In the field of maintenance, the phrase, “If it ain’t broke, don’t fix it” definitely does NOT apply. Waiting until something breaks can result in catastrophic costs. But a little preventive maintenance goes a long way.
We’ll share all the benefits of preventive maintenance – and there are many – to ensure you make the most of it.
What is preventive maintenance?
Preventive or preventative maintenance is a proactive way of organizing maintenance work on machinery, facilities, or equipment in order to prevent them from malfunctioning, or otherwise requiring repair.
Types of preventive maintenance
Because this type of maintenance is proactive (i.e. it must occur without the trigger of a breakdown or repair), maintenance teams use different kinds of approaches to know when to perform them.
- Time-based maintenance is when teams schedule maintenance based on the passage of time such as checking the oil in a vehicle every three months or performing inspections weekly.
- Usage-based maintenance is when teams schedule maintenance based on the use of an asset since it was last serviced or inspected, such as the lubrication of a pump after 500 operating hours.
- Condition-based maintenance is performed when an asset’s condition, as noted by a sensor or other condition data, indicates that maintenance is required, such as refilling a tire once a pressure reading falls below a set threshold.
These parameters are typically defined by manufacturer recommendations in OEM manuals, patterns in an asset’s maintenance history, and the expertise of your team.
Free Preventive Maintenance Plan Template!
Following a consistent Preventive Maintenance Plan can make life easier. Use this template to create your own.
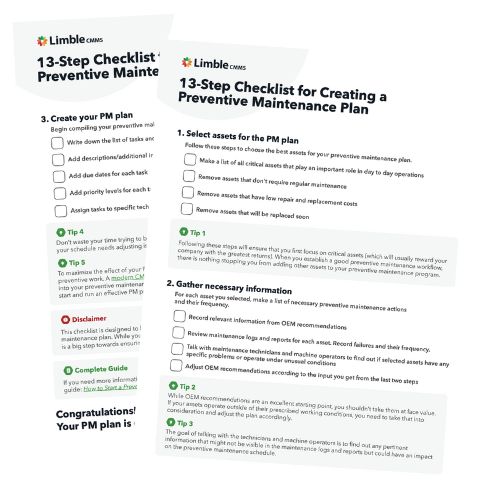
Benefits of preventive maintenance
You have probably been told that preventive maintenance is the answer for a number of maintenance woes. Let’s break down the details of the preventive maintenance benefits most companies experience.
Lower risk of breakdowns and downtime
Downtime stops productivity altogether. By reducing the likelihood of breakdowns, malfunctions, and lengthy repairs, preventive maintenance is the single most effective way to avoid it.
Preventive maintenance helps organizations reduce unplanned downtime by:
- Allowing repairs to be done more quickly thanks to customized and well-researched preventive maintenance protocols
- Improving equipment reliability, keeping assets in top working order
- Avoiding maintenance during important productive time on the plant floor
Longer equipment lifespan
Every piece of equipment eventually runs its course, requiring either repair or replacement. However, preventive maintenance can go a long way toward delaying the inevitable.
Here are some ways preventive maintenance prolongs asset health and overall equipment life:
- Improves detection of minor faults that can escalate to bigger issues
- Enables machines to run cleaner, requiring fewer recalibrations
- Improves calculation of asset depreciation, enabling better procurement decisions
- Reduces wear and tear caused by breakdowns
Increased efficiency
Preventive maintenance improves an organization’s efficiency from almost every angle. Whether it is human resources, materials, energy, or time, proactively keeping your assets in top working order is a huge driver of efficiency.
Furthermore, companies now have the option of preventive maintenance software. These systems provide checklists for common maintenance activities, and automation of many administrative functions that come with running a PM program.
Better workplace safety
When assets are well taken care of, they are safer to use and run less of a risk for accidents. With preventive maintenance, teams also have the time and foresight to perform maintenance activities properly, in accordance with regulations, and with appropriate precautions. All of this helps ensure a safer workplace and more productive environment for everyone.
Financial benefits
All of the other benefits of preventive maintenance translate into an improved financial picture for the company. In addition to cutting down on waste, avoiding repair costs, prolonging asset life, reducing downtime, and lowering safety risk, preventive maintenance also paves the way for greater efficiency right within the maintenance department.
By spending more time on smaller maintenance tasks and less time on lengthy repairs, maintenance costs go down. That trend accelerates when companies take the next step to implement predictive maintenance and other more advanced preventive maintenance strategies.
Improved customer satisfaction
Less unexpected downtime means fewer delays in production, improved product quality, and – because of the cost savings mentioned above – a better price point. All of these things lead to better customer satisfaction and an improved brand reputation.
Less emergency maintenance work
Emergency maintenance is the most expensive and the most dreaded form of maintenance, especially for companies running high-value production equipment.
Routine maintenance insulates an organization from these issues with the added benefit of avoiding overtime and the need to divert resources from other asset management activities.
- Proactive maintenance scheduling allows for easier planning and procurement of parts and inventory needs
- PM inspections identify and resolve potential failures that could otherwise lead to breakdowns requiring emergency repair
- “Always on” systems such as elevators, ventilation, and HVAC have improved reliability
- Static cosmetic fixtures have improved service life and quality
Disadvantages of preventive maintenance
The good must be taken with the bad. As beneficial as preventive maintenance is for many organizations, there are disadvantages to consider as well. Here are some of the most commonly cited hesitations to moving toward a proactive approach.
