CMMS software is helping maintenance teams collect real-time insights and use their data to transform their operating procedures.
Whatever your industry, managing a world-class maintenance department means collecting, managing, and analyzing massive amounts of data. High-quality, granular, up-to-date insights help maintenance teams assess their performance and make positive changes to their asset management strategies. Thorough data collection, management, and analysis can provide benefits including:
- Extending the lifecycle of critical assets thanks to more proactive maintenance work
- Speeding the transition away from an emphasis corrective maintenance to a preventive maintenance strategy
- Reducing the likelihood of unexpected breakdowns and the maintenance costs associated with all types of downtime
- Simplifying auditing by ensuring crucial information is always at the ready
- Increasing the profitability of the maintenance department’s efforts by offering insights into the cost effectiveness of specific decisions
Though spreadsheets may have done the job in the past, organizations are increasingly evolving their maintenance management and data analysis efforts. For more and more teams, Computerized Maintenance Management Systems (CMMS) are supporting world-class maintenance operations.
Our recent survey of maintenance pros found that 78% of respondents are leveraging preventive maintenance strategies to address downtime. CMMS tools are likely playing a role in the development and long-term management of these strategies.
What is maintenance data?
Maintenance data includes any data point used to manage your physical assets and infrastructure. The primary reason to collect all this data and analyze it closely is to help your maintenance team make more informed decisions to execute their work more safely, efficiently, and cost effectively.
There is no “right way” to categorize maintenance data. For our purposes, we’ll group maintenance data into three unique categories:
- Machine data
- Operational data
- Management data
Free CMMS Buyer's Guide
Discover everything you need to know about CMMS in this comprehensive guide. Begin your maintenance journey now!
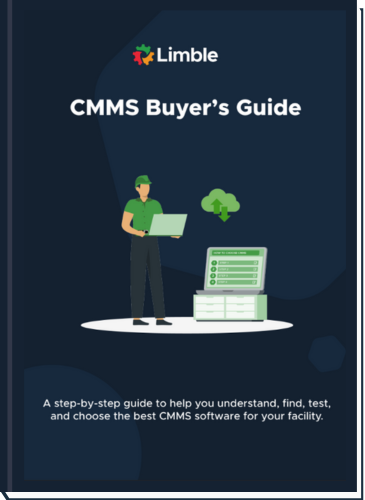
Machine data
With the help of tactics like routine inspection and maintenance software like condition-monitoring sensors and IoT-enabled systems, you can collect and analyze data on asset performance. You can use this data to predict faults, tailor maintenance schedules, and make data-driven decisions about repairs and replacements.
Some machine data points you can collect, track, and gain insights from include:
- Machine speed
- Temperature data for various components
- Torque
- Vibration levels
- Energy consumption
- Output
- Product quality
Spotting data anomalies early can help you proactively address potential problems and consequences like costly downtime. The specific data points you collect and your methods for putting data to work will depend on the maintenance strategies your organization leverages. If you’ve implemented a predictive maintenance or prescriptive maintenance program, performance data is especially important for ensuring you can schedule maintenance work right on time.
Effective maintenance planning and scheduling requires close attention to various types of data.
Operational maintenance data
Maintenance planners, supervisors, managers, and technicians use operational maintenance data to schedule and execute their tasks. You can collect these data points from sources including:
- Historical records of maintenance activities
- Documents related to work requests, work orders, spare parts and tools availability, technician workload, and team or technician performance.
- Asset tracking data
- Machine manuals, policies, safety guidelines, procedures, and checklists.
Some organizations draw a clear distinction between maintenance documentation and maintenance data.
Management-level maintenance data
Management-level maintenance data provides an overview of machinery, facility, and team performance. Common examples of management-level data points include:
- Performance against maintenance Key Performance Indicators (KPIs)
- Machine downtime, uptime, availability, and reliability metrics such as MTBF and MTTF
- Operational efficiency metrics such as MTTR and PMP
- Labor costs including overtime
- Spare parts inventory costs
- Total operational costs
These maintenance metrics are among the most useful data points for maintenance professionals looking to prepare budgets, improve performance, cut costs, and make other important strategic decisions.
Why is maintenance data management important?
