Heavy equipment is expensive to acquire and maintain. It is also critical for business operations. Since you have to have it, you need a good heavy equipment maintenance program to keep the assets in peak condition, increase their utilization, and extend their useful life.
In this article, we’ll guide you through the most important points you need to consider for the maintenance of heavy equipment. We’ll also outline how you can establish a heavy equipment maintenance system customized to your needs.
What can we categorize under heavy equipment?
Heavy equipment refers to specialized machinery built for a specific task or series of similar tasks. The term is broad, covering multiple industries and uses. Some examples include:
- Earthmoving machines like excavators, scrapers, or bulldozers
- Construction equipment such as cranes and modular transporters
- Forestry machinery, including chippers or stump pullers
- Semi-trucks and trailers
- Agricultural equipment such as tractors and combine harvesters
- Railway rolling stock
The term is less about weight than the specialized role for which the equipment is used. These days, such machinery uses sophisticated hydraulics, pneumatics, and electronics to operate. With the critical role of these machines, and the capital cost of acquiring and operating them, comprehensive and targeted maintenance is essential.
The benefits of proactive maintenance for heavy equipment
Establishing maintenance for heavy equipment involves investment, with some operators choosing to do equipment repairs only when it breaks. However, this is a false economy, costing those operators considerably larger sums in the medium and long term.
Studies suggest cost reductions between three to ten times when using preventative maintenance versus fixing it upon equipment failure. Let’s look at the benefits gained from regular, planned, heavy equipment maintenance:
Enhanced safety
As employers, we have not only a duty of care toward our workers; we have a regulatory obligation. When accidents occur, regulators immediately investigate the preventative measures and mitigations the employer had in place. One such mitigation is a well-thought maintenance plan to help ensure machinery cannot degrade to the point of causing injury or death.
Maintaining peak equipment performance
Hidden deterioration costs money: bypass valves not seating correctly, leaking hydraulics, dirty heat-exchangers working less efficiently, or dulled blades not cutting cleanly. All contribute to reduced operating capacity, increased wear, reduced efficiency, and reduced working life.
Each one of these effects sums up to reduced revenue or increased operating and capital expenditure costs.
Reducing the number of unexpected breakdowns
Unexpected outages from breakdowns erode company value. Deadlines are missed, and clients are disappointed. Employees become frustrated, potentially causing safety incidents.
Emergency repair costs can be two to three times the costs of a planned replacement due to expedited freighting of spares, after-hours callouts, and the hire of backup equipment. When maintenance is planned, it is carried out at a time and place of the operator’s choice, without affecting operations, and with all resources preplanned and available.
Extending equipment lifespan
All equipment has a design lifecycle, the achievement of which depends on carrying out recommended routine maintenance. The amortization of purchase costs across the equipment’s design life is the basis of rates charged by the operator. When equipment fails to make its design life due to neglect, costs are understated, and contributions to business earnings are lost.
There are numerous ways to extend useful life of heavy equipment, with proactive maintenance and operator training leading the way.
Greater equipment availability
Most heavy equipment is on an hourly rate. When the equipment is not operating, revenues reduce, and costs increase. When a job is costed as a lump-sum, breakdowns can impose emergency maintenance costs, extra hire costs, extended time-on-task, and reduced fleet efficiency.
The failure to achieve planned fleet reliability rates realistically means a business is losing revenue or carrying increased operating and capital expenditure costs.
Checklist for Creating a Preventive Maintenance Plan
Following a consistent Preventive Maintenance Plan can make life easier. Use this checklist to create your own!
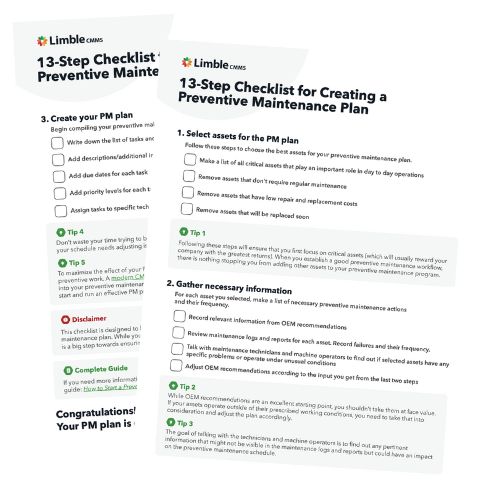
How to set up a proactive heavy equipment maintenance program
The following steps will guide you through the process of implementing a comprehensive heavy equipment maintenance program. The value you receive from the program will directly reflect the depth of detail you consider during the design and implementation phase.
Step #1: Choose a pioneer
If you have not operated a proactive maintenance program in your organization before, begin slowly. Select one piece of equipment for your pilot program. Once you have implemented the necessary systems to support that machine adequately, it is easier to replicate that template across your entire fleet.
