Precision Maintenance
Learn how precision maintenance programs extend the lifecycle of assets, maximize organizational efficiency, and more.
What is precision maintenance?
Precision maintenance is any program in which maintenance teams adhere to established best practices and use standard operating procedures (SOPs) to optimize equipment reliability, availability, uptime, efficiency, and performance. A precision maintenance program emphasizes safety, consistency, and attention to detail with the help of these SOPs, thorough training, and consistent, data-backed improvements.
From routine lubrication ro emergency repair, precision maintenance leaves no room for improvisation or guess work. Precise asset management and maintenance programs outline the tools and techniques necessary for meeting industry standards every time.
You can introduce a precision maintenance program alongside other maintenance strategies like preventive, predictive, and prescriptive maintenance. Those strategies focus on the when of maintenance tasks. Precision maintenance focuses on the how.
Why is precision maintenance important?
Giving two maintenance technicians the same work order doesn’t guarantee they’ll complete the task in the same way. If instructions are too vague, technicians are forced to draw their own conclusions and chart their own course. This leads to variability, one of the root causes of excess waste, cost, and downtime in production and maintenance. Defining precise steps for every maintenance task discourages variability.
It may take years of effort to build an effective precision maintenance program, but your work will pay off. Aside from improved consistency, there are many other benefits of precision maintenance management.
- By establishing precise standards for carrying out maintenance tasks, precision maintenance programs make it easy for technicians to quickly and efficiently service assets, reducing downtime.
- A precision approach to asset maintenance helps extend each piece of equipment’s useful life while improving availability, reliability, effectiveness, and efficiency.
- With a precision maintenance plan, you’ll significantly improve your First Time Fixed Rate and reduce the likelihood of equipment failure.
- Precision maintenance reduces overall maintenance costs and contributes to improvements in product quality.
- Taking the time to design, implement, and perfect a precision maintenance program goes a long way toward establishing a strong maintenance culture.
Checklist for Creating a Preventive Maintenance Plan
Following a consistent Preventive Maintenance Plan can make life easier. Use this checklist to create your own!
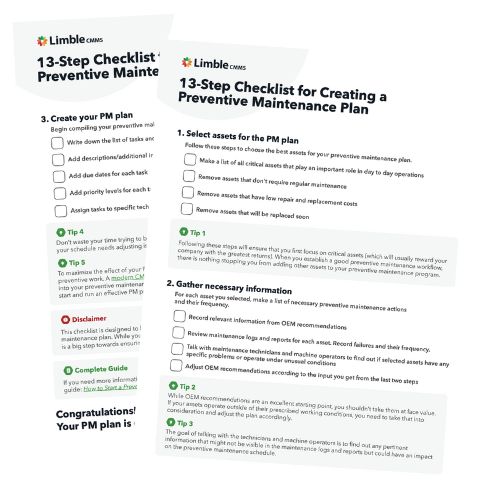
Some examples of precision maintenance and asset management
Your precision maintenance program will affect day-to-day operations at every level thanks to the standards it will establish and the cultural shifts it will encourage.
- Precise training: All maintenance technicians receive the necessary training and certifications for completing their tasks, handling relevant equipment, following safety procedures, and contributing to workplace culture.
- Precise maintenance planning and scheduling: Every element of every maintenance task gets the attention it needs, resulting in well-defined SOPs complete with detailed instructions, timelines, and more.
- Precise task completion: Technicians service equipment with an aim to optimize each asset’s performance and useful life while ensuring they follow established procedures.
- Precise inventory management: The highest quality tools and components are stored carefully so that they’re always secure and easy to find.
- Precise analytics and performance management: Your team establishes key metrics and sets goals based on industry and internal benchmark data, always looking for opportunities to improve.
4 steps for implementing a precision maintenance program
A program for precision maintenance improves the efficacy of all maintenance work to boost equipment performance, availability, and reliability. Once you have the resources in place for introducing precision maintenance, it’s time to get your program off the ground.
You can break this process down into four steps.
- Agree on a statement of intent
- Inventory your measurement tools
- Create the necessary documentation
- Insist on continuous improvement
Agree on a statement of intent
For a new maintenance reliability program to work, you need your full team on board. Start by collaboratively drafting a statement of intent that describes what you hope to accomplish through more precise, strategic maintenance.
Avoid flowery prose and abstract ideas. Focus on establishing quantifiable objectives that will help you develop metrics for monitoring the effectiveness of the program.
Inventory your measurement tools
Make sure you have all the tools you need to execute maintenance tasks on your assets. Your repertoire will likely include tools for assessing machine vibration, temperature, and other performance factors. A good program for maintenance depends on a broad selection of carefully stored tools capable of providing reliable, repeatable measurements.
Create the necessary documentation
An effective maintenance program requires three different types of documents.
- Operational documents: These cover the processes and procedures you or your technicians will carry out on specific machines. They outline standard procedures, workflows, and sequences for carrying out maintenance tasks. This category also includes maintenance documentation that outlines specifications like temperature and pressure thresholds.
- Tactical documents: These capture the results of complete tasks over defined periods of time. They aggregate results to help gauge performance against your maintenance plan’s goals.
- Strategic documents: These communicate the results of maintenance activities in formats like scorecards. They support program governance and indicate performance toward short- and long-term strategic objectives.
Requirements for a precision maintenance program
Do you have what it takes to introduce more precise maintenance processes and see the benefits?
You’ll need plenty of high-performing systems in place to get a new maintenance program off the ground and optimize it in the long term.
Well-trained, motivated maintenance technicians
To keep your program running, you’ll need a team with the right hands-on experience, skill set, and attitude. Your team’s technicians should all understand the crucial importance of diligent execution and compliance with best practices.
An effective preventive or predictive maintenance program
You’ll see more benefit from precision maintenance if you’ve already secured buy-in for more proactive processes and established a dependable program for preventive or predictive maintenance. This existing program will set you up for success and offer a benchmark for assessing and improving performance.
Effective and repeatable work procedures
A precise maintenance program depends on SOPs supported by detailed workflows. These guide technicians through tasks step by step and include any information they might need to guarantee a job well done.
A system to support continuous improvement
Using a continuous loop system to capture failures, analyze them, and respond with corrective action helps to discourage their recurrence and improve both equipment and technician performance on an ongoing basis.
Calibrated measuring tools
“Close enough” is never close enough. A precision maintenance program requires highly precise measurements from calibrated tools. Make sure your technicians and mechanics have access to high-quality tools and repeatable processes for achieving accurate measurements each time. You don’t want them managing shaft alignment or measuring vibration levels with sub-par instruments.
High-quality spares and consumables
Original equipment manufacturers (OEMs) specify the spare parts and consumable necessary for ensuring their assets operate to their fullest potential. Purchasing cheap alternatives to save money in the short term will introduce reliability issues that ultimately shorten an asset’s lifespan.
Want to see Limble in action? Get started for free today!
A computerized maintenance management system (CMMS)
Robust maintenance management systems provide the backbone of precision maintenance programs by eliminating variability and building centralized databases for all essential documents and data.
Spreadsheets and stacks of paper are no longer sufficient for most organizations. A CMMS makes it simpler to store, manage, and access everything that goes into managing an effective maintenance program.
Learn more about one of the most crucial components of precision maintenance in our guide to everything CMMS and begin developing reliability solutions today.