Idle Time
Everything you ever needed to know about idle time.
What is idle time?
Idle time is a period of time in which an asset (machine or an employee) is ready and available, but is not doing anything productive. It is sometimes referred to as waiting time.
Examples of idle time:
- A machine is waiting for input material.
- An office employee waiting for a lost internet connection to come back.
- A truck on a construction site waiting for an excavator to move so it can get to its target location.
- A maintenance mechanic waiting for a circular saw to become available so he can finish his job.
It is crucial to understand and track idle time because it points to the gap between your existing output and your theoretical maximum productivity level. Simply put, every minute that your machine or employee is idle is a minute of lost productivity.
That being said, no business can run at 100% efficiency. Some level of idle time is inevitable. The goal of every manager should be to minimize idle time, not to eliminate it. Eliminating idle time is close to impossible and might only be considered for closed, highly-automated systems.
Is idle time the same as downtime?
Idle time is not the same as downtime. Broadly speaking, when we talk about idle time, the asset can run but it doesn’t. But when we talk about equipment downtime, the machine doesn’t run because it can’t.
In the context of idle time, the machine is capable of performing its intended function but for a certain reason, it doesn’t. There are many possible causes of machine idle time like:
- No input raw material
- Waiting for another machine to finish its job
- Different workflow and process inefficiencies
- Production needs to be slowed down or stopped (for reasons like inventory being at full capacity)
- Power outages or similar technical problems that are not related to the machine itself
On the other hand, when we talk about machine downtime, the asset is not operational for one of two reasons:
- Scheduled maintenance: This is when you schedule planned downtime to perform preventive maintenance on an asset. This is sometimes referred to as normal idle time because scheduled maintenance is something that needs to be performed to keep the machines in good condition.
- Machine failure: Unexpected machine breakdown that needs to be corrected before the machine can continue working. This can be referred to as abnormal idle time since it represents an event that is out of our control and hurts overall business productivity.
Because of this difference, maintenance teams should track planned and unplanned machine downtime separately from idle time.
Checklist for Creating a Preventive Maintenance Plan
Following a consistent Preventive Maintenance Plan can make life easier. Use this checklist to create your own!
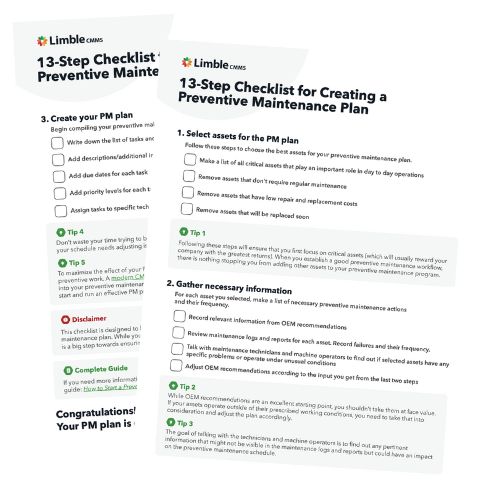
How to calculate idle time
Idle time represents the disparity between the time an asset is scheduled to run and how many actual productive hours have been spent.
For example, in an 8-hour shift, an employee might track 7 hours and 20 minutes of productive work. This suggests that they had 40 minutes of idle time, assuming they accurately tracked everything.
When we talk about machines, things get a bit more complicated. You have to differentiate between when a machine is simply turned on, and the actual productive work.
Let’s imagine that you have a machine that works for 16 hours. Let’s say it needs 10 minutes to power up, 5 minutes to shut down, has one 30 minute break for cleaning, and is stopped for 15 minutes for a shift change.
In other words, the machine is supposed to do productive work for 15 hours or 900 minutes.
During that time, there are many opportunities for a machine to idle:
- 5 minutes every hour waiting for input material (75 minutes in total)
- 10 additional minutes because a shift change took 25 instead of the usual 15 minutes
- 40 minutes because another machine in the production line had an unexpected breakdown
This would all amount to 125 minutes of idle time.
Would you need to reduce it to zero? Not necessarily. Maybe those 5 minutes every hour are also important for machine operators to take necessary breaks or clean things up. That being said, you would definitely want to eliminate any idle time caused by unplanned machine breakdowns.
Maintenance Work Order Template Form
Using a maintenance work order form ensures easy documentation and adherence to Standard Operating Procedures for maintenance activities.
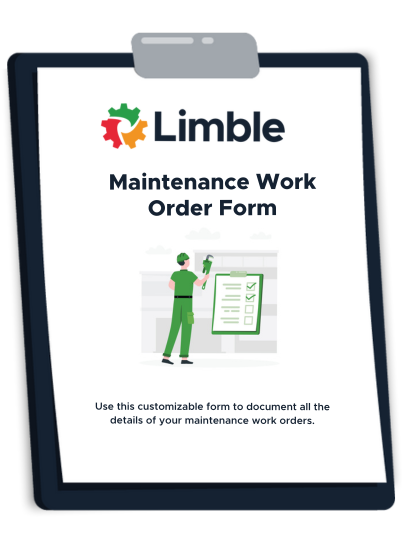
Common causes of idle time
While there are many potential causes of idle time, there are a few critical categories that these causes commonly fall ino. They are:
- Worker inefficiencies: Workers are not machines, and some are more efficient than others. Workers need breaks to avoid burnout. Some who are new may be learning or need additional training time. To address worker inefficiencies, you can work on improving onboarding processes, track work hours, and develop a company culture where everyone pulls their own weight.
- Process and workflow inefficiencies: Poorly optimized production and business processes such as waiting for approvals, and lack of available tools to perform assigned work orders are also common causes of idle time.
- Faulty equipment: Unexpected machine breakdowns can cause serious operational issues. Maintenance departments should use a CMMS system and have a proactive maintenance plan for all medium and high-priority assets.
- Accidents and natural disasters: These are mostly out of our control. However, companies should try and prepare for such events so that responses can be swift and brief, rather than to try to prevent them.
Want to see Limble in action? Get started for free today!
Identify, drill down, correct
Figuring out if idle time is a problem for your organization is often much easier than reducing it. The main challenge is finding the root cause of idle time.
Is a machine idling because the production process is inefficient? Is it because a preceding machine in the production line doesn’t work at full capacity? Is it because low-quality input material results in more intervention from machine operators, slowing the production down? Is it a combination of different reasons?
While reducing idle time is not always as straightforward as we would like it to be, the effect it can have on your bottom line makes minimizing it a worthwhile pursuit.
FAQ
Why use CMMS software to track maintenance metrics?
Using CMMS software simplifies tracking complex maintenance metrics, fosters data-driven decisions, enhancing efficiency, reducing downtime, and aiding in regulatory compliance all in one.
Is Limble Mobile CMMS app user friendly?
Limble is consistently rated Easiest-to-Use CMMS on review sites like G2, Capterra, and Software Advice. And our customers agree. With our mobile CMMS app, teams experience 30%+ better productivity, on average, requiring little to no training or ramp-up time. Our CMMS app can travel with your team, no matter where they go! Visit our App Store or Google Play for more information.
Can I connect to other systems?
Limble provides seamless, pre-built CMMS Integrations with the most widely used software systems. That means no help from a developer or your IT team is required. Learn more about our integrations.
How secure is the Limble CMMS platform?
At Limble, our world-class data security practices ensure your account information is safe. We use state-of-the-art technologies and industry best practices to maintain a secure infrastructure, including SOC-II Type II certification, regular penetration testing, and continuous security training for our staff.