipment failures. Â
- Mean Time to Resolve: This type of MTTR includes the time spent helping ensure a problem does not happen again. It is often used in IT, DevOps, and cybersecurity contexts.Â
- Mean Time to Respond: Tracking this type of MTTR can help you identify bottlenecks in your incident management process. If response times are especially high, you may have issues with your alert system or your team’s workflow. Â
Make sure to clearly define MTTR and other incident metrics in discussions with your team and service level agreements (SLAs) with your buyers and suppliers.Â
How do you define MTTR?
Want to see Limble in action? Get started for free today!
Six best practices for improving Mean Time to Repair
Want to improve your incident response processes to reduce MTTR? Check out these tips for maintenance teams:Â
- Segment MTTR calculations to identify opportunities for improvement. Look at your MTTR data for specific locations, types of assets, or periods of time. This will help you establish a baseline and pinpoint areas where incremental changes will make a big impact.Â
- Optimize your spare parts management and asset inventory management processes. Taking these steps will ensure your team always has access to the resources it needs Â
- Use condition-monitoring sensors to track asset health and performance. Technology for real-time monitoring can help your team take a more proactive approach to maintenance while also speeding up the diagnosis and troubleshooting processes.   Â
- Streamline your repair processes. Establish and document clear standard operating procedures and checklists to guide team members through maintenance tasks
- Emphasize proper training. A well-informed team is an efficient team. Ensure that training programs prepare everyone to play their essential role. Fostering open communication and building a culture of continuous improvement will ensure assets stay highly maintainable throughout their full lifecycle.Â
- Implement a CMMS. With workflow automation, real-time performance tracking, and more, CMMS platforms simplify the transition from reactive to preventive maintenance.Â
Check out our essential guide to CMMS platforms to learn more about how Limble can evolve your maintenance function and improve performance across all key performance indicators.
The Essential Guide to CMMS
Download this helpful guide to everything a CMMS has to offer.
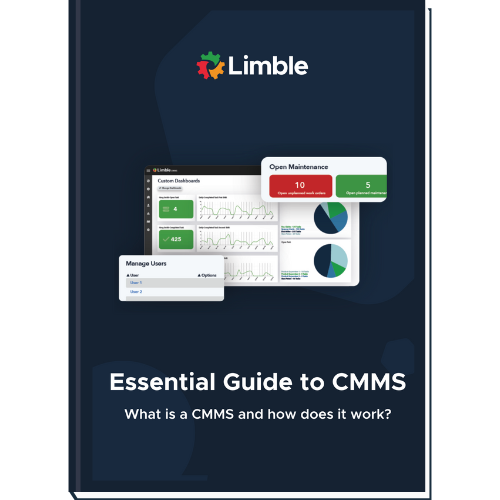
FAQ
Why use CMMS software to track maintenance metrics?
Using CMMS software simplifies tracking complex maintenance metrics, fosters data-driven decisions, enhancing efficiency, reducing downtime, and aiding in regulatory compliance all in one.
Table of Contents
- Mean Time to Repair (MTTR) measures the average time your maintenance team spends getting an asset or system up and running after a failure.
- MTTR and MTBF
- Calculating MTTR
- MTTR formula
- Benefits of MTTR
- Challenges in measuring MTTR
- When is calculating Mean Time to Repair useful?
- More essential maintenance metrics
- Different types of MTTR
- Six best practices for improving Mean Time to Repair
- The Essential Guide to CMMS
- FAQ
- Related Content
Is Limble Mobile CMMS app user friendly?
Limble is consistently rated Easiest-to-Use CMMS on review sites like G2, Capterra, and Software Advice. And our customers agree. With our mobile CMMS app, teams experience 30%+ better productivity, on average, requiring little to no training or ramp-up time. Our CMMS app can travel with your team, no matter where they go! Visit our App Store or Google Play for more information.
Table of Contents
- Mean Time to Repair (MTTR) measures the average time your maintenance team spends getting an asset or system up and running after a failure.
- MTTR and MTBF
- Calculating MTTR
- MTTR formula
- Benefits of MTTR
- Challenges in measuring MTTR
- When is calculating Mean Time to Repair useful?
- More essential maintenance metrics
- Different types of MTTR
- Six best practices for improving Mean Time to Repair
- The Essential Guide to CMMS
- FAQ
- Related Content
Can I connect to other systems?
Limble provides seamless, pre-built CMMS Integrations with the most widely used software systems. That means no help from a developer or your IT team is required. Learn more about our integrations.
Table of Contents
- Mean Time to Repair (MTTR) measures the average time your maintenance team spends getting an asset or system up and running after a failure.
- MTTR and MTBF
- Calculating MTTR
- MTTR formula
- Benefits of MTTR
- Challenges in measuring MTTR
- When is calculating Mean Time to Repair useful?
- More essential maintenance metrics
- Different types of MTTR
- Six best practices for improving Mean Time to Repair
- The Essential Guide to CMMS
- FAQ
- Related Content
How secure is the Limble CMMS platform?
At Limble, our world-class data security practices ensure your account information is safe. We use state-of-the-art technologies and industry best practices to maintain a secure infrastructure, including SOC-II Type II certification, regular penetration testing, and continuous security training for our staff.
Table of Contents
- Mean Time to Repair (MTTR) measures the average time your maintenance team spends getting an asset or system up and running after a failure.
- MTTR and MTBF
- Calculating MTTR
- MTTR formula
- Benefits of MTTR
- Challenges in measuring MTTR
- When is calculating Mean Time to Repair useful?
- More essential maintenance metrics
- Different types of MTTR
- Six best practices for improving Mean Time to Repair
- The Essential Guide to CMMS
- FAQ
- Related Content