Asset Utilization
Everything you ever needed to know about asset utilization.
What is asset utilization?
In business, asset utilization is a ratio that measures how efficient an organization is in using the assets at its disposal to turn a profit. In manufacturing facilities, it measures how well organizations use their installed production capacity.
To calculate asset utilization for any piece of equipment, you have to take into account two different factors – its potential utilization and its actual utilization. Remember, there is a hard limit to the number of hours you can work even the most powerful machine in a given year: 8760 hours. Calculating Total Effective Equipment Performance (TEEP) is a way of assessing the productivity of equipment and systems with respect to the full calendar year.
Even when potential utilization is 100%, numerous factors can come into play and keep organizations from using assets to their full capacity.
These include:
- Mandatory downtime
- Changeover and operator breaks
- Scheduled downtime for maintenance and repairs
- Rest periods
- Holidays
- Unexpected equipment failure
- Other routine and unexpected events
Calculating asset utilization allows you to take all of these factors into account and measure the actual use of total assets. It is a key metric that can reveal a lot about the efficiency of your business and support you in delivering on your KPIs.
Higher asset utilization usually translates into increased overall efficiency and better profit margins. Businesses with high asset utilization rates have typically optimized their processes, effectively deployed preventive maintenance strategies, and established cultures of continuous improvement. Digging into low asset utilization figures can identify opportunities to streamline operations.
Table of Contents
Why should you calculate your asset utilization ratio?
The asset utilization metric is important for accurately gauging business performance. Low asset utilization could indicate excess production capacity or other inefficiencies affecting uptime.
Calculating asset utilization is more useful than calculating overall equipment effectiveness (OEE) alone for several reasons. For one, OEE only focuses on the production process. Poor asset utilization, however, is often caused by other factors that are independent of production. For example, low sales can lead to inventory pile-up. This could force you to reduce production, ultimately affecting asset utilization.
It is best to combine both of these metrics. You should first measure OEE and then use it in your asset utilization calculations. Ideally, asset utilization should stay above 70%. Anything lower, and the impact on unit cost is too high and can cause your business to fall behind the competition.
The key metrics involved in the calculation of asset utilization
Four primary metrics are used to calculate asset utilization ratio.
1) Product yield
Production processes can’t deliver 100% flawless output all the time. Some number of units in a given batch may suffer from defects that render them unfit for sale. Product yield is the ratio of good units available in a batch compared to the total units produced.
2) Overall equipment effectiveness (OEE)
When it comes to plant productivity, OEE is widely considered one of the gold standard metrics. It looks at quality, performance, and availability to paint a comprehensive picture of actual productivity and effectiveness. OEE calculation is done by multiplying the three factors:
1. Quality: How many defects were produced?
Quality = Good parts / total products produced
2. Performance: How did the asset’s performance compare to its maximum potential?
Performance = (Ideal cycle time x ideal products produced) / actual throughput
3. Availability: How did the asset’s uptime compare to its total available production time?
Availability = Runtime / planned production time
In lean manufacturing and maintenance, OEE is a key metric for identifying and eliminating sources of waste. A low OEE score could be a sign of poor maintenance, inefficient production, or an overall lack of adequate planning..
Check out a quick video guide to calculating OEE.
3) Unplanned downtime
Unplanned downtime occurs when an asset shuts down due to malfunctions or breakdowns and the resulting emergency maintenance. It may also occur due to a shortage of parts or stock-outs.
More often than not, high levels of unplanned downtime are signs of inadequate or ineffective maintenance management, inventory management, and maintenance team training.
4) Maintenance spend
As an asset reaches the end of its lifecycle, it may require more frequent and more costly maintenance. A piece of equipment may be especially inefficient or outdated if it accounts for an especially high ratio of your overall maintenance spend. It may be time to gradually phase the asset out, invest in more extensive repairs, or replace it as soon as possible.
8 Steps to asset utilization calculation
Measuring asset utilization is straightforward. You start with the maximum total number of hours an asset could be used and you subtract all the time it was not in use.
The primary challenge in calculating asset utilization is obtaining accurate data for the calculation.
To calculate actual asset utilization, follow the steps outlined below.
- Determine annual planned downtime: Find the annual figure for planned maintenance downtime for all of your production-related assets. Calculate the total average across all assets to figure out the actual maintenance downtime for a plant or facility
- Add lost operations time: Find the total number of operational hours lost each year due to holidays and other sources of operational downtime.
- Include production hours lost due to low sales/backlog: Calculate the hours lost due to forced underutilization of assets. Factors to consider include reduced sales, loss of market share to competitors, seasonal variations in demand, downtime caused by trials, innovations, or changes in plans/schedules driven by business decisions.
- Calculate the total losses related to a strategic plan: Add all the figures from steps 1 through 3 to calculate the total asset utilization losses that cannot be attributed to operations or production processes. These factors are typically not under your control.
- Account for unscheduled downtime: Take into account the total number of hours of unplanned downtime your assets experienced.
- Look at quality losses: Calculate your product yield and convert defective units into lost production time.