Your selection should focus on an asset that has considerable operating life remaining, and it should meet at least one of the following three criteria:
- Its efficient performance is critical to effective operations
- It requires intensive maintenance
- It has a high failure or breakdown rate
Step #2: Baseline equipment’s previous operation
It is difficult to analyze the adequacy of a maintenance program without having historical operating data and diagnostics against which to measure interventions. Where possible, ascertain the operating cost, efficiency, troubleshooting data, availability, and spare usage of the machine.
Historical equipment performance and diagnostics, operators’ gripes, and maintainers’ experiences will all provide useful yardsticks against which to measure improvement. Once the maintenance program is in place and settled, you may compare the new data to the old to gauge the program’s effectiveness.
Step #3: Gather necessary data
When building a heavy equipment maintenance program, always begin with the original equipment manufacturer’s (OEM) data. All heavy machinery manufacturers will publish a list of recommended maintenance tasks and their intervals. Manufacturer’s recommendations will form the core of your maintenance program.
Next, consider the regulatory requirements you must meet in the jurisdiction you are operating. Most countries have specific maintenance intervals for lifting equipment. Health and safety legislation may impose specific requirements, as will environmental laws which require a regular monitoring of fluids, gasses, and emissions.
Lastly, you’ll need to consider what other maintenance tasks you need to add based on company requirements, aftermarket equipment installed, and your specific application:
- For instance, your company may use a GPS excavator guidance system fitted as an aftermarket product. The OEM of that equipment will have maintenance requirements that will form part of the overall machine maintenance program.
- Similarly, your company may require hydraulic and engine oil testing. The task of sampling the oils, sending them in for analysis, and recording the received results on a trend plot will become a planned maintenance task.
Step #4: Manage spares, consumables, and special tooling
Heavy equipment maintenance programs require certain spares, to be held in inventory or readily available at the jobsite, from third-party suppliers. Consumables and fluids will also need to be identified, as well as specialized tools needed to execute specific tasks.
When a maintenance period is planned, it is important that all spares, seals, fluids, and tooling are available to support the maintenance process. All specialist tooling that requires calibration should end up on your preventive maintenance program to ensure they are in proper working order before use.
Step #5: Decide on your management system
At this point, you’ll have a lot of data. You now need to decide how best to manage that data to call up tasks when due, raise the necessary worksheets, and capture the maintenance results. While you can use manual card systems or spreadsheets, they’re cumbersome, time-consuming, and require constant vigilance to ensure important things are not forgotten or missed.
A modern computerized maintenance management system (CMMS) allows the easy setup of initial data. It looks ahead for upcoming maintenance and creates a work pack for tasks to be completed during the maintenance period. Once completed, the data is updated to show the new status of the machinery.
Read our essential guide to CMMS to learn how a modern CMMS works and what you can expect from it. Or download the PDF version of the same article directly using the box below.
Step #6: Develop initial maintenance schedules
At this point, you need to accumulate all the data gathered above and overlay it to line up the tasks into obvious groupings.
The regular maintenance frequency for each task may be based on cycles, equipment hours, miles, calendar time, or a mixture of all. If you have condition-monitoring sensors installed on your heavy equipment, their pressure/temperature/vibration readings will drive a lot of your maintenance actions.
More advanced organizations with a lot of equipment data readily available can use Reliability-centered maintenance and Risk-based maintenance to decide which failure modes they want to track and which maintenance strategies they need to implement to make that happen.
Step #7: Monitor and adjust your heavy equipment maintenance plan
Your initial heavy equipment maintenance plan is not going to be perfect. Almost immediately, you will find that you need to make certain adjustments.
Some maintenance periods may have many tasks to be completed, while others have but a few. In this case, you can schedule some tasks early to reset when they’re due, smoothing the workload between consecutive maintenance periods and balancing downtime and resource requirements.
As you progress, you may find you complete some tasks too frequently. For instance, a filter inspection clean may be unnecessary at the initial frequency you selected. You might choose to lengthen the time between cleans to avoid unnecessary expense and time.
The opposite is also true. Some tasks may need a higher frequency due to the ways the asset is used or the conditions it operates in. If you encounter increased wear, failures, or downtime, it is prudent to increase the frequency of specific maintenance tasks.
Step #8: Roll out your proactive maintenance program to other assets
Once you have completed a proactive maintenance program on one piece of heavy equipment, you should have data proving the benefits.
With the template in place for your first machine, it’s not difficult to complete these steps for your other equipment. With a good CMMS, the process is as simple as loading the data and letting the heavy equipment maintenance software do the heavy lifting for you.