The data maintenance teams have at their disposal plays an important role across all of their operations. Here are some examples of high-quality maintenance data in action:
- By assessing the number of work orders and the types of work orders associated with specific assets, you can determine if you’re performing maintenance tasks too often or too irregularly. For example, assets associated with huge numbers of emergency work orders may require more frequent attention than they’re getting. On the other hand, if an asset has very few corrective work orders associated with it, it’s possible you are doing more maintenance work than you need to.
- A close look at planned and unplanned downtime can help you learn which assets are most critical to your operations and most likely to cause costly disruptions. Once you’ve identified the assets experiencing the most unplanned downtime, you can find the most costly and make these assets your priority. Assessing emergency work orders can point to the most common causes of trouble and lead you to process improvements.
- Analyzing emergency work orders can help you optimize spare parts inventory management to ensure the tools you need most often are always stocked and easily accessible. Kitting essential parts together will ensure your team can quickly and efficiently carry out maintenance tasks, ultimately lowering MTTR.
- Diving into labor costs can help you determine whether it would be more cost effective to bring new full-time employees abroad or outsource additional maintenance work to contractors.
- Identifying trends in your work order completion notes can help you proactively identify technicians who are struggling or common obstacles that are affecting your team as a whole.
We could provide hundreds of additional examples. Accurate, accessible, granular data is useful for everything from planning spare parts orders to scheduling tasks and beyond.
Your maintenance team aren’t the only employees who’ll benefit from better data management. Any business function that collaborates with your maintenance department will potentially benefit from managers, operators, and technicians who can make more informed, data-driven decisions. Data analysis could also pave the way for the maintenance department to distinguish itself as a valued strategic ally rather than a tactical cost center.
Check out this video introduction to Limble’s reporting features.
How can a CMMS improve maintenance data management?
With useful templates, tools for automation, dashboards for data management and more, cloud-based CMMS software is becoming an integral part of modern maintenance and facilities management. Here are just a few of the ways CMMS tools are supporting the evolution of the maintenance function.
Explore our free maintenance templates & resource library
Simplified data storage and accessibility
CMMS solutions like Limble provide a digital, centralized platform to story all of your maintenance data and streamline analysis. You can access essential data from anywhere with just a few clicks, even from a mobile device. Role-based access controls can help organizations ensure every team member only has access to the information they need and that sensitive data is protected.
Automated data collection
When you introduce a new asset, part, or vendor to your operations, you can manually add the relevant data to your CMMS. The real value of a CMMS, however, comes from its automated data collection capabilities.
Imagine a work request comes in. You approve a new work order for the task, assign it to a technician, and schedule the work for completion. Once the technician has completed the task, they’ll submit the appropriate documents for your review.
Throughout this process, your CMMS will collect the following relevant information:
- Who submitted the work order?
- When was the work order submitted?
- What is the problem?
- How urgent is the problem?
- What is the cost of failing to complete the task in a timely manner?
- Who performed the work?
- How long did it take your technician to complete the work?
- Which materials and spare parts were necessary for completing the task?
- When was the work completed?
- Was your technician able to meet your requirements?
Upon completion of maintenance work, your CMMS will automatically update the maintenance history for the asset or system in question. It will also update your spare parts inventory count accordingly.
That’s a lot of maintenance data – data you can use to improve internal processes and make your maintenance more as cost effective and impactful as possible.
In-depth data analytics
Access to the right data is essential for delivering on maintenance goals like eliminating unplanned machine downtime, reducing labor costs, and improving the performance, reliability, and availability of critical assets.
The rigorous analysis enabled by CMMS tools can help uncover valuable insights that may not be readily apparent at a glance. A CMMS platform will simplify data analysis by:
- Keeping maintenance records up to date
- Enabling you to set KPIs and track relevant metrics
- Generating periodic reports based on the templates you’ve established
- Providing access to real-time condition-monitoring data
- Forecasting your MRO & spare parts inventory needs
- Making it simpler to conduct root cause analyses and trace problems to their sources
Check out this demonstration of how easy it is to build and customize your dashboards in Limble CMMS.
Limble’s custom dashboards are an essential feature for modern maintenance teams.
Optimize maintenance data management today
With a centralized, cloud-based CMMS platform like Limble, you can seamlessly generate, store and access all of your maintenance data. Request a demo today to learn more about transforming maintenance data management.