- Include production rate losses: When assets are operating below their peak capacity, you should log this in terms of losses in operation time. You should calculate this figure by following the same steps you followed to calculate quality losses. If, for example, an engraving machine was rated for 10,000 units per hour but only produced 5000, you would convert the 50% output reduction to a 50% reduction in operating time.
- Calculate actual asset utilization: To arrive at the final figure, subtract all those losses from 8,760 – the total number of hours in a year. Multiply this number by 100 and you’ll have your actual asset utilization ratio.
How do you optimize asset utilization?
Once you gain insights into the actual state of asset utilization in your organization/individual facilities, you can begin making more informed decisions to take the appropriate corrective action.
If your utilization figures are too low, there are several optimization tactics and strategies to help you make more effective, productive use of your critical equipment.
- Aggressively investigate all asset failures to determine their root causes.
- Track MTBF to determine which assets have reliability issues.
- Provide adequate training for maintenance teams and machine operators to prevent downtime as a result of human error.
- Refine your spare part management, MRO management, and tooling management processes.
- Buy only reliable, high-quality equipment and replacement parts that are designed with fault tolerance in mind.
- Transition from reactive maintenance to a proactive and/or predictive maintenance strategy.
- Improve maintenance scheduling by using a customized CMMS solution.
Want to see Limble in action? Get started for free today!
Get the most from your assets and optimize maintenance costs
A modern CMMS system can go a long way in making the process of calculating and optimizing asset utilization easier. When used properly, a CMMS can automatically track planned and unplanned downtime for specific assets or facilities. Check out our guide to learn more about how a CMMS can help you optimize asset management.
The Essential Guide to CMMS
Download this helpful guide to everything a CMMS has to offer.
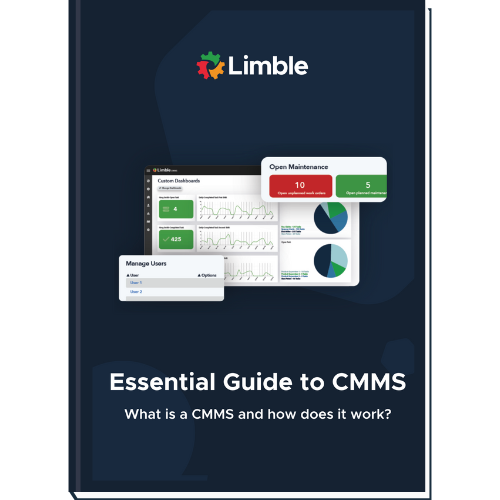
FAQ
Why use CMMS software to track maintenance metrics?
Using CMMS software simplifies tracking complex maintenance metrics, fosters data-driven decisions, enhancing efficiency, reducing downtime, and aiding in regulatory compliance all in one.
Table of Contents
- Everything you ever needed to know about asset utilization.
- What is asset utilization?
- Why should you calculate your asset utilization ratio?
- The key metrics involved in the calculation of asset utilization
- 8 Steps to asset utilization calculation
- How do you optimize asset utilization?
- Get the most from your assets and optimize maintenance costs
- The Essential Guide to CMMS
- FAQ
- Related Content
Is Limble Mobile CMMS app user friendly?
Limble is consistently rated Easiest-to-Use CMMS on review sites like G2, Capterra, and Software Advice. And our customers agree. With our mobile CMMS app, teams experience 30%+ better productivity, on average, requiring little to no training or ramp-up time. Our CMMS app can travel with your team, no matter where they go! Visit our App Store or Google Play for more information.
Table of Contents
- Everything you ever needed to know about asset utilization.
- What is asset utilization?
- Why should you calculate your asset utilization ratio?
- The key metrics involved in the calculation of asset utilization
- 8 Steps to asset utilization calculation
- How do you optimize asset utilization?
- Get the most from your assets and optimize maintenance costs
- The Essential Guide to CMMS
- FAQ
- Related Content
Can I connect to other systems?
Limble provides seamless, pre-built CMMS Integrations with the most widely used software systems. That means no help from a developer or your IT team is required. Learn more about our integrations.
Table of Contents
- Everything you ever needed to know about asset utilization.
- What is asset utilization?
- Why should you calculate your asset utilization ratio?
- The key metrics involved in the calculation of asset utilization
- 8 Steps to asset utilization calculation
- How do you optimize asset utilization?
- Get the most from your assets and optimize maintenance costs
- The Essential Guide to CMMS
- FAQ
- Related Content
How secure is the Limble CMMS platform?
At Limble, our world-class data security practices ensure your account information is safe. We use state-of-the-art technologies and industry best practices to maintain a secure infrastructure, including SOC-II Type II certification, regular penetration testing, and continuous security training for our staff.
Table of Contents
- Everything you ever needed to know about asset utilization.
- What is asset utilization?
- Why should you calculate your asset utilization ratio?
- The key metrics involved in the calculation of asset utilization
- 8 Steps to asset utilization calculation
- How do you optimize asset utilization?
- Get the most from your assets and optimize maintenance costs
- The Essential Guide to CMMS
- FAQ
- Related Content