Lean Maintenance
Everything you ever needed to know about lean maintenance.
Lean maintenance is a strategy that aims to reduce waste and inefficiency in the management of physical assets. It relies on the application of lean methodology in the realm of asset maintenance and repairs.
Though many manufacturers focus more on the optimization of production using lean principles, it is arguably even more important in maintenance. This area is often a huge drain on any manufacturing concern, accounting for up to 40% of total production costs.
Waste in maintenance is a perennial problem due to a plethora of inefficient practices, such as:
- Excessive maintenance
- Unnecessary transportation of spares
- Walking back to a central location after every task to pick up new work orders
- Wasting time searching for tools and replacement parts
- Work order pile-ups due to poor inventory management
- Premature replacement of costly spares
- Delays and downtime due to slow processing or overprocessing
- Extra expenses to correct servicing errors and repair defects
Lean principles can make a difference here through tactics like smart proactive maintenance, digital work orders, improved leadership and worker training, Kaizen events, and distributed MRO inventories. We discuss all of those and more in the following sections.
Why should you apply lean principles to maintenance?
Using a lean approach in maintenance has the potential to bring massive improvement to vital aspects of manufacturing. Without proper maintenance, machines will break down and halt the production process – messing with your maintenance schedules and shortening the life span of your equipment.
Lean maintenance helps you do more (effective) maintenance work with fewer resources. Maintenance departments that are experiencing staffing issues can still deliver better equipment availability and reliability.
Through the implementation of lean maintenance, you are forced to identify and eliminate actions that waste your internal resources, improve inefficient processes, and speed up your emergency maintenance response.
The end result?
A streamlined maintenance process, and a significant reduction in the overall cost of maintenance, while delivering an equal or better service.
The Essential Guide to CMMS
Download this helpful guide to everything a CMMS has to offer.
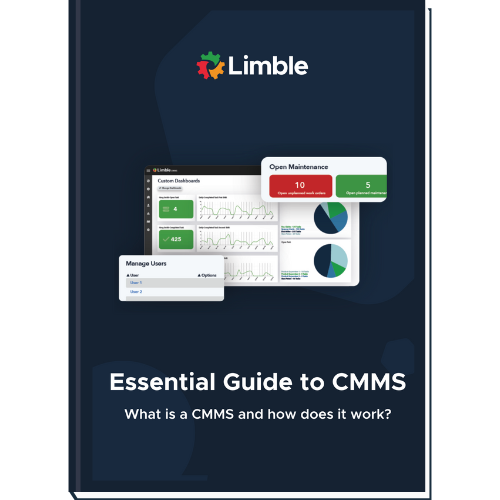
Prerequisites for running lean maintenance operations
Shifting to lean maintenance results in a major or minor overhaul of nearly all aspects of maintenance. To get started, you will require a mix of several systems, processes, and philosophies, which form the core of lean maintenance you can build upon.
1. A proactive maintenance strategy
Many manufacturers rely on a passive, reactive maintenance strategy to cut down on initial costs. But this outdated approach can prove to be more costly in the long run. Waiting for critical assets to fail before repair/replacement is inefficient – which is exactly what lean maintenance is trying to eliminate.
In contrast, a proactive approach aims to negate the problem before it gets a chance to fully manifest. With strategies like preventive and predictive maintenance, you can reduce the risk of sudden equipment failures and production delays. The focus is on establishing optimal servicing and replacement schedules for degrading parts.
2. CMMS software to streamline maintenance work
A computerized maintenance management system (CMMS) is the bare minimum to improve efficiency in everything from work order management, overall planning, maintenance scheduling, spare management, budgeting, worker management, and more.
Large industrial organizations looking to implement lean maintenance will often want to integrate CMMS with their existing ERP system. This forms a strong foundation for effective Enterprise Asset Management (EAM).
As it requires enhanced digital capabilities across the entire company, the EAM approach is viable for firms that have already adopted digital transformation. For an initial foray into lean maintenance, a cloud-based CMMS system can be considered an adequate starting point.
3. Up-to-date list of asset inventory
Having a fully updated inventory of all your core assets is mandatory for lean maintenance. You can use this to plan your repair schedules, spare part requisition processes, and allocation of maintenance teams.
A well-maintained asset inventory ensures that every machine or system is accounted for – failure in even a minor sub-system can bring down the entire production line. To prevent this, manufacturers need efficient and proactive maintenance of all assets.
4. Operator training and autonomy
Excessive oversight by maintenance managers often leads to slowdowns and inefficiencies within the maintenance system. Firms and managers need to embrace the concept of increased autonomy on the work floor in lean maintenance.
And this requires a team of highly trained, preferably multi-skilled repair technicians. Apart from basic training in the use of assets and heavy machinery, you will also need to train your teams to act decisively when problems arise.
Operators need a clear understanding of their duties and responsibilities within the maintenance process. This helps create a smooth flow in autonomous maintenance, where everyone is aware of what is required from them.
5. Leadership change and lean culture
Lean maintenance often requires a significant change in how systems are managed – instead of overt centralization of power, it focuses on increased autonomy at the lower levels. This cannot happen without a profound change in attitudes about the role of leadership.
In particular, you will have to address the changing roles/responsibilities of managers and supervisors. Instead of controlling teams, they will need to perform a more positive role in supporting those autonomous teams on the ground.
The system relies on a flatter organizational structure with fewer levels of management. The focus is more on the shop floor – not at the top and middle layers of management. This requires adequate preparation and planning but will inevitably lead to continuous improvement.
