Workplace safety procedures are critical to reducing the occurrence of injuries, accidents and fatalities. This is especially true for high-risk industries such as manufacturing, construction, and power generation. According to the U.S. Bureau of Labor Statistics (BLS), 2021 saw roughly 2.8 million nonfatal workplace injuries and illnesses. The manufacturing industry alone accounted for 15% of these incidents and saw an incidence rate of 3.3 cases for every 100 full-time workers.
The value of workplace safety precautions and procedures
Unsafe conditions are a threat to the well-being of your employees as well as your bottom line. Poor safety management can translate into lost productivity, inflated medical expenses, and bloated administrative costs. The National Safety Council (NSC) estimates the value of these losses at more than $171 billion in 2022 alone. That massive figure underscores the value of effective workplace safety procedures.
Safety procedures are designed to prevent accidents and injuries, safeguard employee health, and ensure compliance with regulatory standards across all workspaces. Effective safety procedures can also improve your work environment, enhance productivity, and reduce costs.
What are workplace safety policies and procedures?
Workplace safety procedures are standardized protocols designed to ensure a healthy and safe working environment. These procedures are especially important in industries where the use of certain systems, machinery, and materials can pose a heightened safety risk such as manufacturing, construction, healthcare, and transportation.
Broadly speaking, safety procedures are designed to prevent accidents, injuries, illnesses, and fatalities. Workplace safety procedures will typically include:
- Formal written instructions outlining specific steps for the safe performance of operational and maintenance tasks
- Preventive measures such as routine maintenance and regularly scheduled inspections aimed at preventing equipment failure and consequent accidents and injuries
- Workplace safety training aimed at educating employees about potential hazards and offering a guide to implementing safe practices and building a safety culture
- Emergency preparedness plans and drills to ensure that employees know how to respond in the event of an emergency
- Regulatory compliance efforts such as aligning with federal safety standards established by bodies such as the Occupational Safety and Health Administration (OSHA) and the Centers for Disease Control (CDC)
Safety procedures in action
Safety procedures play an important part in maintaining a safe workplace, maximizing productivity, and achieving regulatory compliance across an extremely wide spectrum of industries and organizations.
- Manufacturing safety procedures will typically address Lockout/Tagout (LOTO), Personal Protective Equipment (PPE) guidelines, Hazard Communication protocols, and more.
- Construction safety procedures will typically address fall protection measures, Site Safety Plans, equipment safety protocols, and more.
- Healthcare safety procedures will typically address protocols for infection control, patient transfer, hazardous drug handling, and more.
- Mining safety procedures will typically address ventilation systems, ground control techniques, evacuation strategies, and emergency cave-in response plans.
- Logistics and transportation safety procedures will typically address driver safety training, hazardous materials handling, and ergonomic assessment of repetitive or physically demanding tasks.
Types of safety procedures
The types of workplace safety procedures you introduce to your facilities will depend on several factors including the nature of your operation, the equipment you use, the raw materials handled by your personnel, and more.
- Emergency response and evacuation plans including differentiated procedures for incidents such as fires, chemical spills, and natural disasters
- Personal Protective Equipment (PPE) programs with comprehensive guidelines for the use, maintenance, cleaning, and storage of safety equipment such as hard hats, gloves, goggles, respirators, and more
- Lockout/Tagout (LOTO) procedures ensure that machinery is properly powered down and locked during maintenance or repair work
- Training programs designed to educate employees about workplace hazards, instruct in safe practices, and onboard new hires
- Incident reporting procedures for documenting and investigating workplace incidents, identifying root causes, and implementing corrective actions
- Ergonomic assessments aimed at evaluating workplace design and work practices to reduce strain, improve comfort, and prevent musculoskeletal disorders and other ergonomic-related injuries
- Chemical safety procedures for handling, labeling, storing, and disposing of hazardous chemicals safely, as well as creating Safety Data Sheets (SDS)
Preventing common safety hazards
Many standard workplace procedures are designed around common safety hazards. Below, we take a closer look at some of the most common workplace hazards and the procedural strategies typically used to prevent the risks posed by these hazards.
Slips, trips, and falls
Wet surfaces, obstructed pathways, and inefficient guardrails can result in serious falls and injuries.
Prevention methods may include:
- Housekeeping procedures for keeping floors clean and dry, eliminating clutter, and maintaining clear walkways
- Floor markings and signage to indicate wet floors and other slip hazardous
- Fall prevention measures like guardrails, safety nets, and harnesses
Repetitive strain injuries
Strains and musculoskeletal injuries can result from repetitive tasks, poorly designed tools, and constrictive workstations. Prevention methods may include:
- Ergonomic tools and ergonomically designed workstations
- Adjustable chairs and desks
- Task rotation and routine stretching breaks
Forklift accidents
The standard warehouse forklift will typically weigh somewhere between 8000 and 9000 pounds and is susceptible to tipping when used improperly, which can cause accidents and fatalities. Prevention safety tips may include:
- Proper certification for all forklift operators
- Routine maintenance, lubrication, and calibration
- Operation guidelines based on manufacturer recommendations
Chemical hazards
Exposure to certain chemical substances can lead to a variety of health and safety risks including skin and eye irritation, respiratory issues, and illness.
