CMMS and CAFM solutions play pivotal roles in automating and streamlining facility management and maintenance operations.
In this article, we will discuss common use cases, highlight similarities and differences, and compare their features.
By the end, you should have the insights you need to select the right solution for your specific needs, whether that’s streamlining maintenance tasks, managing assets, or optimizing your overall facility management efforts.
What is CAFM software?
CAFM stands for Computer-Aided Facilities Management. CAFM software is designed to streamline various aspects of facility operations and maintenance. It helps facility managers streamline processes, improve space utilization, track assets, schedule maintenance tasks, and generate reports for informed decision-making.
It is useful to think of it as a comprehensive commercial facility or building management tool. Hence, it is widely used in commercial buildings, healthcare facilities, educational institutions, and other large-scale facilities.
Organizations use CAFM solutions to:
- Efficiently manage space utilization and allocation
- Track and manage physical assets throughout their lifecycle
- Streamline facility maintenance and work order management
- Optimize move management and space planning processes
- Improve energy management and sustainability initiatives
- Generate comprehensive reports and analytics for informed decision-making
- Streamline lease management and tracking
- Optimize resource allocation and utilization within the facility
- Streamline vendor management and contract tracking
- Support strategic facility planning and budgeting processes.
The Essential Guide to CMMS
The Essential Guide to CMMS
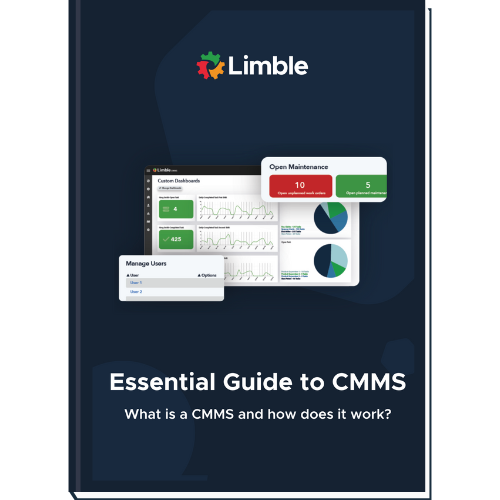
What is CMMS software?
CMMS stands for Computerized Maintenance Management System. CMMS software exists to help maintenance and facility managers organize, automate, and streamline every aspect of asset management and maintenance work.
CMMS makes your maintenance department drastically more efficient. It also reduces operational costs, minimizes equipment downtime, and automates many of those pesky administrative tasks.
Just to give you an idea of the effects, here are the average benefits for organizations that implement Limble CMMS:
Businesses use CMMS to:
- Manage incoming maintenance work requests
- Plan, schedule, and organize all maintenance work
- Track and manage physical assets throughout their lifecycle (from purchase to disposal)
- Keep track of their maintenance inventory
- Have an in-depth overview of all maintenance-related costs and activities
- Ensure compliance with regulations and safety standards
- Generate reports and analytics for data-driven decision-making
- Streamline communication and collaboration among maintenance teams
- Improve overall operational efficiency.
CMMS vs CAFM — the differences
The main differences between CMMS and CAFM can be found by looking at what they focus on, the scope of the features they offer, and by looking at who are the common users of the respective solutions.
Focus
CMMS primarily focuses on managing and tracking maintenance activities, such as work orders, preventive maintenance schedules, equipment repairs, and inventory management. It is geared towards optimizing maintenance operations and improving equipment reliability.
CAFM focuses on broader facility management functions beyond maintenance, including space management, move management, lease management, asset management, and sustainability tracking. It aims to enhance the overall efficiency and effectiveness of facility operations.
Scope
CMMS is primarily used within maintenance departments and is typically more task-oriented. It helps manage maintenance activities, work orders, spare parts, and equipment history.
CAFM has a broader scope and is used across multiple departments within an organization. It encompasses facility planning, space utilization, asset tracking, lease management, and other facility management functions.
Users
CMMS is predominantly used by your maintenance staff: managers, supervisors, planners, and technicians that are directly involved in maintenance activities and asset management.
CAFM is used by facility managers, space planners, asset managers, and other stakeholders involved in facility management and operations.
CMMS vs CAFM — the similarities
While CMMS and CAFM solutions have distinct differences, you will often find them clumped up in the same category — maintenance software. Here are six reasons why:
- Both CMMS and CAFM are software-based solutions that leverage technology to improve operational efficiency and effectiveness.
- Both solutions help manage and organize data related to physical assets and maintenance activities. In other words, they serve as a centralized repository for storing and accessing information.