Potential for over-maintenance
This is one of the primary disadvantages of preventive maintenance. It is important to regularly take a critical eye to your PM plan. If you are experiencing zero equipment failures, you may have room to loosen the parameters and spread out your PM activities and maintenance technicians.
Other solutions include the addition of sensors that measure an asset’s working condition to trigger maintenance. Data compiled by a Computerized Maintenance Management System (CMMS) can also be used to detect patterns that can help more precisely plan regular inspections at appropriate intervals.
Spending resources where they aren’t needed
Some assets simply don’t rise to the level of criticality where a preventive maintenance program is worth the effort. Weighing the contributions an asset makes to operational efficiency against the cost of performing regular maintenance is a good place to strike the right balance.
It can be a tricky balance to get right, but the most effective maintenance programs use many different approaches to maintenance strategically.
Watch out for these common preventive maintenance mistakes
Without making the effort to avoid these common mistakes, your preventive maintenance program may not be as effective as it could be.
- Not leveraging team expertise: Your team knows your equipment best. Don’t forget to include technician input in your preventive maintenance plan before putting it into place.
- Not clearly defining maintenance procedures.: Preventive maintenance tasks are performed routinely and as a result, should follow the same steps every time.
- Not re-evaluating PM plans over time: Taking a continuous improvement approach will help you learn more about what works and what doesn’t. Experimenting with timeframes and triggers for routine maintenance can help strike the right balance between too much, and just enough maintenance.
Tips for getting preventive maintenance right
It is easy for preventive tasks to be deferred when other more time-sensitive problems emerge. Follow these tips to make sure preventive maintenance gets done, and gets done well.
- Take asset criticality into account: Not all assets are created equal. Perform a criticality analysis and focus your efforts, resources, and skills on the pieces of equipment that are most critical to your success.
- Strategically leverage the skills on your team: Preventive maintenance provides the opportunity to be planful. Take advantage of that opportunity by assigning tasks to the technicians with the best skillset for the job.
- Strategically schedule maintenance tasks: Proactively scheduled maintenance can ensure tasks are performed at times when they provide the least disruption to the organization.
- Create accountability for preventive tasks: Ensure preventive tasks are worked into daily schedules and reports to hold team members accountable.
- Use the right tools to coordinate PMs: Using a CMMS to coordinate your preventive maintenance program eases the burden of administration, allowing resources to focus on the maintenance tasks themselves.
Free CMMS Buyer's Guide
Discover everything you need to know about CMMS in this comprehensive guide. Begin your maintenance journey now!
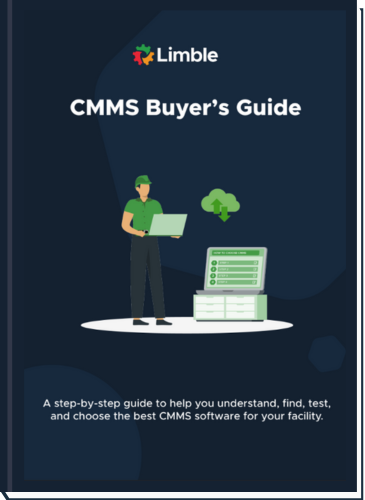
Get expert engineers to develop PM plans
The maintenance managers and crew who work with your equipment regularly know those assets better than anyone. They should be the subject matter experts who help create and customize your PM plans.
Developing expert-backed PM plans has several benefits, including:
- Highly detailed insights on regular tasks
- More cost-effective preventive maintenance programs
- Fewer parts and tools needed for preventive maintenance tasks
- Low-redundancy plans that efficiently allocate PM resources
- Greater customization compared to PM stock plans
Leverage historical data and machine learning
Sometimes looking to the future means we first have to look at our past. Developing a preventative maintenance plan based on maintenance histories will improve a company’s chances of eliminating resource waste.
By tracking all maintenance tasks and finding patterns and ideal maintenance intervals you can determine which practices will help streamline your maintenance in the future. Analyzing long-term data offers several benefits to the PM framework. These include:
- The ideal basis for a predictive maintenance strategy
- More precise resource allocation for every job
- Knowledge of maintenance parts, quality, and inventory needs
- Shorter troubleshooting and issue identification which reduces downtime
Prioritize tasks categorically
Most PM plans apply a one-size-fits-all approach to equipment maintenance. This means that some of the more valuable and complicated machinery get the same level of priority as other assets. Prioritizing and performing the most critical tasks first will make the biggest impact on your operations and maintenance goals.
Here are some of the advantages of categorically prioritized maintenance:
- Increases the life of high-value machinery
- Enables skill-based assignment of maintenance tasks, ensuring the right people are on the job
- Prevents resource allocation to lower priority machinery
- Saves time on individual service sessions
- Allows for a smoother maintenance framework for newer companies
Final thoughts
While it may be tempting to rely on reactive maintenance, you will be better off investing the time to create and use a preventive maintenance plan. Not only will you improve the bottom line, but you will also reduce your overall downtime, increase the lifespan of assets, and decrease waste.
And by sticking close to these best practices like utilizing a CMMS system, your program will begin to see results in no time.
See for yourself what Limble can do for you, schedule a quick product demo or start a free trial.