For more information, read our full guide on how to set up a preventive maintenance program.
The Essential Guide to CMMS
The Essential Guide to CMMS
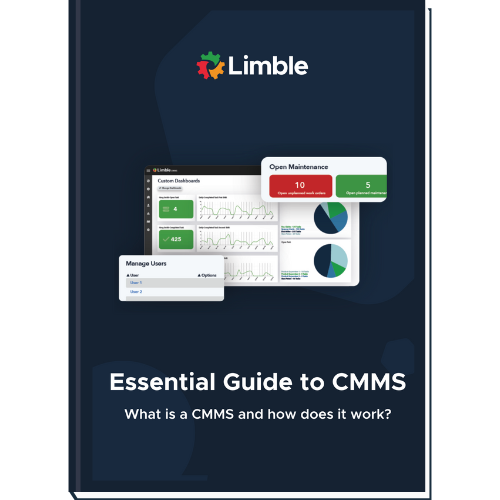
General advice for heavy equipment maintenance
The following tips will assist you in fine-tuning your maintenance program to ensure you extract maximum value from each maintenance intervention.
Use heavy equipment maintenance checklists
Without a degree of standardization and consistency, it’s difficult to maximize the payback from your regular maintenance. If one technician misses tasks while the other is diligently doing them, your maintenance is neither controlled nor effective.
Maintenance checklists and SOPs are a great way to standardize equipment management tasks and technician performance. They don’t need to be complicated – a simple checkbox to show task acquittal should be enough for a properly trained person.
For more complex tasks, checklists are a great way of highlighting the necessary steps of equipment service, while also adding a method to follow, the tools and spares needed, and providing a space for capturing who completed the task. It can also allow space to record observations that form a good narrative on the ongoing condition of the machine.
If you use a CMMS software, technicians will usually be prompted to leave completions noted upon closing WOs and PMs so those kinds of observations will be directly saved in the maintenance log for that specific asset.
Use defect logs for equipment operators
Place a defect log in the cab of all heavy equipment. A log allows the operator to note any concerns, leaks or deterioration, or breakages.
Defect tracking log template. Source: Free Excel Templates
Ensure the date is added and the entry initialed. Maintenance technicians can regularly check these defect logs to capture maintenance trends that may be developing. When planning the next maintenance day, all defects should be removed and added to the maintenance work pack for the technicians’ information.
All items in the defect log should be considered and addressed, either written off as an item to monitor, cleared as having been rectified, or pending awaiting tooling or spares. This control ensures the operators have feedback on issues they have raised, and no concerns slip through and come back to haunt you in the form of major service concerns.
If you are using a CMMS, all checked/addressed problems should be recorded in the equipment maintenance log so you have the complete maintenance history of an asset in one place.
An example of equipment maintenance log inside Limble CMMS.
Develop service packs for standardized tasks
A service pack is a collection of items needed to perform a particular task. For instance, if you need seals, some lubricant, and new fasteners to complete an inspection, put them all in a sealed pack with a discrete part number which relates to the task.
You can either have someone make up the pack before service day or create a part number and put them in stock.
When the task is due, the service pack is made available (along with maintenance tips and checklists if needed). Such a system prevents technicians from losing time by searching for those items before going out in the field.
Improve work traceability and accountability
Have the technician or operator who completes a specific task sign and date their task. Such traceability allows you to speak to the individual if something occurs in weeks or months ahead. It also allows for an easy follow-up if they were the ones who found defects during visual inspection or other maintenance work.
Ideally, you should know:
- Who performed each task
- How much time they spent doing it
- Which spare parts they used
Knowing those three things is essential for calculating your overall maintenance costs, and breaking them down into labor costs, parts costs, and costs associated with each vendor or asset.
Make sure your technicians give “completion time” for larger tasks. This doesn’t have to be about checking up on your workers. Alongside cost calculations, it’s very useful information that allows maintenance planners to schedule sufficient time for maintenance (by having a better understanding of the mean-time to repair for specific maintenance tasks).
Major components such as hydraulic rams, pumps, and electronic components will have model numbers and serial numbers. Track these to know what is on your equipment, what is in inventory, and what is out being repaired.
This data will help you decipher how long a component is in operation before repair is required. If one component fails more frequently than others (has lower MTBF), you can isolate that part and investigate the problem, fixing or replacing the component to achieve improved operational life.
Your CMMS is invaluable here as it automates a significant portion of the data collection and tracking process, as well as allowing you (at least in the case of Limble CMMS) to generate highly-customized maintenance reports.
Limble CMMS dashboard can be populated with all kinds of custom metrics that refresh in real-time
Centralize service information and tooling
Be sure that your technicians are completing the task to your requirements, not their idea of what is needed. There should be only one place to access the service information and the tasks to be completed. No photocopied sheets of paper in people’s toolboxes.
