The best way to extend the useful life of your assets and facilities is by building a strong maintenance culture in your organization.
You need to care for your maintenance personnel as much as for your equipment – they too experience wear and tear and can become careless and unmotivated. Maintenance culture helps you to develop skills, tenacity, and diligence.
A McKinsey report highlights that strong leadership and maintaining the energy for change among employees are two principles of success that reinforce each other when executed well. And we know how change management is important to build a proactive maintenance culture.
But before we discuss how, we need to understand the meaning behind the phrase “maintenance culture”.
What is maintenance culture?
Maintenance culture entails the company’s values, way of thinking, behavior, perception, and the underlying assumptions that guide their daily maintenance actions and practices.
Broadly speaking, there are at least 10 factors that will impact the maintenance culture at any organization:
- Leadership
- Communication
- Motivation
- Recognition and reward systems
- Empowerment
- Involvement
- Policies, strategy and work planning
- Teamwork
- Training and education
- Overall organizational culture
An organization needs to have a proactive maintenance culture if it wants to create a safe and productive work environment.
The Essential Guide to CMMS
The Essential Guide to CMMS
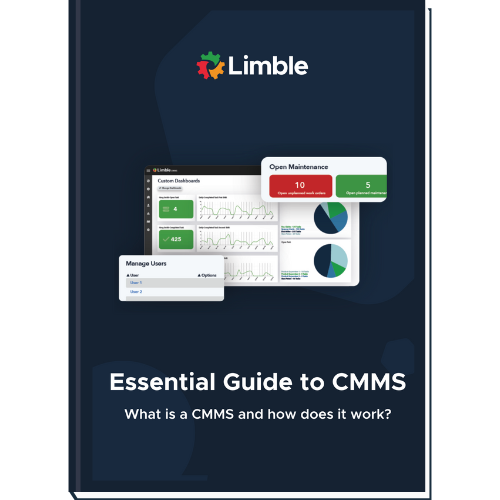
How to build and imbue maintenance culture in your organization
Getting your maintenance personnel on the same page, and making sure everyone holds the same values and attitudes towards maintenance work and equipment can be harder than you think, especially if you have to coordinate more than one team.
Here are the steps you can follow that will get you closer to that ideal.
1. Onboard the right professionals
Employees are a company’s most valuable asset in any organization. But this can only be true when you hire the right people. Incompetent or poorly suited personnel in maintenance positions will bring about significant operational and cultural problems.
To create a successful maintenance culture, onboard the right professionals that inspire, guide, and bring clarity to the maintenance and growth of the company.
2. Invest in training and people management
Maintenance thrives with technical knowledge. In a market where new maintenance talent is hard to find, it is worth looking at people with less experience but with the right attitude. With proper onboarding and maintenance training programs, you can get them to the level they need to be fairly quickly.
Building a uniform work environment governed by technical know-how and people management is crucial. This will remove the guesswork from hundreds of maintenance chores that must be completed regularly and help you maintain a consistent level of quality when it comes to performing maintenance work.
3. Optimize your internal resources and scheduling
It is hard to care about the quality of your work if the organization doesn’t even bother to provide you with the resources you need to do your job properly.
Maintenance supervisors/planners should make sure that each technician has access to the right maintenance tools and spare parts, as well as enough time to complete all assigned tasks.
The easiest way to do that is to employ a CMMS software as its main use is to help you track and organize maintenance work at your facility.
4. Develop and track relevant maintenance KPIs
Maintenance culture is not something that can be described with a single key performance indicator (KPI). Still, KPIs are a great way to track and measure whether your maintenance department is moving towards set goals.
By keeping an eye on maintenance KPIs and metrics (like Mean Time To Repair, Mean Time Between Failures, and the volume of planned vs unplanned work), you can assess the organization’s current maintenance arrangements and subsequently describe where you need to make improvements.
Improvements in maintenance culture will often be reflected in improvements of the aforementioned metrics. When workers can directly correlate their effort with the improved numbers, you will have less trouble getting everyone to follow your maintenance principles and procedures.
5. Leverage recent technology and tools
Newer technologies – such as Artificial Intelligence, Machine Learning, and the Internet of Things – are gradually overtaking the realm of machine maintenance.
For instance, you can create a system to scrap machine data like working time, steady states, routine maintenance, and oil use through various condition monitoring sensors and non-destructive tests. You can also push that data through predictive analytics to spot anomalies in your operation and detect equipment issues in their infancy.
Having access to such technology helps you optimize your internal resources, but more importantly, it makes your daily life easier. And it is much easier to strive for higher values and continuous improvement when your whole day doesn’t consist of running around a facility, putting out fires.
6. Define policies and procedure
The essence of your maintenance culture will often be outlined in your maintenance policies. If you do not have one, it is as good of a time as any to write a maintenance policy and communicate the maintenance mission, vision, goals, and responsibilities with all stakeholders. That way, each person knows what they’re expected to do and why.
Great supporting documents to your maintenance policy are Standard Operating Procedures and maintenance checklists. They both help with the standardization of maintenance work according to best practices.
Start improving your maintenance culture today
A strong, proactive maintenance culture will result in well-maintained equipment that works and serves the purpose it’s made for. Reliable equipment that rarely fails means that both technicians and operators will be faced with less stress. As a result, they will be able to channel the necessary energy into more productive areas.
Your company will be capable of tapping into other bits of the value chain and adopting high-level operations that primarily bring about profits. In the end, this will strengthen your competitive strategy and market share.
Author: Owen McGab Enaohwo is the CEO and Co-Founder of SweetProcess, an easy-to-use and intuitive business process management software founded in 2013. The software makes it possible for company executives and their employees to collaborate and document standard operating procedures, processes, and policies.