Most asset management strategies include both preventive and corrective maintenance. However, many maintenance managers fail to move beyond preventive maintenance into the world of predictive maintenance.
While there is some additional up front investment required to implement PdM, the benefits are numerous. We’ll share the most significant benefits of predictive maintenance that make it worth the effort.
What is Predictive Maintenance?
The goal of predictive maintenance is to collect and analyze asset condition data in order to identify patterns and algorithms that can predict when failures may occur. This allows maintenance teams to monitor assets to look for conditions that may indicate a failure so maintenance can be performed to prevent it.
An effective predictive maintenance plan is best applied to assets that are more prone to have a failure due to a specific condition or circumstance and that have a major impact on business operations. This means that asset condition is detected and the maintenance is performed just before a breakdown or failure happens in order to avoid its negative impacts.
Predictive maintenance schedules are associated with big cost savings related to the avoidance of machine downtime. Companies that invest in PdM reduce up to 30% of maintenance costs and significantly increase return on investment.
Checklist for Creating a Preventive Maintenance Plan
Following a consistent Preventive Maintenance Plan can make life easier. Use this checklist to create your own!
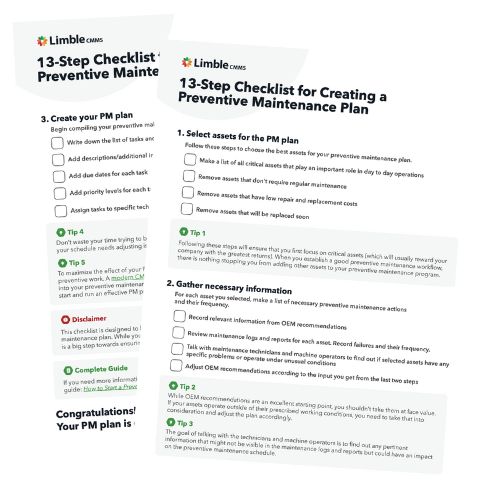
7 Benefits of Predictive Maintenance
PdM is one of the more advanced maintenance strategies that is widely used today, and it is growing rapidly.
That’s because with preventive maintenance alone, organizations run the risk of performing too much maintenance and wasting resources or not performing enough maintenance and having to deal with mechanical failure.
And with reactive maintenance, technical work is performed when needed, but inevitably comes with the high cost of unscheduled downtime.
The premise of predictive maintenance is that constant monitoring of an asset’s condition and performance allows maintenance to be performed when, and only when, it is necessary to prevent problems. Let’s dive into all the ways this approach can benefit organizations that use PdMs.
Fewer equipment failures
The ultimate goal of every maintenance and reliability professional is to avoid equipment failure. Monitoring the condition of equipment and systems on a regular basis can reduce the number of sudden machine failures by more than 50%.
Using condition monitoring techniques to inform your maintenance strategies, allows facility and equipment managers to get real-time data about asset health and take necessary action before the failure happens. A predictive maintenance program can reduce unexpected failure by up to 90% — nearly eliminating breakdowns.
Reduced MTTR
By avoiding machine failures, predictive maintenance also reduces the actual time required to repair or recondition plant equipment.
When condition monitoring sensors detect something wrong, technicians can fix the problem before the damage gets bigger. The average facility leveraging predictive maintenance can reduce the mean time to repair (MTTR) by 60%.
Increased asset lifetime
Leveraging machine learning to detect equipment and system problems early increases the service life of facility machinery by an average of 30%.
After implementing a predictive maintenance strategy, organizations reduce not only the severity of damages but also the rate of deterioration and defects. That’s because an issue in an inexpensive part can lead to damage in a vital part, which can make the asset lifecycle shorter.
Precise assets data
One of the benefits of predictive maintenance is the ability to use sensor data to make predictions about the mean time between failures (MTBF).
Having access to this data allows facility and equipment maintenance managers to determine the most cost-effective time to replace machinery. This avoids performing costly maintenance tasks that won’t contribute to the asset’s condition in the long-term.
Through the algorithm applied by technologies like CMMS software, managers can see when maintenance and continuing operation costs exceed replacement costs. With that, it becomes easy to make a confident decision.
Verification of a repair’s efficacy
Predictive maintenance sensors can be used to conduct vibration analysis, oil analysis, thermal imaging, equipment observation, and more. In addition, PdM sensors are also used to verify whether a repair was successful before the machine starts up again.
That increases efficiency by eliminating repeat repairs and additional shutdowns to address inadequate or incomplete repairs.
Improved workplace safety
Risk management and workplace safety are primary concerns for maintenance managers. Accidents in the workplace related to machine failure are not only dangerous but can also represent lawsuits with significant financial impact.
Early detection of equipment and maintenance problems reduces the risk of catastrophic failures, avoiding injury, and even death.
In fact, several insurance companies currently offer incentives for organizations that have an established condition-based predictive maintenance program in place.
Increased ROI
In addition to the money saved by reducing downtime, by avoiding complex machine breakdowns, maintenance teams need to invest less in maintenance tools and services overall. At the same time, maintenance technicians and managers are able to increase work productivity as they have more time to focus on other vital maintenance tasks.
With CMMS software leveraging internet of things (IoT) technology to read PdM sensor data, maintenance managers no longer have to spend precious time performing inspections or reviewing raw data.
Leverage the Advantages of Predictive Maintenance
A predictive maintenance program enabled by modern software such as a CMMS, is the best way to increase cost savings in a building or manufacturing plant. According to the Department of Energy, maintenance teams can expect an increase in production of 25% after implementing a predictive maintenance software and strategy.
Even with higher implementation costs than other maintenance strategies, it pays off in the long term.
The Essential Guide to CMMS
Download this helpful guide to everything a CMMS has to offer.
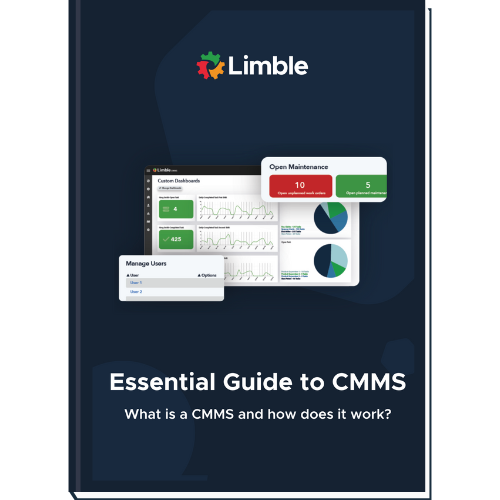