Ever since the first industrial revolution, in one form or the other, improving equipment reliability has been the core subject of interest for reliability engineers and maintenance professionals alike.
Designing highly reliable equipment requires subject matter knowledge of the concepts of reliability, working principles of the equipment under consideration, levels of desired performance, and the context of the operation where the equipment is intended to operate in.
Below are seven ways equipment reliability can be improved at the design and operational phases.
1) Improve data quality
The presence of high-quality data represents the single most important thing to have at any stage of the asset lifecycle.
Oftentimes, the equipment failure and maintenance data is either not available or it is contaminated with errors and biases. This lack of quality data leads to reliability engineers judging equipment performance based solely on their experience – resulting in decision-making that is not able to squeeze the maximum value out of the available assets.
The best way to ensure data quality is to simplify, standardize, and automate equipment data collection and reporting.
All of that can be done by implementing a mobile-enabled CMMS app like Limble. It serves as your centralized data repository with instant access to maintenance information like:
- Who has performed what, when, and for how long
- An overview of all work requests
- List of tools and parts used during the repair process
- Detailed equipment maintenance log with technicians’ notes for each asset (which can be used to identify common problems and failure modes)
- Costs associated with each part, asset, vendor, and contractor
- Various maintenance metrics and KPIs you set up and decide to track (for example, Limble automatically calculates metrics such as MTBF, MTTR downtime, etc.)
Reliability and maintenance engineers can use this granular information to improve future equipment/component designs and develop maintenance strategies and schedules that address the most problematic failure modes.
2) Rank assets based on criticality
An industrial facility can feature hundreds or even thousands of equipment pieces. Performing reliability analysis for each one is neither feasible nor cost-effective.
The equipment has to be prioritized based on some criticality score. The most common approach is to perform Failure Mode Effect and Criticality Analysis, which can be used to rank assets based on the severity of the impact of their failures on the overall operation.
For example, you will not spend the same amount of resources on tracking the condition of the traction converter for the locomotive versus the small manual transfer switch installed on the same locomotive.
As pointed above, the presence of quality data plays a crucial role in performing criticality analysis.
Some of the components which may look non-critical at first sight can have a significant impact on the overall plant reliability. A detailed level of impact and criticality can only be understood if the component level breakdown information is available.
3) Improve the effectiveness of maintenance work
The quality of performed maintenance work on an asset will have a direct impact on its reliability.
There are many ways to improve the quality of executed maintenance work:
- Ensure that maintenance techs and mechanics are properly trained and have access to the right maintenance tools
- Implement condition monitoring sensors, non-destructive testing, and predictive maintenance
- Use SOPs and maintenance checklists to standardize maintenance work according to best practices
- Use a CMMS system to set up maintenance schedules (and stick to them!)
- Use CMMS and other analytics to gather and analyze data and improve upon every point mentioned above
Getting all of this right will reduce the occurrence of unexpected downtime, as well as unnecessary planned downtimes and thus improve the overall levels of reliability and equipment availability on your plant floor.
4) Develop metrics that track reliability
It is hard to improve something you do not measure. Use metrics like MTBF, MTTF, MTTR, and availability to estimate and improve the reliability of critical equipment.
In some cases, critical equipment comes with sensors that provide a real-time overview of equipment performance and health. With these sensors, the equipment time of operation can be automatically logged – along with the time and frequency of failures.
The real-time display of reliability measures provides situational awareness to the equipment operator and enables proactive corrective actions. This reduces the probability of failure and initiates intervention before the equipment reaches complete failure, thus prolonging the P-F interval and equipment reliability.
5) Increase equipment redundancy
One of the methods to improve the reliability of any system is to introduce redundancies that eliminate single points of failure.
Take an oil refining facility as an example. If the facility has only one specific mainline crude oil pump, it has to continuously operate to ensure the sustained operation of that facility. If it fails, the entire plant has to be shut down.
With the use of redundancy, a plant operator can eliminate this scenario. They can install a similar-sized pump as a standby that can automatically take the load if the other one fails.
It is a proven way to improve reliability, albeit a fairly expensive one. The investment is justified in capital-intensive industries where the impact of equipment failure on overall plant reliability is enormous.
The same principle can be applied while designing parts and equipment. Engineers can use redundancies to address specific failure modes and create more fault-tolerant systems.
6) Improve training and skills of equipment operators
Improving the knowledge and skill of equipment operators and other people that come in contact with the equipment is among the most cost-effective and easy ways to improve equipment reliability.
Most of the machines operated in industrial settings have to interact with humans in one way or another. No matter how sophisticated the controls for tracking machine health are, if the operators are not properly trained, the equipment is bound to experience frequent failures.
There are several ways to minimize the chances of human errors and minimize their impact on equipment reliability both at the design as well as operational stages.
At the design stage, reliability engineers can work with ergonomic consultants to simplify the design from a human perspective. In other words, to balance equipment efficiency with its ease of use and maintainability.
Once the human factors are incorporated in the designs, the next phase is often to make sure that operators get proper training and education.
The error-free operation of the equipment and its effective and quick troubleshooting produce a direct impact on reliability by reducing unscheduled downtimes and other unpleasant surprises. As such, they should be one of the building blocks of a solid asset management program.
7) Improve the reliability culture
Most maintenance and plant managers should already know the importance of equipment reliability. This is because they have a broader understanding of the cash flows and profits that equipment is generating for them.
The bottom-line workers, on the other hand, often fail to realize why it is such a big deal for management when equipment that was failing once every six months has all of the sudden started to fail once every four months. The workers may see this change as insignificant.
You need to educate people at all levels of the organization about the importance of asset reliability. It is the only way to foster a culture of reliability and continuous improvement. Ideally, every person of the organization should have a clear understanding of how a machine they operate is contributing to achieving the overarching business objectives.
The Essential Guide to CMMS
The Essential Guide to CMMS
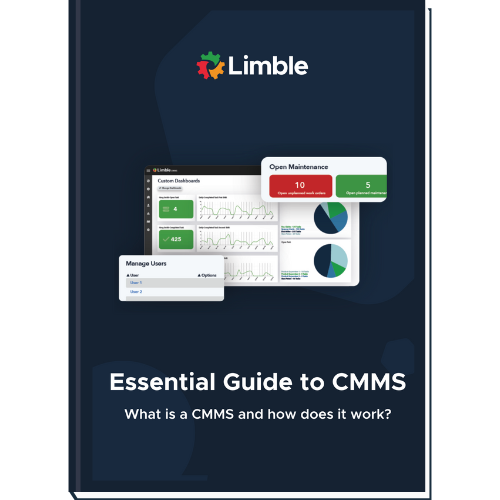
Equipment reliability is a team effort
Asset reliability can’t be the responsibility of reliability engineers alone. Every stakeholder, be it a designer, reliability engineer, maintenance mechanic, or equipment operator, has an impact on the reliability of the equipment they are responsible for.
Effective organizations that excel in reliability recognize this and make sure that each stakeholder has the right tools and knowledge to do their job to the best of their abilities.
Start your reliability journey today by implementing Limble CMMS. It will offer you unprecedented access to the data you need to establish strong maintenance and reliability programs.
Comments are closed.