Preventive Maintenance Compliance (PMC)
Preventive maintenance compliance (PMC) is a measurement that shows organizations how successfully they perform preventive maintenance tasks.
What is preventive maintenance compliance (PMC)?
Calculating PMC helps maintenance teams identify the percentage of preventive maintenance tasks they’ve completed compared to their total total number of scheduled maintenance tasks over a given period of time. It is a useful metric for identifying gaps in a preventative maintenance strategy.
Preventive maintenance work is a crucial aspect of any industrial facility’s maintenance plan. Compared to reactive maintenance, when a maintenance team tackles problems as they occur, preventive maintenance strategies are structured to help prevent problems from occurring in the first place.Â
How do manufacturers use PM compliance?
Preventive maintenance is only a helpful strategy when teams comply with it and complete tasks according to their maintenance schedule. If teams consistently miss PM work, companies face the risk of equipment failures and breakdowns.Â
Preventive maintenance compliance scores tell manufacturing organizations whether they are keeping up with their preventive maintenance activities. This way, they can determine if they need to make improvements to their PM program.Â
PMC is also helpful in preparing for audits and identifying long-term solutions to recurring issues. It increases the accountability of maintenance technicians when they work to improve the PMC score and helps companies improve their work order processes.Â
Calculating PM compliance scores
Calculating PM compliance is a relatively simple formula. A company must take their number of completed preventative maintenance tasks, divide that by their total scheduled PM tasks during this time frame, and multiply that number by 100 to get their PM compliance percentage.Â
Preventive maintenance compliance formula
Here’s a closer look at the numbers that go into calculating PM compliance.Â
(# of completed PM activities / # of scheduled PM activities) x 100 = PMC percentage
Let’s say a manufacturing plant has 200 scheduled PM activities over a 3-month period. 50 went incomplete, leaving just 150 tasks completed within that period. The PMC score would be 75%.Â
(150 / 200) x 100 = 75%
A general rule of thumb to minimize downtime and keep operations running smoothly is to aim for at least a 90% PMC score.Â
The 10% Rule
Even tasks completed within the time period of the PMC calculation can cause complications if maintenance teams complete them after the scheduled due date. Consistently late PM tasks are likely a sign of issues in your maintenance processes.Â
To gain a more accurate PMC score, it’s helpful to understand and use the 10% rule.Â
The 10% rule is simple: only tasks completed within a 10% window of their scheduled due date count as a completed PM task.Â
For example, if a part needs to be replaced every 90 days, it would only be considered complete (for the sake of the calculation) if it was complete within 9 days of (on either side) its scheduled due date.Â
Why is preventive maintenance compliance important?
Preventive maintenance compliance is a crucial measurement for maintenance teams to understand their current capabilities. If you consistently have a low PMC score, it’s probably time to change your strategy. This might entail increasing personnel, outsourcing, or finding another way to keep up with maintenance schedules.Â
If a company finds that they are consistently getting a low PMC score, then they won’t reap the full benefits of their preventive maintenance strategy.Â
Let’s look at some of those benefits:
- Reduced downtime: Staying on top of a preventive maintenance strategy reduces downtime by recognizing signs of trouble early and preventing machine failure. It is an essential part of asset management in order to keep equipment running smoothly.Â
- Asset longevity: When companies utilize preventive maintenance versus reactive maintenance, it minimizes equipment damage, improving its lifespan.Â
- Reduced costs: Repairing equipment, replacing parts, and replacing entire pieces of equipment gets costly. Preventive maintenance helps reduce these costs by preventing breakdowns and unnecessary labor.Â
- Improved compliance and safety: With fewer breakdowns and less need for reactive maintenance, equipment is safer to work with and stays compliant with industry and government regulations.Â
- Improved productivity: One piece of equipment breaking down can disrupt an entire production line. With fewer breakdowns, companies can increase uptime and keep operations running more efficiently.Â
While preventive maintenance strategies provide many advantages, there are some short-term disadvantages of transitioning to a new PM program. It takes hefty up-front technology investments to manage the plan, labor costs to run the maintenance schedule and activities, and more. In the long run, however, most companies find that transitioning to a PM plan is a solid investment.