Prevention safety tips may include:
- Safety Data Sheets (SDS) with instructions on safe handling and emergency measures
- Clear labeling and storage guidelines
- Comprehensive employee training for safe handling
Machine hazards
Machines and equipment with moving parts can cause crushing, amputation, and fatalities if used improperly or if accidentally powered up during maintenance.
Prevention safety tips may include:
- Lockout/Tagout (LOTO) procedures to ensure machinery is in shut-off mode before maintenance;
- Machine guarding to protect operators against moving parts
- Standardized safe operating procedures
Electrical hazards and fire hazards
Electrical equipment can lead to fire safety risks, as well as burns, shocks, and electrocution.
Prevention safety tips may include:
- Routine inspection and testing of electrical equipment, wiring, and circuits
- Lockout/Tagout (LOTO) procedures to ensure electricity is powered down before maintenance
- Comprehensive fire safety program including drilling, evacuation routes, and sufficient emergency exits
Maintenance and workplace safety
Maintenance personnel will typically play an instrumental role in carrying out workplace safety procedures. Indeed, many of these procedures will fall under the umbrella of preventive maintenance. Regular inspections, timely repairs, and routine upkeep are all central to workplace safety.
Below, we take a closer look at the preventive maintenance tasks that contribute directly to effective workplace safety:
- Regular inspection of machinery, equipment, and systems to verify proper functionality and identify potential safety hazards
- Scheduled maintenance of physical assets, including lubrication, parts replacement, and cleaning to prevent the safety risks that come with malfunction or breakdown
- Facilities risk assessment aimed at identifying potential safety concerns resulting from obstructed ventilation, outdated fire safety equipment, inadequate machine guards, etc.
- Lockout/Tagout (LOTO) procedures to ensure machinery is properly powered down, locked, and inoperable during scheduled maintenance, inspections, and repairs
- Emergency response, ensuring maintenance technicians with relevant specialized knowledge and certifications are among the first responders to equipment-related emergencies
Digitizing safety procedures with a CMMS
A Computerized Maintenance Management System (CMMS) can streamline, simplify, and optimize your preventive maintenance program. This also makes a CMMS a valuable solution for streamlining, simplifying, and optimizing your workplace safety program. The right platform can make it easy to implement and automate a variety of maintenance strategies that are essential to an effective workplace safety program.
Key CMMS features include:
- Automated scheduling of routine maintenance, inspections, and safety checks
- Standardized workflows, ensuring safety procedures are performed according to established protocols
- Regulatory compliance support including alerts for inspection dates, safety certifications, and compliance deadlines
- Reporting and analysis on safety performance, illuminating areas of need, and providing insights for continuous improvement
- Centralized safety data, giving employees easy access to safety manuals, procedure documents, and training materials
- Digital records and audit trail of all maintenance activities, safety inspections, and incident reports
For more information on how a leading-edge CMMS platform can simultaneously enhance your organization’s safety procedures and the performance of your maintenance program, check out Limble’s Essential Guide to CMMS.
Free CMMS Buyer's Guide
Discover everything you need to know about CMMS in this comprehensive guide. Begin your maintenance journey now!
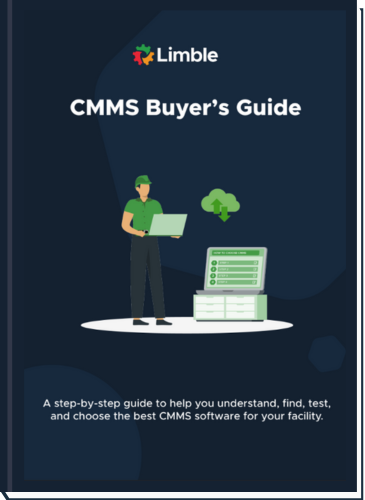
Resources for optimizing safety procedures
Workplace safety procedures should be informed by a variety of sources including internal data, manufacturer recommendations, and regulatory conditions. Fortunately, there are many federal regulatory agencies and professional associations that provide clear and detailed guidelines for achieving workplace safety compliance.
Below are a few leading resources to consult as you build, update, or improve your workplace safety procedures:
- Occupational Safety and Health Administration (OSHA) offers a wealth of resources geared toward employers including a summary of employer responsibilities, a full index of support services for Compliance Assistance, Education, and Training, and access to free, onsite consultation.
- Centers for Disease Control and Prevention (CDC) provides a forum for employers that includes a library of tools for health promotion, models for implementation of workplace safety programs, templates for training programs, and more.
- Limble CMMS offers powerful compliance solutions designed to ensure adherence to regulatory requirements, improve audit performance, and effectively document all maintenance activities, safety inspections, and equipment testing procedures. With helpful task checklists, work order tracking, and downtime reporting, Limble’s compliance and audit solutions are a vital component of an effective workplace safety program.