- Both CMMS and CAFM solutions typically include features for managing maintenance work. Users can create, assign, track, and prioritize maintenance tasks and requests.
- Both solutions allow you to track physical assets. You can record various asset details and track their location, maintenance history, and performance metrics.
- Better CMMS and CAFM systems always come with extensive reporting and analytics capabilities. Users can generate various reports and access data-driven insights to monitor maintenance performance, asset utilization, and other maintenance KPIs.
- To streamline internal processes and data exchange, CMMS and CAFM can be integrated with different enterprise systems, such as inventory management, procurement, financial systems, or other specialized software. For reference, check the list of Limble CMMS integrations.
For those that want a more detailed breakdown of their functionality, we take a closer look at their features in the following section.
CMMS vs CAFM — feature comparison
Different CAFM providers offer different functionality. For example, some CAFM solutions come with an integrated CMMS, offering the best of both worlds (at a price).
There’s a similar story with CMMS vendors. While spare parts inventory modules and mobile app support have become an industry standard, you will not find them in every CMMS software.
To simplify this comparison, the table below lists standard features you will find in the respective software.
Let’s dive a little deeper into these features to see what they actually bring to the table.
Standard CAFM features
Different CAFM systems provide different functionality. That being said, the core features we discuss below should be found in any better CAFM solution.
- Space planning & management: Integrated CAFM systems optimize facility usage by storing asset information and floorplans, recommending layouts based on space availability, and mapping equipment utilization for process optimization.
- Maintenance management: CAFM software schedules maintenance operations based on time intervals or equipment performance, while also managing assets throughout their lifecycle for efficient maintenance practices.
- Physical building administration: CAFM software connects to building equipment like HVAC units and lighting, enabling remote control, monitoring meter readings, and providing alerts for maintenance needs.
- Space reservations: It streamlines leasing and real-estate management, tracking long-term leases, contract statuses, facility rentals, and incidents/events to generate extra revenue and efficiently manage space allocation.
- Reporting: Serves as a database for incident reports, allowing easy tracking and retrieval for audits and inspections, enhancing safety and compliance measures.
- Energy performance analysis: The software monitors energy usage and provides insights to evaluate environmental impact and sustainability initiatives.
Standard CMMS features
Different CMMS systems offer varying functionality, but there are core features that should be present in any robust CMMS solution. These standard CMMS features empower organizations to streamline their maintenance operations and maximize asset efficiency.
- Work order management: CMMS software allows users to efficiently manage and track maintenance work orders, from ticket creation to completion. It enables the scheduling, assignment, and tracking of tasks, ensuring timely maintenance execution and reducing downtime.
- Preventive maintenance: With CMMS, organizations can implement proactive maintenance strategies by scheduling routine inspections, servicing, and replacements based on predefined intervals or usage metrics. This helps prevent equipment failures, prolongs asset lifespan, and reduces unexpected breakdowns.
- Predictive maintenance: CMMS systems leverage advanced technologies such as machine learning and predictive analytics to monitor equipment health and predict maintenance needs. By analyzing historical data and real-time sensor readings, the software identifies potential issues before they escalate, enabling timely interventions and minimizing unplanned downtime.
- Asset management: CMMS solutions facilitate comprehensive asset management by providing a centralized repository for asset information, including specifications, maintenance history, and documentation. This enables an efficient tracking of asset location, status, and lifecycle management, ensuring optimal utilization and informed decision-making.
- Spare parts inventory management: The software simplifies inventory management by tracking and optimizing spare parts inventory. It helps organizations maintain adequate stock levels, track usage, and generate reorder notifications to ensure timely availability of critical components.
- Analytics and reporting: Offers robust reporting and analytics capabilities, allowing organizations to gain insights into maintenance activities, asset performance, costs, and resource allocation. This data-driven approach enables informed decision-making, identifies trends, and supports continuous improvement initiatives.
Should CMMS and CAFM be used together?
While there is a certain overlap between the features they offer, organizations with complex facility management needs will find it useful to implement and integrate both solutions.
Many CAFM solutions will have limited functionality for organizing and managing maintenance work. In that scenario, an organization can integrate a CMMS with their CAFM solution to offer comprehensive support for all of their maintenance management activities.
While that works for organizations that need all-encompassing facility management software, many businesses just need a better way to manage their assets, inventory, and maintenance work. In that case, modern CMMS software will be more than enough.
Ultimately, it all depends on the specific needs of your organization. What features do you actually need — and how much you are able/willing to pay for them.
If you’re looking for a reliable CMMS solution that offers comprehensive features and a user-friendly interface, consider exploring Limble CMMS by scheduling a quick product demo or starting a free trial.