Establishing preventive maintenance workflows
Preventive maintenance isn’t the right strategy for every facility and piece of equipment, but it is typically useful for medium-to-high priority assets that organizations intend to use for the long haul.Â
While every company has its own approach to preventive or proactive maintenance, here are a few basic steps to establish a preventive maintenance workflow. Â
Step 1: Take inventory of assets
Create a list of each asset that requires preventive maintenance. This will assist you in setting priorities and determining what maintenance tasks are necessary.Â
To stay organized, consider utilizing a Computerized Maintenance Management System (CMMS) to track assets and maintenance tasks.Â
Step 2: Identify preventive maintenance tasks
After taking inventory of your assets, make a list of all of the preventive maintenance tasks each piece of equipment requires. Having this tally will also help in calculating preventive maintenance compliance later.Â
Step 3: Set priorities
Determine which assets are most crucial for setting a preventive maintenance schedule. Assets that contribute to employee safety and that other assets rely on to keep daily operations running are a good place to start.Â
Step 4: Determine maintenance frequency
Refer to OEM manuals, company SOPs, and equipment historical data to determine the best frequency for tackling each preventive maintenance task.Â
Step 5: Set up a preventive maintenance schedule and checklist
Once you’ve determined priorities, what tasks are needed, and task frequency, set up a schedule and checklist that maintenance technicians can adhere to.Â
Need help getting started? Check out our free preventive maintenance checklist.Â
Step 6: Train and develop your team
Lastly, be sure to incorporate any new preventive maintenance plans or tasks into company SOPs and staff training to get the whole team up to speed.
Want to see Limble in action? Get started for free today!
More crucial maintenance metrics
Beyond PM compliance, other KPIs and metrics are also important for maintenance teams. These metrics help determine how well assets are maintained:Â
Mean time to repair (MTTR)
MTTR is the time it takes to fix an asset after it breaks down or a part breaks. It starts when the repair begins and ends when the asset is fully functional. This calculation helps organizations understand equipment downtime and determine if additional personnel, expertise, or assets are needed.Â
Mean time between failure (MTBF)
MTBF is the average time between the resolution of a specific asset’s failure and the next failure that occurs. Understanding this metric helps organizations plan their preventive maintenance tasks around these failures to prevent breakdowns and improve uptime.Â
More ways to improve your maintenance team’s performance
Low PM compliance can indicate larger problems in an organization’s maintenance program. Here are a few ways that companies can improve PM compliance and overall performance of their preventive maintenance activities:Â
- Audit PM tasks: Running an audit of your PM activities can help to determine if any PM tasks are unnecessary. Removing unnecessary tasks from a maintenance schedule helps free up time for maintenance techs to spend time on the priority tasks, thus improving the PMC.Â
- Utilize maintenance software: A Computerized Maintenance Management System (CMMS) is a crucial tool for enforcing compliance, evolving maintenance capabilities, and improving overall performance. It helps maintenance techs stay on task through notifications, real-time data, and more.Â
- Allocate sufficient resources: Audits and PMC calculations may reveal that organizations don’t have sufficient resources allocated for their PM program. Hiring additional personnel or finding other ways to get the right resources allocated toward a PM program will make a huge difference.Â
Implement these additional techniques into your PM strategy to see significant improvement in productivity.Â
To further improve your maintenance team’s performance, take advantage of our free preventive maintenance checklist.
The Essential Guide to CMMS
Download this helpful guide to everything a CMMS has to offer.
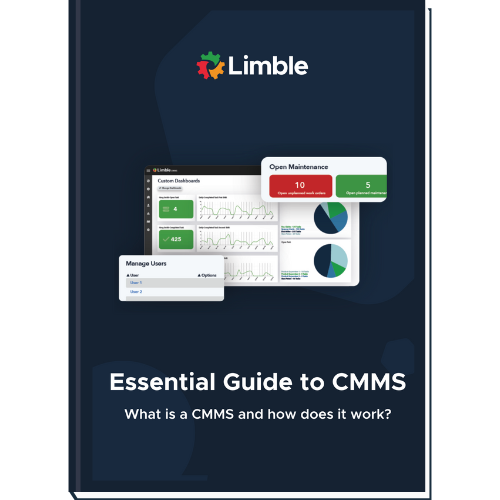
FAQ
Why use CMMS software to track maintenance metrics?
Using CMMS software simplifies tracking complex maintenance metrics, fosters data-driven decisions, enhancing efficiency, reducing downtime, and aiding in regulatory compliance all in one.
Is Limble Mobile CMMS app user friendly?
Limble is consistently rated Easiest-to-Use CMMS on review sites like G2, Capterra, and Software Advice. And our customers agree. With our mobile CMMS app, teams experience 30%+ better productivity, on average, requiring little to no training or ramp-up time. Our CMMS app can travel with your team, no matter where they go! Visit our App Store or Google Play for more information.
Can I connect to other systems?
Limble provides seamless, pre-built CMMS Integrations with the most widely used software systems. That means no help from a developer or your IT team is required. Learn more about our integrations.
How secure is the Limble CMMS platform?
At Limble, our world-class data security practices ensure your account information is safe. We use state-of-the-art technologies and industry best practices to maintain a secure infrastructure, including SOC-II Type II certification, regular penetration testing, and continuous security training for our staff.