Advanced concepts and tools for developing a lean maintenance workflow
The lean approach in manufacturing has evolved over the decades into a rich and complex system of different advanced concepts, philosophies, and tools. In this section, we provide a brief introduction to important concepts that can be used to optimize maintenance work.
Total productive maintenance (TPM)
TPM is the bedrock on which the entire tower of lean maintenance stands. It is a holistic approach with one core aim – try to achieve perfect production with minimal breakdowns, delays, or accidents to your assets and equipment.
It emphasizes proactive maintenance by autonomous teams, who are fully trained and supported to the hilt by supervisors and top-level executives.
5S philosophy
There are five keywords in this process that all start with the letter “S” in Japanese – Seiri, Seiton, Seiso, Seiketsu, and Shitsuke. They involve the removal of unnecessary tools/materials, neat arrangement of tools, frequent cleanups, emphasis on a clean and perfect work area, and instilling such behavior into habits at the workplace. The aim of the 5s process is the creation of an efficient, clean, and safe workplace with minimal wastage.
5S example: Workplace scan diagnostic checklist
Distributed MRO inventory
Instead of centralized storerooms for spares, the lean approach emphasizes the creation of multiple store locations closer to the area of use. These stores will contain relevant, area-specific parts and tools. Lean stores require standardized materials and long-term planning/forecasting based on CMMS tracking data to ensure maximum availability without holding a huge inventory stock.
Just-in-time inventory management
Lean manufacturing is often called JIT manufacturing. In a maintenance context, JIT involves changes to inventory management. Firms will only place orders for essential spares or tools. It requires a well-planned maintenance schedule with in-depth knowledge about the condition of individual assets.
Successfully implementing JIT practices in MRO inventory management requires capable spare parts management software combined with predictive maintenance.
Kaizen events
Pioneered by Toyota, Kaizen in Japanese means “change for good” or “improvement.” In business, Kaizen events mean activities that are regularly conducted with the aim of continuous optimization of processes and systems. It tries to eliminate waste and redundancies by constantly looking for problem areas that can be further improved.
What this means in practice is that maintenance teams should regularly audit and update their processes and procedures to ensure continuous improvement.
Empowered, multi-skilled teams
Maintenance teams in a lean approach are expected to be autonomous, and capable of conducting all activities – administrative, logistics, regulations, and more – all within the strictly defined limits of the maintenance process.
Such teams require diversity, with membership drawn from multiple departments and specializations. Furthermore, to reduce waste and improve crisis management, an emphasis is placed on having members who are skilled in multiple areas of specialization. Achieving that requires well-thought-out training programs.
Work standardization
If you want to eliminate wasteful actions from your production floor, workers need clear and unambiguous procedures that show how to perform specific tasks – in other words, it’s time to standardize. This is exactly what standard operating procedures (SOPs) are for. They outline best practices for repetitive tasks of varying complexity.
Ultimately, SOPs help create a more autonomous working environment with less micromanagement and supervision.
RCM, RCA, and FMEA
Reliability-centered maintenance, Root cause analysis, and Failure modes and effects analysis are advanced concepts that can be applied in an effort to improve equipment reliability.
Their primary focus is on ensuring that equipment or manufacturing facilities continue to function reliably in their operating context. They are based on the realization that maintenance has to look beyond concepts like age and life expectancy of individual parts – to prevent asset failure, firms have to actively monitor the condition of individual systems and parts and assess their reliability.
By applying RCM, RCA, and FMEA, maintenance professionals can get a better understanding of different failure modes and causes, which enables them to select the right maintenance strategy and schedule for each critical asset.
How to set up a basic lean maintenance workflow
It takes time for an organization to fully embrace lean maintenance, even when you have all the above-mentioned ingredients in place. In the crucial early stages, it is better to take a focused and limited workflow approach. In other words, it is best to run a pilot project.
1. Choose a system to manage
The best option is to start small and pick a problem area within your maintenance wing, one with excessive wastage and costly inefficiencies. Trial your lean maintenance workflow here first, and use the Kaizen philosophy to improve and gradually expand to other sectors.
2. Create maintenance teams
Make a team of operators who work with the assets in the problem area you selected in the previous step. Try to include experienced maintenance technicians along with regular machine operators whenever possible. It can drastically improve their autonomous capabilities.
3. Assign leadership
Pick a maintenance manager – someone capable of planning and scheduling all the maintenance tasks on the shop floor. Along with an in-depth understanding of the assets, he/she should also have excellent organizational skills and training/experience in proactive maintenance.
4. Create maintenance schedules
Once all the pieces are in place, it is time to focus on the necessary maintenance tasks at hand. Scheduling is usually based on the concept of preventive maintenance. Use CMMS data along with inputs from any monitoring sensors you have on the assets to decide on the optimal maintenance schedules.
5. Test new procedures and workflow
Using techniques we outlined in the previous section, you should be able to develop new, more lean maintenance procedures. The team you established in the second step should try to follow the new workflow as closely as possible. The idea is to see if the changes are applicable in practice, and if things can be improved any further – before you standardize and expand lean principles to other parts of the production flow.
Want to see Limble in action? Get started for free today!
Create a lean maintenance department
Lean maintenance can be a handful, with a lot of complex concepts and tools involved. The comprehensive and intense nature of this approach is simultaneously its greatest strength and its biggest weakness.
Effective implementation of lean principles in production and maintenance can involve high upfront costs, which can have a dampening effect on the enthusiasm – particularly at higher echelons of management. It also demands profound changes across the organization, inviting pockets of resistance to change at all levels.
But in these uncertain times, manufacturers have to improve their standards of efficiency to stand a chance. Lean maintenance, being a vital prerequisite for lean manufacturing, will play a pivotal role going forward.