Similarly, don’t allow each tech to have special tooling they’ve made up to do a job. If it’s a good idea, get it made and make it available, so everyone can use it. If it’s not a good idea, it could damage your equipment or injure your technician.
Provide common data and tools for all to access and use. By controlling the information, the task, and the tooling, you control the safety and quality of work being completed. In this way, you optimize equipment life and maintain peak reliability.
Again, CMMS can be used as your asset inventory management system, keeping track of tools and equipment.
Gather relevant maintenance statistics and metrics
The aviation industry uses metrics such as mean-time-between-unscheduled-removal (MTBUR) and total-time-in-service (TTIS). They help you find parts that are not achieving their intended life or compare parts from different vendors to see which one provides more value for the $$ spent.
An added bonus of tracking such maintenance metrics is the ability to plan maintenance before failure. This helps you avoid costly breakdowns. Your CMMS will allow you to mine that data, reducing cost and optimizing equipment uptime.
If you have the budget for it and truly want to optimize your maintenance resources, you will have to install condition-monitoring sensors on your heavy equipment and implement strategies like CBM or predictive maintenance.
Should you outsource heavy equipment maintenance to a vendor?
There is a line. At one end sits the option of doing all maintenance yourself in-house, while at the other end you outsource all maintenance to a third-party organization. There are unlimited options between those two extremes, where you complete some maintenance and have some done by others.
There are many reasons for outsourcing.
- You may consider that maintenance is not a business you should be in or want to be in, as it’s not your core competency.
- Some maintenance may require very specialized tools or skills that you don’t wish to purchase or train your employees for.
- You may wish to transfer the risk of maintenance onto a third party who specializes in the task. With service level agreements (SLA) in place, if your equipment availability drops, so too does the maintenance provider’s revenue.
- You may wish to reduce your permanent workforce.
- You don’t have the facilities or ground space to carry out the maintenance.
- The cost of your employees doing the maintenance may be more expensive than having a specialized contractor complete the task.
Whatever your decision, there are some key issues to consider before taking the large step into outsourcing.
1. Retain your information.
If you outsource everything to a service provider, who owns all the data that they gather? Where does that data go if you wish to change maintenance providers? Will their control of your data restrict you from changing providers – effectively holding you to ransom?
If you do choose to outsource completely, it is advisable to require them to use your CMMS. For example, Limble CMMS allows you to keep all of your data, giving contractors limited access to the software. Work Orders can be sent directly to the vendor through our software (see how this works in practice here). The vendor receives the WOs, performs the work, enters time and spare parts spent, and closes the WO.
This way, you have insight into how the maintenance is being acquitted. You also may carry out audits at your discretion. Should there be an issue with your provider, it is easy to transfer control to a new provider who can continue without an interruption to your business.
If you selectively outsource, you need to be clear in your SLA what data will be provided, in what format, and the timeframe in which you must receive it. An example of selective outsourcing is an electrical maintenance group carrying out specialized tests and inspections or a heavy maintenance workshop carrying out your annual inspections. Require them to upload their data to your maintenance program.
2. Design a customized SLA to suit your needs
You can shift business risk onto a third-party provider through a well-constructed SLA. If you stipulate a percentage of equipment availability in the SLA, you can gain share, and pain share, if the availability is higher or lower. Your maintenance contractor gets paid less as your availability reduces and receives a bonus if it improves.
Be clear on your expectations concerning the use of maintenance information, the application of safety procedures, and the desired outcomes.
Outsourcing maintenance to a contractor does not absolve you of all responsibility, as you cannot delegate regulatory compliance issues. If your equipment is found to be in breach of regulations, the law will hold you to account. Implement a strong governance system to audit ongoing contractor compliance.
3. Price isn’t everything
Do not base your contractor selection on price alone. Competence, capability, compliance, and compatibility are all factors you should consider. The price of that more expensive contractor may pay back tenfold in increased uptime, reduced inventory, and extended machine life.
Be the manager you were hired to be and think about the big picture.
To recap
While businesses still exist that only do reactive maintenance, they usually do so for specific reasons. The majority of operators now realize that proactive maintenance is significantly more cost-effective, especially for heavy equipment.
While the upfront administration for implementation may seem prohibitive, you can gently introduce your business, machinery, and technicians to a new paradigm through simple pilot projects. Proactive maintenance coupled with a reliable and modern CMMS will drive greater revenue, greater uptime, lower inventory costs, and improved earnings.
If you’re interested in using Limble CMMS as the foundation for your future heavy equipment maintenance efforts, you can request a demo or start a month-long free trial.